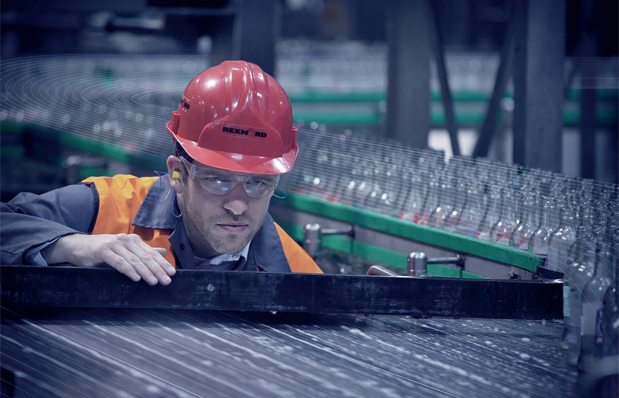
Rexnord FlatTop
Moving forward
As a global leader in conveying components manufacture, Rexnord FlatTop is committed to driving efficiencies through its customers’ facilities with a focused and clearly defined innovation strategy.
Headquartered in Wisconsin, Rexnord is a global leader in delivering high quality products under two strategic platforms: process and motion control, and water management. Employing around 8000 people around the world and with over 120 years of experience, Rexnord has established for itself a robust reputation for delivering innovative, high quality and durable products. Through a programme of continuous improvement across product development and manufacturing processes, the company aims to consistently create superior value for its customers, shareholders and associates.
Rexnord’s FlatTop division designs and manufactures standard and bespoke conveyor systems for the food and beverage, industrial and automotive markets. The company supplies OEMs, end-users and a network of distribution partners around the world and is currently experiencing significant success as its core markets grow. With global population rising and a middle class expanding in many developing countries, the global food and beverage industry is currently experiencing a period of positive growth, as to is the automotive industry.
“We listen to our customers and their voice is number one,” begins Rexnord VP and Business Manager for FlatTop, Rick van den Berg. “We are also very capable of problem solving. With such a vast bank of expertise and experience we have a reputation for never walking away from an issue.” Rexnord FlatTop places itself firmly in the driving seat of the conveyors industry by delivering the majority of significant innovations and retaining technology leadership across the world. Innovation focuses revolve around four main drivers: safety, productivity, energy saving and water reduction. In a push to deliver this to the market for the last three years Rexnord FlatTop has been developing its Engineered Sustainability product programme.
“Engineered Sustainability is a product programme focused on developing and launching solutions around these four central topics,” explains Rick. “It is a product programme that enables our customers to utilise durable conveyor systems with components that guarantee optimum product handling solutions, without compromising the ability to meet our customer’s targets of safety improvements, productivity optimisation, energy savings, product protection and water minimisation.” By working closely with its customers Rexnord FlatTop deploys its skilled engineers to help obtain low Total Cost of Ownership (TCO), resulting in cost savings by improving the overall operational processes.
Currently sitting amongst the Engineered Sustainability product portfolio is the ZeroGap Multi-flex Chain, which has a patented top plate design to allow for tight side-flexing with no gap opening on the surface. This unique design enhances product performance and results in less tippage, reduced debris trapping and improved safety. Accompanying this, amongst many others, is the 661 Series Chain which offers improved product handling with smooth running conveyors, optimal bottle stability and low noise levels. A 25 per cent reduction in chain weight also means lower headshaft tension. In October 2015, Rexnord FlatTop will be attending the annual Brau Beviale exhibition in Germany to showcase its Engineered Sustainability product range and will be launching its new generation of low backline-pressure solutions designed to help increase safety, offer optimum product protection and reduce noise levels in packaging conveying.
Innovation is at the heart of Rexnord FlatTop being able to deliver these industry-leading solutions to the market. “We offer industry standard products, which are designed around the latest industry needs. This is a big portfolio of solutions, which are available off the shelf for low, medium and high speed bottling and filling,” highlights Rick. “Beside this, especially for OEMs, we are able to utilise and offer customisation to customers to optimise products for specific installations. We have continued our innovation drive in terms of materials as well and have just launched a hybrid material technology by combining engineered plastics with metals.”
To facilitate this level of continuous improvement across the global organisation, Rexnord employs a business operating system, which derives itself from Toyota’s renowned business system. Named the Rexnord Business System (RBS), it ensures that all manufacturing plants around the world are focused on the same strategy. In essence, RBS creates a scalable, process-based framework that focuses on driving superior customer satisfaction and financial results by targeting world-class operating performance throughout all aspects of the business. “In terms of capability, we have metal processing, injection moulding, machining, extrusion, testing, assembly and shipping all done in-house,” outlines Rick. “We also do all of our research and development in-house, which is supplemented by working closely with our global suppliers of resins, metals and technology to ensure we are driving the industry forward in the best way possible.
“As for the future”, Rick continues: “Over the next year we will be focusing heavily on expanding our Engineered Sustainability offer for primary and secondary packaging applications. We will also be looking to further develp our product offering for the automotive industry. In the longer term, Rexnord is planning to take a leading position in providing and demonstrating manufacturing efficiency by continuing to offer the most reliable and durable products in the industry.
“Last but not least, we continue to ensure that we are easy to do business with.”
Rexnord FlatTop
Products: Manufactures conveyer chain components for various industries
Sites: HQ: Wisconsin, US