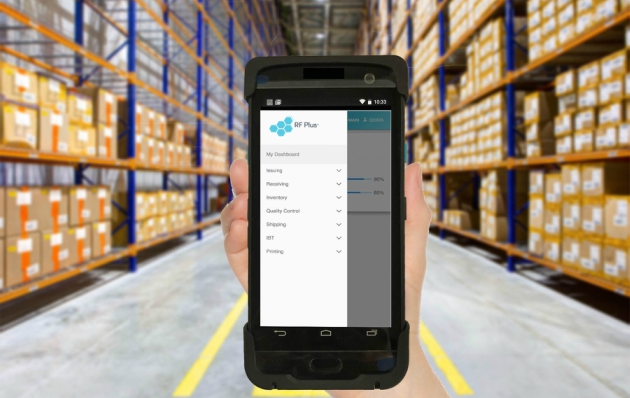
Overcoming ERP Inventory Management Limitations with RF Plus™ for Manufacturers
Are you using one of the many ERP systems purpose built for manufacturing companies?
These systems used by tens of thousands of companies around the world have deservedly earned a stellar reputation for planning, managing production and tracking costs. They were, however, not created to manage inventories.
One of the underlying principles of a manufacturing ERP is the premise that you order materials by the job. You buy just enough materials to make the product and you ship all production to the customer, thus leaving very little inventory to track.
However, over time due to growth, a manufacturer goes from being made-to-order to a made-to-stock producer. Bigger and more frequent orders, creates the requirement to hold inventories due to supplier lead times and customers start giving you delivery schedules around shipments. Suddenly you have inventory and lots of it, but your ERP can’t adapt to this new reality.
While having lots of inventory isn’t a bad thing, it becomes a problem if you can’t track it. Typical symptoms: production delays and bottlenecks, short shipments to customers, increasing inventory write-offs, and customer penalties related to delays and/or label non-compliance.
To compensate for this lack of visibility and control, the answer is to add more people and paper-based processes. And because this system is not scalable it’ll work up to a point – typically about 25 percent more volume. After that, you’re back to square one with more people, more inventory and more inventory management problems than ever before.
This is why we created RF Plus™, which addresses the materials management blind spot that manufacturers inevitably face as they grow. While RF Plus has dozens of features that represent best material management practices, here are our top seven:
1. Data Capture – Barcodes remain the fastest and most accurate form of data entry at the lowest cost. Most popular barcodes are 1D symbology’s like code 39 or UPC and typically are used for part numbers and lot codes. Beyond ID barcodes, there is the 2D version, which can encode as much as one page of information. One manufacturer puts 2D barcodes on their finished product which contains the complete bill of materials and work order number. Data capture is not limited to scanning. With our latest version of RF Plus, you can take pictures or video associated with any action like inbound receipts/shipments. These can then be sent with shipping documents or used as evidence of damage on inbound goods.
2. Real Time Transaction Processing – The most critical pieces of information needed in a manufacturing facility is the arrival of raw materials, usage of raw materials and the shipping of finished goods. If you lack real time data, your warehouse team will be spending several hours a day looking for product, have too much money tied up in excess stock, and you’ll be disappointing customers with sudden stock-outs that are not reported by your system.
3. Bin Locations – It is not uncommon to see a few locations like main or finished goods as the only storage locations in the warehouse. You’re not going to find anything quickly when you have these super large locations. We advocate using the acronym ZABLB (zone, aisle, bay, level, bin) to properly identify all the locations in your warehouse. Furthermore, you should designate location types in the warehouse such as bulk, production, overstock and pick areas.
4. Inbound Processes – The arrival of goods triggers a series of processes including labelling, inspection, PO updating and put away. Unless your supplier is amenable to printing your barcoded part ID on your purchased parts, RF Plus has an alias function that supports the cross reference of supplier part ID to your own part ID such that you can scan supplier barcodes. For putaway, your inventory management system, when required, should also take into account FIFO (first in first out) and be able to direct your staff to put product into pick or overstock locations.
5. Trace – Chances are if you are not using barcodes, you’re not using trace information such as lot or serial numbers to further identify your materials. This is essential for basing inventory turns on FIFO or providing customers with traceability information. Furthermore, you may have to track multiple trace fields. If you ever have to add additional trace fields, RF Plus is able to automatically accommodate that new field.
6. WIP (work in progress) Tracking – Typically, during the creation of a finished good, parts waiting for the next operation can’t be taken to the next department because they’re backlogged, or the next operation isn’t scheduled until next day. These parts which are not officially a raw material or finished good are put away to a location which is not recorded anywhere except someone’s memory. RF Plus tracks these “in between” goods and this feature alone was sufficient for a recent customer to purchase the product.
7. Cycle Count – Less than 50 percent of companies do daily cycle counts. A cycle count benefits the business because it ensures location and quantity accuracy. If you are like the typical warehouse, you will avoid losing upwards of two hours per day looking for parts. As for setting up cycle counts, RF Plus can schedule those counts. Just identify your ABC product categories and how many times per year you would like those categories counted.
Like any other endeavor worth doing well, material management should be part of your continuous improvement program. These seven best practices along with RF Plus represent a great start.
Jeff Lem, MBA, P.MM, is president of Portable Intelligence Inc.