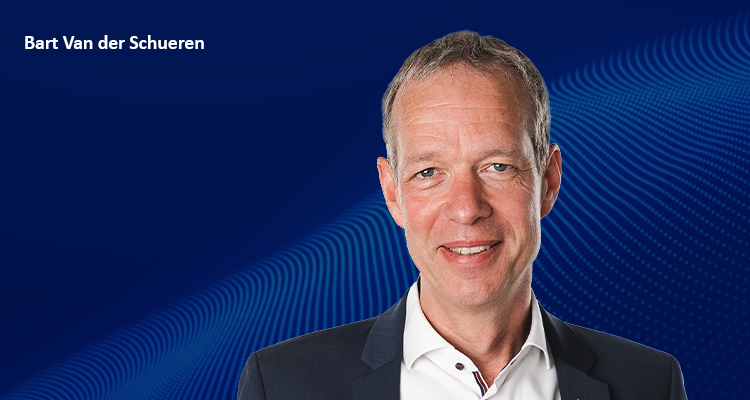
Scaling additive manufacturing for real-world manufacturing.
Until recently, the additive manufacturing industry focused heavily on innovation. The continuous introduction of radical new technologies often led to hesitation among manufacturers, who were reluctant to invest in refining and optimizing existing applications while anticipating the ‘next big thing’. As a result, many delayed new investments, uncertain of where the industry was headed. Now, a shift is occurring. A period of ‘détente’ in the technological arms race is allowing manufacturers to confidently invest in scaling production, driving broader adoption, and fully realizing the benefits of additive manufacturing. This shift is evident in the fact that fewer companies are entering the space, yet existing manufacturers are expanding their machine fleets. This marks a transition from innovation to application and signals a readiness to scale the technologies and processes already in development.
Scaling in additive manufacturing presents unique challenges, from material costs to process repeatability and production speed. Yet, scaling is essential for enabling cost-effective mass production while maintaining quality and design flexibility. Addressing these challenges is crucial for additive manufacturing to establish itself as a key pillar of modern manufacturing.
Scaling up in additive manufacturing (AM) directly relates to economies of scale, particularly in the relationship between raw material volumes and cost per kilogram. Despite 35 years of progress in additive manufacturing, material costs remain a major hurdle. While prices have decreased over time, they still cannot compete with the raw materials used in traditional manufacturing. The premium price for additive materials is largely due to their specialized forms, such as powders. While further price reductions are possible, the current market volume is not yet sufficient to drive down costs significantly. This creates a classic chicken-and-egg scenario: manufacturers need lower material costs to scale production, but costs will only decrease when production volumes rise significantly.
Scaling is not synonymous with growth. The fundamental difference is that scaling implies expansion without a corresponding increase in resources, particularly human resources. Too often, additive manufacturing operations expand linearly, requiring a proportional increase in workforce, which limits scalability. Overcoming this challenge demands automation at every stage of the process, from data preparation and machine operations to optimal scheduling and post-processing. The entire ecosystem must work together to achieve this, embracing greater openness and collaboration. This includes increasing interoperability between software and hardware, expanding material options, and granting access to key machine parameters. At Materialise, we have taken a bold step in this direction by opening up the algorithms behind Magics, our flagship software for data and build preparation. By enabling users to create fully customized workflows, we help manufacturers optimize their processes for efficiency and scalability.
A key obstacle to scaling up is the availability of a qualified workforce. Additive manufacturing remains a highly specialized field, requiring skilled professionals to operate and optimize processes. To facilitate broader adoption, the industry must demystify additive manufacturing by sharing knowledge and best practices, particularly about what works well in real-world applications. For example, Layer Analysis has proven valuable in quality and process control, providing deeper insights into the printing process. Emerging technologies like AI will further enhance process understanding, enabling operators to make informed decisions with less reliance on highly specialized expertise. By lowering the barrier to entry for skilled labor, we can make scaling additive manufacturing more achievable.
Successfully scaling up also depends on applying lean manufacturing principles. Leaning out a production process involves eliminating waste, reducing unnecessary steps, and streamlining operations. In this regard, additive manufacturing is often treated as an outlier, but the reality is that conventional manufacturing faces similar challenges. Producing the first few parts of any new design is typically inefficient. In traditional production, once the initial prototypes meet quality standards, the next step is to optimize the process for cost-efficient mass production. The same principle applies to additive manufacturing, but with one key difference: traditional manufacturing benefits from large production runs, allowing optimization costs to be amortized over many units. In contrast, additive manufacturing often operates at smaller batch sizes, making process optimization more costly. To truly scale, the industry must find more efficient ways to streamline and optimize additive manufacturing workflows.
Finally, scaling up in additive manufacturing is also about ensuring consistent quality. Printing a single high-quality component is relatively easy; the challenge lies in producing hundreds or thousands of identical parts while maintaining the same level of precision. This requires rigorous control over production processes, ensuring that every part meets stringent quality standards. The only way to achieve this reliably is through full process traceability, where every component’s production history is meticulously recorded. Advanced software solutions make this possible, enabling manufacturers to detect anomalies early and make real-time corrections. This level of control not only improves quality but also minimizes scrap production, further enhancing scalability.
For additive manufacturing to become an essential component of modern manufacturing, scaling must be a top priority. While challenges exist, from material costs to workforce availability and process optimization, they are not insurmountable. By embracing automation, increasing collaboration, and applying lean principles, the industry can transition from a niche technology to a mainstream manufacturing solution. The shift from innovation to application is already underway. Now, the focus must be on scaling additive manufacturing to deliver on its full promise.
Bart Van der Schueren
Bart Van der Schueren is CTO at Materialise. Materialise incorporates more than three decades of 3D printing experience into a range of software solutions and 3D printing services that empower sustainable 3D printing applications. Its open, secure, and flexible end-to-end solutions enable flexible industrial manufacturing and mass personalization in various industries — including healthcare, automotive, aerospace, eyewear, art and design, wearables, and consumer goods.