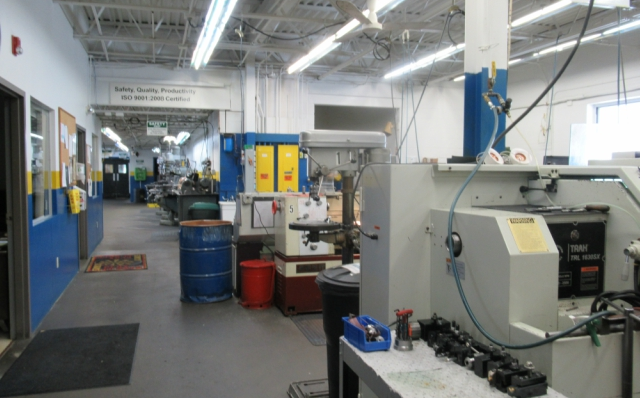
LillyWorks Inc.
Time is important, particularly in the manufacturing industry. Companies regularly evaluate what work they need to prioritize first, and LillyWorks can help them eliminate the guesswork in doing that with its Protected Flow Manufacturing software.
“It’s addressing a major pain,” Mark Lilly declares. “North American companies continue to struggle with delivering to their customers on time.”
Based in New Hampshire, LillyWorks provides solutions that help manufacturers with on-time performance and flow problems. Lilly’s father, Dick Lilly, started the company after a long career that included IBM and his own ERP software companies, including ProfitKey and Lilly Software, creator of VISUAL ERP, now owned by Infor.
Today, Mark Lilly is a partner and co-owner of LW Performance, LillyWorks’ sales and marketing arm. He says Protected Flow Manufacturing eases the pains its clients feel when having to call customers to tell them their orders will be late. This is often caused by the difficulty of using manual scheduling tools, like whiteboards or spreadsheets, or the complexity of Advanced Planning and Scheduling (APS) software within or outside of their enterprise resource planning (ERP) system.
When using a scheduling program, “The parameters have to be dead on,” Lilly says, explaining that ERP users have to look at multiple elements, including run times and inventory. But even after incorporating those, the schedule may still not keep operations efficient.
“Manufacturing companies are well aware that they’re in an environment of constant change,” he says. “Nothing is ever static. The priorities generated by any scheduling program are only as good as the last time it was run, which could be hours or days ago.”
The Right Order
A typical ERP Scheduling program tends to sort jobs based on due date, but the Protected Flow Manufacturing software uses a different method. “It focuses first on how and in what order you should execute your operations out on the shop floor,” Lilly says. This prioritization method starts with the creation of a framework for each job.
The Framework shows the steps needed to complete the job, a due date, and a buffer that sits between the end of the last operation and the due date. Lilly says, “[If] it would take me four days to get that work done, I’m going to create a 10-day buffer that sits in front of that. What that buffer is doing is protecting my due date.”
He notes that this allows the user to adjust to other manufacturing conditions, including other jobs being prioritized first or material or people issues. “It’s also nice to have some buffer in there for unpredictable events. As we know in manufacturing, stuff happens!”
The start date of the framework controls how much work you put in WIP. This is important. Putting too much work out into WIP clogs up resources, increases wait times and increases confusion about which job to work on next. Google “Little’s Law” and you’ll see that the less you put in WIP, the faster whatever is in WIP will flow through the shop. In this way, the start date of the framework protects you from putting too much work into WIP.
Once the job is released to WIP and as time goes by, the job is prioritized by the amount of buffer remaining compared to other jobs in WIP. The less buffer remaining, the higher priority. It’s that simple.
The Predictor – A Crystal Ball for your Shop Floor
“The Protected Flow Manufacturing software also has the ability to look into the future,” Lilly says. Thanks to a feature known as “The Predictor,” users can see a simulation of the execution methodology.
“It knows your capacity, your people, departments and groups,” he says. “It shows you which jobs it is going to run in what sequence and why, and if a resource becomes free what job it is going to select to be worked on at that future moment in time.”
The system can simulate hundreds of work orders in a matter of minutes and even warn the user about future problems. “You can see how often a job ran into another job or people constraints or why it is predicted to be late out in the future,” he says. “I can take that information and do something about it now before it bites me in the future. The simulation also gives me a method to commit a delivery date to my customer that I’m very confident of achieving.”
Bringing Benefits
LillyWorks clients such as Graphicast Inc. and Mid-Continent Engineering have enjoyed the benefits of the Protected Flow Manufacturing system. For example, the software allows users to control how and when to release jobs, manage their buffer sizes and prioritize based on buffer remaining, which often leads to shorter lead times and much better on-time delivery performance.
“A six- to eight-week lead time can become a three- to four-week lead time,” Lilly says, adding that some of its clients have been rewarded with premiums.
The system’s ability to hold the release of material until the release date also reduces the amount of WIP across a firm by at least a third. “A company with a WIP value of $500,000, for example, is going to see $125,000 in cash freed up,” Lilly says. “That’s a huge benefit.”
But the Protected Flow Manufacturing System also allows LillyWorks’ clients to save time. Some, he notes, have eliminated daily production scheduling meetings thanks to the software. “Everybody in the company – sales, production, engineering, management – is in agreement,” Lilly says. “You don’t need [to meet] anymore. The way jobs are prioritized allows everyone to agree what the most important job is to be worked on next!”
It also ensures workers are keeping focused on the right jobs. “It really drives the on-time performance well over 90 percent,” he says, noting that its clients typically enjoy a 60- to 90-day turnaround after implementing the system.
The Means to Manage
LillyWorks’ Protected Flow Manufacturing software can be implemented with any ERP system, Lilly says. “Currently, we have it connected to Epicor, IQMS, SyteLine and M1, so it’s really very open in that regard,” he says.
“As you continue to do your labor transactions and work orders in your current ERP, what we’re doing is culling work order, operation, and material information and showing you these priorities,” Lilly says, noting that he sees a strong future for LillyWorks with the system.
“It’s combining lean, theory of constraints and finite scheduling in a simplified way that makes sense for people,” he says. “We really see this becoming the de facto means to manage throughput flow and on-time delivery for manufacturing companies.”