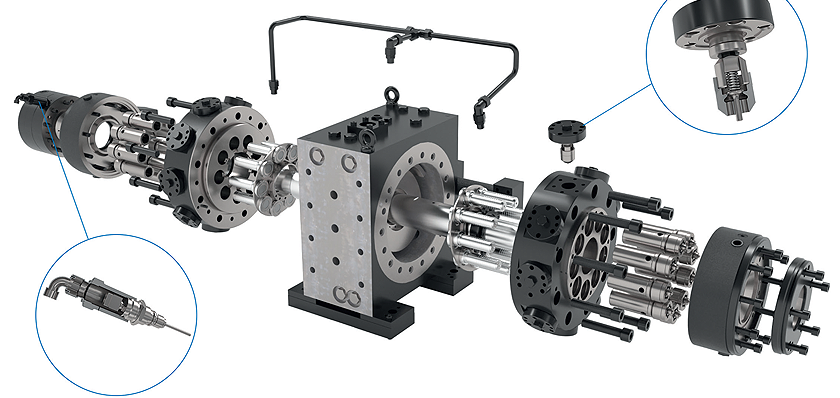
Oilgear
Calm under pressure
With a century of experience behind it, it is no exaggeration to say that Oilgear makes historically good pumps, valves and engineering systems, and that it has become a one-stop problem-solver
For the best part of 100 years, Oilgear’s high-performance fluid power solutions have proven themselves invaluable to the world’s most demanding hydraulic control applications. Founded in 1921, in Milwaukee, Wisconsin, the company continues to set the standard in industries requiring precise, high-performance hydraulic systems, with its products finding their way from depths of Earth’s oceans to the surface of our planet’s Moon.
“One of the things that Oilgear is recognized for today is its extensive – yet niche – product range, which is geared towards the sorts of high pressures that go beyond those that standard manufacturers within the hydraulic industry are used to working with,” states Chris Howie, Oilgear’s Vice President of UK and International Operations.
Although it is best known for its robust line of pumps, Oilgear also supplies cartridge valves, subsea pressure control solutions and electrical embedded controllers, and is a global provider of complex fluid power control systems. It also has a strong presence in forging and extrusion press control systems. “Where we really thrive is in the area of 450-to-1000 bar pressures,” Chris continues. “Unlike other suppliers who have a portfolio of ‘off-the-shelf’ products to choose from, we build our systems from the ground up. This gives us an unmatched level of understanding and know-how when it comes to the solutions we supply, and that gives our customers a huge amount of confidence that in Oilgear they have a partner that will be able to answer their specific needs.”
As a truly international entity, in 2020 Oilgear has global facilities in the United States, the UK, France, Germany, Spain, South Korea, China, Brazil and Mexico, which provide fully integrated manufacturing, service and training. It also has the ability to provide engineering support to customers in more than 50 countries.
Oilgear’s UK office can be found in the city of Leeds, where its European Specialist Pump and Valve Centre boasts modern manufacturing and test capabilities for multi-fluid/high pressure component development. It is in Leeds where Chris began his Oilgear career in 1988, before moving to South Korea in 1995, from where he became involved in the company’s Asia-Pacific dealings. Fast forward to 2018, and Chris was asked to again get involved with the Leeds operation as it made a transition away from being, what until then was, more akin to a cost center focusing on inter-company trading.
“In the last couple of years, our Leeds site has taken great strides to move towards being more of a profit center for the wider business,” Chris explains. “This has been achieved by ramping up the development of its product lines, examining Oilgearnew vertical markets, and driving innovation at ground-level, rather than waiting for this to filter down through our other global offices.
“Today, our Leeds center possesses full engineering capabilities – encompassing, mechanical, hydraulic, electrical and software engineering – operated by highly skilled individuals whose actions help to create the potential for our sales teams to go out and win business for Oilgear. Within the facility, we also have extensive, automated testing capabilities, including test stands delivering up to 500KW of power, and multi-fluid testing tools that allow us to carry out work on a full gambit of exotic oils for the chemical industry, power plants, and offshore and subsea mining customers.
“One of the exciting things we are looking to do in Leeds going forward is to utilize Cloud-based technology to give our customers a factory-live’ view of the facility so that they can get a birds-eye perspective of their respective product or system being assembled or tested. This will allow our customers to have unrivalled access to the development of their solutions, keeping them fully up-to-date with their progress up to the point of leaving the building.”
Industry 4.0
As Chris goes on to detail, these aren’t the only developments currently taking place within Oilgear’s Leeds site. “Recently, we have been looking closely at the integration of existing products with condition monitoring, so as to enable our existing product line to be industry 4.0 capable. This requires the incorporation of a lot of smart technology into our products, for instance, vibration monitors and casing drain temperature and flow meters. We are also working to introduce electronic traffic light warning systems to our products, which will be used to send messages to a users’ mobile device in real-time to alert them as to when a product is not being used optimally or may require a health check. These checks will then be able to be carried out either remotely or in person.”
Remote working
The drive towards condition monitoring and remote maintenance – which Oilgear began developing in 2019 – has been given a significant boost in importance this year as a result of the Covid-19 pandemic. “An understandable consequence of the emergence of Covid-19 is that a lot of businesses are limiting face-to-face contact, which would usually present a major challenge should one of our customers – for example – face a problem with their equipment,” Chris adds. “We are meeting this issue by wrapping a lot of our work around remote maintenance.
“Examples of this work include when we were contracted earlier in 2020 to carry out upgrades and maintenance lifts of Brayden Bridge in Great Yarmouth, which carries the A47 across the River Yare. We were able to maintain a limited presence on site, and through the smart, remote commissioning tools at our disposal, we were able to dial into them to get a live view of the bridge as we lifted and lowered it from 200 miles away in Leeds.”
Equally as impressive, was an instance that Chris recounted whereby a customer in India was experiencing problems with some of the pumps on their particular machine. While the customer was able to order and receive replacement parts from Oilgear, the company was unable to send over a representative to do the repair work itself. Oilgear’s answer to this was to set up a live video call to its customer so that they could watch a Leeds-based engineer with an equivalent pump in hand walk through the disassembly, repair and reassembly process.
New product development within Oilgear can also be found taking place across the Atlantic in the United States. There, at its Nebraska facility – where it specializes in the manufacture of smaller, more standardized products – the company has a new product range on the market called the XD5 series of pumps. This range offers lightning-fast control response on both low-viscosity fluids and standard hydraulic oil, and is designed to handle the most challenging environments. Meanwhile, in Michigan – where subsea and offshore products are created – the company has developed its BARS (Boosting and Regulating System) product. With its unique ability to maximize pressure capacity in accumulators without increased weight or pressure on the existing piping and hydraulic system, BARS is designed to increase the fluid pressure from the surface with its proprietary intensifier pumps to a maximum of 7500psi. Storing additional volume, it then regulates the downstream pressure back to 5000psi.
With the company marking its 100th anniversary in 2021, its future strategy involves achieving both organic and external growth. “In terms of organic growth,” Chris continues, “our sales team, led by UK and International Sales Manager, Stephen Raper, will continue to explore vertical market expansion, while also identifying sectors that we can gain greater traction in, whether that be the defence arena, in civil engineering, marine and offshore building, mining or the energy/renewables field. Meanwhile, in terms of our approach to acquisitions, an example of this saw the company re-acquire Andrew Fraser Pumps in July 2020, as part of our strategy to target emerging industries such as power generation and advanced renewable technologies, and we look forward to integrating that range into our wider portfolio. In this vein, we will continue to seek out potential acquisitions that will create synergies throughout the business.”
Oilgear
Products: High-performance fluid power solutions
www.oilgear.com