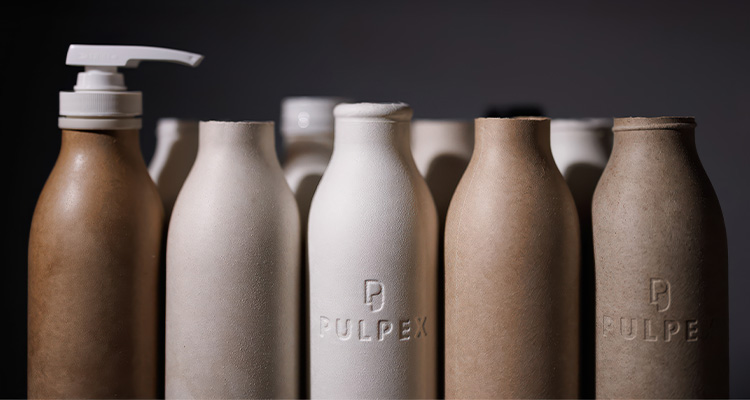
Packaging pioneer Pulpex is ready to shake up the industry with its planet-first technology
Driven by scientific curiosity and a planet-first approach, Pulpex offers a safe, sustainable alternative to glass and plastic packaging. The company has been developing its cutting-edge products for several years and will soon begin large-scale production, as Managing Director, Scott Winston, begins: “Pulpex started its life within Diageo, the alcoholic beverage giant, and it’s my background in leading a team in Commercial Science that led me there. Our team worked on long-term growth strategies for drinks brands within the beverage industry. We saw science as a driver of growth, rather than a fixer for optimization. One of the big problems we looked at, all the way back in 2018, was this question of glass alternatives.
“Glass packaging is obviously very popular in the beverage market, but it’s not always safe or sustainable. With glass being banned from most outdoor events, we decided to investigate the production of a fiber-based bottle. We focused our efforts on research projects through experimentation over the following years to find a suitable alternative.
“At first, this was internal to Diageo partnering with Pilot Lite Group to determine the best and most agile path to scale. Then, in 2020 we decided to move the technology out to a new company called Pulpex. As a natural evolution, this meant we could open ourselves up to wider markets and provide broader access to the technology behind our product.
“Once we’d struck out on our own, we built a core team of experts, from scratch during the pandemic, to help scale up the operation. We invested in developing new technologies, as well as a new research and development facility, and that’s how we got to where we are today. We have a team of around 50 staff members and our first factory is currently under construction in Glasgow.”
Designed with clients, consumers and the planet in mind, Pulpex offers something new to the commercial packaging industry. As Scott affirms: “There are three critical elements to successful packaging production. It must carry brand equity and semiotics which are recognizable to consumers. The second aspect is that it must be dual point functional. That essentially means it must be up to specification, balancing functionality with other values such as sustainability and convenience.
“The final key ingredient is circularity. This is to do with the products’ end-of-life. If you look at most packaging, they hit two out of three, but this third element is where a lot of our competitors fall. There’s just not enough capacity in the recycling chain to move everything through. There’s a surplus of plastic and glass where you don’t necessarily need or want it. That’s what makes our packaging unique. It’s designed using fiber-based technology, for which we have a much stronger recycling infrastructure.
“Our packaging is intrinsically strong. It doesn’t have any split lines or weak points, which is very important in terms of functionality. As long as the top load and side load of the structure is correct, it’s suitable for most commercial production filling lines. This has been key to our success, as a lot of businesses face pressure to take up sustainable alternatives but are struggling with the financial demands should they be required to replace their current processes. Our fiber-based packaging is much easier to adopt, as it is compatible with clients’ existing manufacturing operations.
“Our fiber molding technique builds the perfect shape and is completed with applied barrier coatings. This means we can offer functionality, shelf life and quality, while also being a more sustainable packaging solution. We optimize for use up to 24 months post filling, meaning it’s best used for fast-moving goods. We’re not looking to replace all glass and plastic – glass is suited to luxury, long-life goods and aggressive substances are better suited to plastic containers. That being said, there’s a lot of opportunity for fiber-based packaging when it comes to rapid consumption products.”
After years of research and development, Pulpex is primed to break into the industry in a big way, as Scott discusses: “Our short-term priority is getting our factory in Glasgow up and running with the aim of being operational by the first quarter of 2026. That’s no small task, as with any first-of-a-kind facility we’re at the beginning of our journey. We need to get the technology deployed and in place, but we’re very confident that our products will flood into the market once that happens.
“In the meantime, we’ll continue to produce packaging from our research and development center. There’s also a lot of new product launches coming out over the course of this year in various categories, which will offer something new and exciting to the UK market.
“Looking further ahead, our priorities will be driving scale and becoming a major player in the packaging industry. We’re constantly in conversation with potential manufacturing partners across the globe. We have frequent visitors to our research and development center in Sawston so they can learn what we’re all about and be ready to deploy in their local markets. It’s a hugely exciting time and I can’t wait to see how Pulpex evolves,” he concludes.