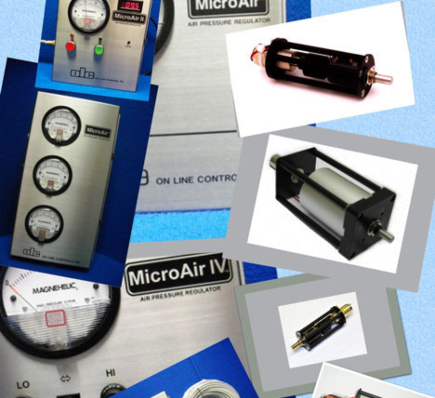
On Line Controls Inc.
On Line Controls is the leading manufacturer and supplier of ultra-low air pressure regulators and controllers for plastic tubing extrusion that require stable constant air pressure under 5 psi. “I’m most proud of the fact that our product is made to last more than 15 to 20 years,” says Kay DeWolfe, co-owner.
The Hudson, Mass.-based company was founded in 1980 to manufacture on line control systems for plastic tubing manufacturers. From 1981 through 2007, On Line Controls manufactured the first PC-based ultrasonic OD/ID/Wall measurement and control system, UltraGage 2000 and UltraGage 3000, for plastic tubing manufacturers.
Since then, On Line Controls has been focused on its two product lines MicroAir and Motorized Potentiometer, making great improvements in the quality of its products over the years. Motorized potentiometers are high precision proportional controls for automating analog-driven devices, and the line was purchased from ETI Systems in 1999 by On Line Controls. While they have not been used as often in new equipment since 2000, the company sells a lot of replacement units. “In the ’80s and ’90s, motorized potentiometers were used in printing presses, oil rigs, asphalt plants and simulators, to name a few, and they have all come back to us and buy replacement parts to keep their equipment running,” DeWolfe explains. “Today, we are the only ones who still make exact replacements.”
The Motorized Potentiometer line also includes Motorized Rheostats for higher wattages. Using the highest quality potentiometers, geartrains and motors made, and adding a slip clutch to protect the potentiometer end stops and allow for manual adjustment, helps make them the longest lasting motorized potentiometers on the market.
MicroAir Regulators are used for plastic tubing extrusion and make up a large majority of On Line Controls’ business today. MicroAir provides high precision control of tubing outside diameter by regulating air pressure to a set point during the extrusion of all types of profiles including medical, catheter and automotive tubing. “We make the perfect hole in the middle of the tube, which is a simplified way of explaining it,” DeWolfe says. “Our precision ultra-low pressure air regulators are used for precise air sizing and ovality of extruded plastic tubing. Air assist, support air pressure or positive air pressure are added to control the diameter and ovality variations during extrusion. The plastic tubing industry needs the air pressure to stay constant, otherwise a bubble could form or the walls could be too thin. We make sure the air pressure stays stable and precisely regulated.”
Built to Last
MicroAir Regulators series of precision air controls, ultra-low pressure air regulators and controllers are built to last. “We have been around for 35 years and set the standard for everyone else in the industry,” DeWolfe says. “Our products usually last 10 to 25 years and that’s what makes us stand out to people. Our reputation is built on that longevity.”
While the basic body design of MicroAirs have looked the same for the last 20 years, On Line Controls continues to improve upon the products internally to allow for greater precision and lower ranges to meet market demand. “Tubing has gotten smaller and smaller over the years, so people need more stability at lower ranges,” DeWolfe explains. “Medical tubing companies are making tubing with more than one hole called multi-lumen and we have one customer making 29 lumens. They are putting 29 holes in a tube that’s probably one-eighth of an inch. Multi-lumen tubes need one MicroAir for every hole they put in the tube.” On Line Controls can make its MicroAir units in Dual, 3-channel or 4-channel for multi-lumen tubing.
MicroAirs are used to make critical medical tubing, medical device, micro-tube, coextruded, catheter, multi-lumen, balloon, taper tubing, straws and small automotive tubing. The pressure range required can be below one-inch of water for the smallest tubes. Its manual MicroAir I and controller MicroAir II use a by balancing against a low tension spring and venting surplus air. The MicroAir IV provides instantaneous response to changes in pressures, required for bump or taper tubing and can also be controlled with a 0- to 10-volt input from the PLC or other extrusion line control system. “Both our low-tension spring models and our high speed linear solid-state model offer some of the highest flow rates in the industry,” DeWolfe notes.
All of On Line Controls’ products are custom made at its headquarters and delivered to its customers worldwide. “Everything is custom because you need to know the range each customer needs and if they need additional options, such as a digital display or output option,” DeWolfe explains. “Depending on the requirements, model and parts in stock, delivery can vary from one week to three months.”
Moving forward, On Line Controls will continue to rely on its reputation and marketing efforts to increase its market share. The company this year attended MD&M Show in Anaheim, Calif., and plans to return in February 2020. At the show, DeWolfe says networking has been phenomenal for business and even included the hiring of a new representative for Mexico.
“On Line Controls has been growing since 2007 when myself and the company’s vice president, who has more than 30 years of experience with our products, took greater control of the company before purchasing it in 2016,” DeWolfe says. “Our goal is to expand the sales of our products globally, find new industries for our products and develop new product lines.”