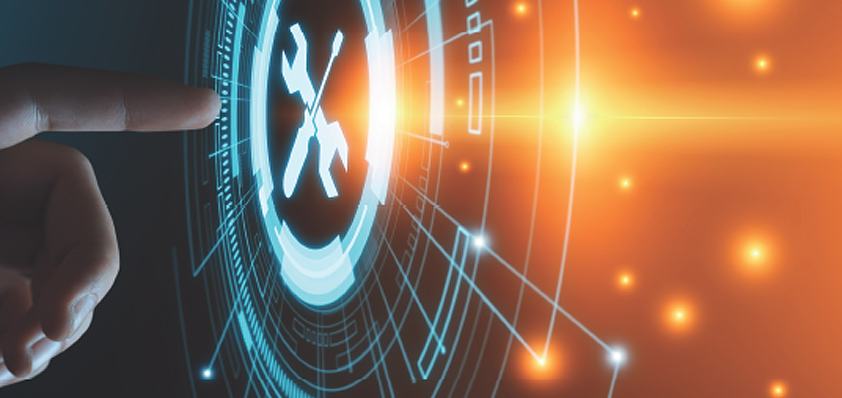
Rapid advances
The pandemic has been profoundly difficult for the manufacturing sector worldwide. In addition to contending with concerns about employee health and safety, manufacturers also have had to face various other challenges, including plant closures, gaps in supply chains and slowed economic activity. For many, applied machine learning (ML) has assumed a crucial role in bolstering resilience. Here’s a sampling of how ML applications are being integrated to improve business operations like machine maintenance and a look at what may lie ahead for ML in the manufacturing environment.
Predictive maintenance and safety
Manufacturers know that machines need regular maintenance and that maintenance always costs less than repair. However, disruptions from the pandemic have made it difficult to keep up with scheduled inspections and servicing. Fortunately, ML-augmented applications can help manufacturers monitor the condition of equipment remotely, using the data they collect to determine how to optimize maintenance. Image analytics, for instance, allow manufacturers to extract meaningful information from sensor displays and then make the decisions necessary to reduce downtime and maximize the longevity of assets. In other instances, drones equipped with thermal imaging cameras have been used to take thousands of images per minute, which are then processed to make predictions around potential machine failures. ML applications like these eliminate steps that used to depend on human intervention and can help improve operational efficiency, enhance near real-time decision-making, reduce costs and mitigate risks for employees.
It is also possible to combine sensors and advanced (multi-disciplinary) models to create ‘digital twins’ of machines or systems. These digital representations can then be used with various inputs, and the outputs produced can provide insights without having to
incur test costs of the actual physical system. Although digital twin technology is still in its early days, the pandemic has accelerated the push to refine the models and data acquisition capabilities required for these kinds of usable simulations. It is now easier than ever to simulate and optimize a shop floor without having to physically move machines around the plant.
Supply chain rebalancing
In a way, supplier networks need regular monitoring and upkeep just as machines do. Near real-time sensing for supply chains could alert manufacturers of impending inventory vulnerabilities and how those gaps could be filled. ML integrations are already helping many manufacturers better understand their supplier networks and the impact of potential disruptions. To be the most useful, this type of predictive crisis management requires data collection across all of the organizations involved in the manufacture, packaging, transport and distribution of the supplied goods. That, in turn, raises complex issues related to the sharing of data between manufacturers and their 3PL partners, usually across international boundaries.
Can hurdles to this type of co-operation be overcome? The pharmaceutical industry, for example, could leverage decentralized ledger technology to boost data sharing across the supply chain for production and supply of SARS CoV2 vaccines. However, sharing data in competitive markets remains subject to strict rules, siloed organizational structures and much skepticism. These concerns will limit how much information manufacturers have available for integrations and valuable algorithms that can apply inventory levels for multi-criteria decision-making and supply chain rebalancing.
Robotic Process Automation (RPA)
Robotic automation was introduced to assembly lines decades ago. Now, manufacturers have begun implementing robotic process automation (RPA) to improve other business operations, as well. For example, automating routine—and traditionally manual—tasks such as purchase order management, bill of material generation and report filing means those activities can continue even if back-office employees are unable to work. That helps maintain workflows, reduce processing times and improve productivity.
Likewise, manufacturers are expanding the use of autonomous mobile robots (AMRs). Today’s sophisticated ML algorithms enable these unattended bots to not only perform tasks, but also sense and respond to their environments in real-time. That means an AMR tasked with moving goods on the shop floor can detect an obstruction and then make an informed choice about how to handle it. AI capabilities like these are making AMRs increasingly indispensable for use in hazardous conditions, to fill in gaps caused by diminished headcount and when throughput needs to be ramped up to meet increased product demand.
Because ML applications like PdM and RPA have proven so effective in helping manufacturers cope with the disruption and uncertainty of the past year, advances in this field are happening at a more rapid pace than ever before. These technologies will continue to evolve, enabling manufacturers to maintain their competitive edge in a global marketplace that is sure to demand adaptability and resilience long after the pandemic ends.
Jean-Paul de Vooght
Jean-Paul de Vooght is Senior Director, Client Solutions, at Ness Digital Engineering. Ness is a digital solutions company with product engineering in its DNA, backed by a global collective of software engineers, data experts, user experience designers and innovators. Combining core competence in engineering with the latest in digital technology, it builds customer-facing platforms and software products that help businesses thrive in the digital economy.
www.ness.com