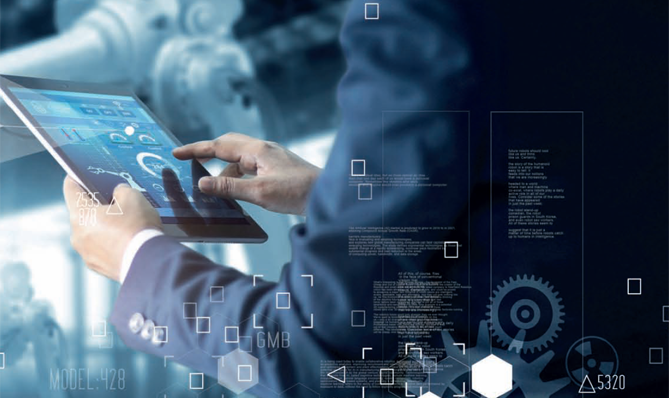
Protecting production
Industry 4.0 has been described as a revolution but, in reality, it’s been slowly transforming the manufacturing world for the best part of a decade. The installation of connected devices, cameras and sensors into production lines and on to the factory floor has been bringing traditional IT and operating technology (OT) together.
A survey, conducted by PwC, found that 85 per cent of businesses expect they will be deploying these Internet of Things (IoT) technologies in their operations by the end of 2020. But over the last few months, the appeal of the digitally enabled factory has grown further.
IoT is providing greater scope for remote monitoring which promises increased business intelligence and operational efficiency – leading to greater productivity and profitability. But with social distancing now also a crucial consideration, this technology is helping to keep factories operational in difficult times. IoT enabled OT is helping to increase automation, introduce advance robotics and deploy sensors for proactive maintenance – all of which reduces the need for human presence on the factory floor.
To realise the benefits of Industry 4.0, however, we must first acknowledge and overcome the challenges it brings. Cyber security is cited as one of the main reasons why 76 per cent of IoT projects fail – and if it’s not addressed it will pose a significant barrier to those entering this new age of manufacturing.
Manufacturing OT has not previously been exposed to pernicious security threats that the IT world has been battling for decades, but it now is. So, how should manufacturers approach cyber security during this industrial revolution?
Cyberattacks in manufacturing
If manufacturers become increasingly reliant on automation, there needs to be a recognition that a compromised IT system could easily lead to disruption on the production line. A major incident could have a nasty knock-on effect to a global supply chain, which is already suffering from the Covid-19 pandemic. It could bring manufacturing to a grinding halt and create even greater backlogs and uncertainty.
The growing prevalence of IoT increases the potential attack surface area available to hackers and therefore, the potential for large-scale disruption. This was evident when Renault-Nissan was forced to unplug its IT systems after a global ransomware attack infected its network, forcing stoppages at several international production sites.
The harsh truth we have to face is that it might not be possible to stop every attack. However, we can limit the damage, especially if we make the assumption that a breach is inevitable and plan for it. Known as a ‘Zero-Trust’ approach, it encourages companies to increase their layers of defence.
The zero-trust philosophy
Rather than rely on a ‘castle wall’ approach, zero-trust is about segmenting your systems, and creating more obstacles for hackers to get over if they breach that initial external barrier.
This will hinder the lateral internal movement of hackers within a compromised system, which we know can be so destructive – as a recent ransomware attack on a US gas pipeline demonstrated.
In this case, the operational network was connected to the IT office, meaning the attack spread quickly. But with zero-trust, preventative measures slow down the hackers, giving IT teams the chance to kill off an attack before it can infiltrate multiple areas.
Prevention in zero-trust
Of course, you still need a firewall in place. Organisations must put several protective measures in place and unified endpoint management (UEM) is a good first step to developing an effective security architecture. UEM technology provides an organisation with the ability to enforce the compliance of all endpoint devices, offering monitoring protection throughout the network.
We can then treat each segment within the network viewed as an independent and potentially insecure unit. A useful analogy is that of house where both the external and internal doors are locked. If one room holds particularly sensitive information – i.e. your IoT data – then limit the number of people with keys to that room.
Investing in multi-factor authentication technology will help secure the house. Together with conditional access policies, these technologies provide layers of barriers to hackers. They require multiple checks of the user, ensuring only those who have permission to access certain areas can do so.
Embracing the smart factory
IoT technology won’t replace the role of humans entirely. Thankfully, we are still needed to interpret and act on the information provided. It does improve our ability to increase social distancing though – which makes it an attractive proposition in the current climate.
This will likely usher in the age of the smart factory faster. But, as it does, manufacturers must ensure they stay in control of their production lines and overcome the challenges this tech brings. In this respect, cyber security should be viewed a crucial enabler for Industry 4.0.
By understanding the risks to their business however, and embracing a zero-trust approach, organisations large and small can put the right measures in place to protect connected factories and future production.
Mark Lomas
Mark Lomas is technical architect at Probrand, a leading technology services provider. It delivers IT products, managed services and solutions to over 3500 clients across small to medium sized businesses and all areas of the public sector. Probrand helps customers procure IT more efficiently through its ground-breaking marketplace, and deliver IT solutions, Cloud and managed IT services that run, manage and transform business operations.
www.probrand.co.uk