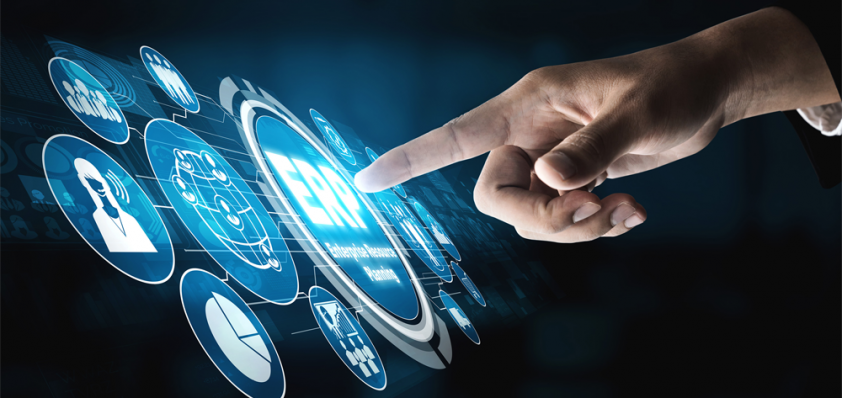
Relieve the burden
Few ERP solutions are tailored for the engineer-to-order (ETO) manufacturing space. Even fewer contain a build-to-print feature which allows manufacturers of custom-designed products or parts to advance quickly and profitably. Build-to-print is a process in which a manufacturer produces products, equipment, or components according to the customer’s exact specifications. Typically, an engineer provides drawings, and the manufacturer is responsible for producing the part or piece of equipment to spec, using the correct materials. The design specifications often include performance and quality requirements. Build-to-print falls under the general category of contract manufacturing and is occasionally referred to as build-to-suit.
Companies engage a custom manufacturer for a build-to-print project when their engineers need components which are not their specialization or when they do not have the capacity or equipment to manufacture. Frequently, an OEM will have the capabilities onsite to execute most of a design, but will find it less expensive to outsource certain components that fail to align with their staffing and equipment resources. Enabling companies to keep operations streamlined and cost-effective can only happen in ETO manufacturing with build-to-print functionality; it allows companies to specialize in low volume, high mix contrast manufacturing.
Specialties requiring this solution include precision component manufacturing, sub-assembly manufacturing, and end-product manufacturing. It is critical that full quoting capabilities are included in built-to-print modules. Quotes must be generated via the process flow estimations for individual parts (entering estimated times, setting markup/margin, time/material jobs, or even just a user specified cost). The build-to-print capability is especially useful when a company is not purely a “contract manufacturer” nor an OEM.
Manufacturing engineers are not happy
While the Bureau of Labor Statistics (BLS) estimates a ten percent (ten percent) YoY (year over year) growth rate among industrial engineers the rapid attrition rate is equally high; that equates to 100 percent attrition in a decade. Nowhere is the dissatisfaction and attrition of industrial engineers as great as the engineer-to-order manufacturing space.
With all the permutations inherent in the ETO manufacturing process, it may seem counterintuitive that so many are bored and exhausted. The fact that no two customers or products being manufactured are identical would seem to alleviate the possibility of boredom. In fact, the variety of engineering tasks would seem fun and interesting. These one-of-a-kind engineering and production elements would suggest an interesting and challenging engineering career.
The exhaustion in the ETO manufacturing process is not from the engineering and design creativity needed, but rather the antiquated tools, disconnected technologies, and need to constantly create production work-arounds to offset and compensate for system inefficiencies. Industrial engineers named ill-suited ERP (enterprise resource planning) solutions as the main culprit, triggering as much as 30 – 40 percent of their work time fixing and overcoming limitations.
The cost of frustrated industrial engineers
These are highly paid industrial engineers who spend their time sending post-it notes to purchasing, operations, and production. They are frequently blamed when a production schedule is missed, yet frequently senior management fails to take responsibility and accountability for providing the wrong tools to get the job done efficiently.
Quality impacted when ERP fails industrial engineers
It is estimated that hiring and training a replacement industrial engineer will cost at least $40,000. Just keeping industrial engineers equipped with the proper ETO ERP solution will allow for happy and engaged workers. It is up to employers to identify disengaged workers and find ways of reinjecting purpose and interest into their jobs. Failure to do so puts manufacturers at the risk of high turnover rates. Boredom is a sign the engineering staff is already searching for a new job or employer who understands what is needed to maximize creativity and efficiency.
Not burdened with workarounds required due to poor integration between SOLIDWORKS and an antiquated ETO ERP solution, industrial engineers confer with clients about product specifications, vendors about purchases, management personnel about manufacturing capabilities, and staff about the status of projects.
Andrew Schutte
Andrew Schutte, General Manager at COUNTERPART ETO ERP, has been mechanically inclined from a young age. Growing up in his father’s machine shop he was provided a valuable hands-on education of machining, fabrication, and mechanical design throughout high school. He moved to designing automation assembly equipment and machine design supporting the automotive, office furniture, medical equipment, and consumer product industries. Follow on Twitter @CounterpartErp, call (616) 738-8922 or visit http://counterpart-erp.com/.