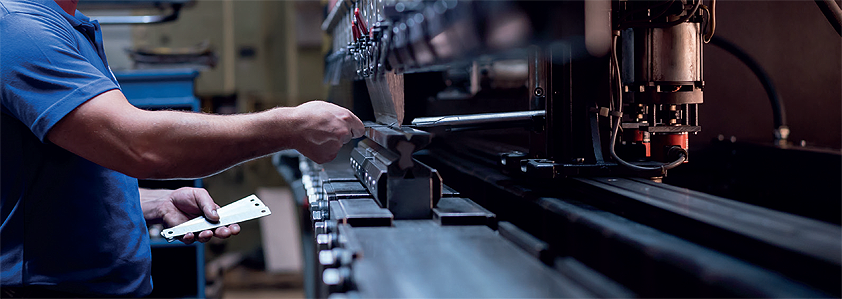
Know the rules
Following the UK’s exit from the EU, EU harmonized standards have simply been carried across as UK designated standards in order to maintain a single model. For example, the EU’s Machinery Directive has the same requirements as the UK’s new Supply of Machinery (Safety) Regulations.
This means that in the UK, procedures have changed very little from the EU’s CE marking structure. The UKCA marking is now required for new machinery placed on the market for the first time in Great Britain (England, Scotland and Wales), where the involvement of an independent certification body is required, but CE marking will continue to be accepted in Northern Ireland. The CE marking of course remains in the EU.
All machinery should meet relevant essential health and safety requirements (EHSRs). Machinery must be able to satisfy the EHSRs for any corresponding hazard which may apply to it. The EHSR requirements are wide ranging, taking into account potential dangers to operators and other persons who may be at risk.
A technical file for the machinery should also be available as it proves due diligence and provides evidence of compliance. It can be a traditional rulesrulespaper file, or stored electronically, with hyperlinks to documents. It must also be kept up to date as the product is adapted, which means that the technical file cannot be put away and forgotten.
The technical file must remain available for inspection by a competent national authority for a period of ten years. However, it does not have to include detailed information such as the sub-assemblies of the machine, unless a knowledge of them is essential for verification and compliance with the EHSRs.
When building machines, or when combining machines to produce an assembly of machines, it is easy to get things wrong, resulting in a project that requires a lot of rework and ends up going over budget or overtime. To this end, it is vital to ensure that the CE/UKCA marking is considered from the start. If this is not done, common problems that occur include:
- Equipment being installed before a final layout is agreed so that machines have to be moved and rework is required.
- Consideration not given to a safety related control system at the start leads to a number of problems when linking different machines with different performance levels.
- Not considering control system functionality so that feed conveyors are not stopped when a process is stopped, resulting in damaged products at best and injury at worst.
- Machinery that is not inspected before installation subsequently reveal non-compliances, resulting in disagreements about who pays to put it right – the supplier, the contractor or the user.
- Control colors not being agreed means that different suppliers may use different colors, leading to confusion. The European Standard allows for green, white, black or grey for ‘start’ and red, white, black or grey for ‘stop’, so even if the supply chain complies with the standard, errors and confusion can occur.
Equipment is often designed and installed with no thought as to what happens either upstream or downstream, or who takes the responsibility for which parts, and who takes responsibility for the final assembly. This can be exacerbated when equipment is sourced from outside the European Economic Area, or existing equipment is linked to new equipment.
When starting a project, it is therefore vital to decide who is going to take the responsibility for the CE/UKCA marking and lay down the ground rules. Decide what Performance Level the safety functions will be required to meet, using EN ISO 13849 and ensure all suppliers are aware of what is required. Make sure they all understand which EN Standards to follow, and that they have copies of the Standards. A good tip is to ask for sample declarations before deciding on suppliers, so that you can check to see if they contain the correct information.
When you issue purchase orders, ensure there is a clause about CE/UKCA compliance which states whose responsibility it is. A solution to this is to use a User Requirement Specification (URS) when purchasing new equipment, which will outline your requirements for the equipment supplier. Before accepting and paying for any machines, check that they meet the requirements of the order and also that they conform to the relevant directive. A pre-purchase audit is a useful system that can help machinery buyers ensure that equipment is both safe and correct.
Another consideration is that the EU’s Work Equipment Directive, implemented in the UK by Provision and Use of Work Equipment Regulations (PUWER), which requires the end-user to make sure the equipment complies with all relevant legislation. This means that in both jurisdictions the same rules will apply for designers, manufacturers, importers and end-users – everyone must understand their legal duties and responsibilities. If you are responsible for machinery building and safety, it is therefore vital that you are aware of what your machinery suppliers should be doing, which requires effective project management.
Paul Taylor
Paul Taylor is Head of Industrial Products (UK) at TÜV SÜD, one of the world’s leading experts in product testing and certification, with 150,000 product certificates in circulation globally. Its Product Service division analyzes over 20,000 products each year in Europe, Asia-Pacific and the Americas, using its technical expertise to help customers optimize market access.
TÜV SÜD’s Machinery Safety Division is the UK market leader in machinery safety, providing a range of services on a world-wide basis. It is also the official partner of the Process and Packaging Machinery Association on regulatory affairs.
www.tuvsud.com/uk