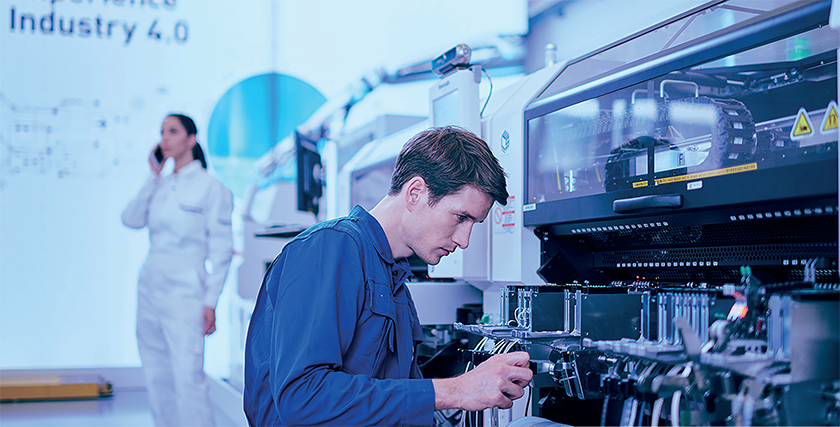
Seeing the future
Imagine the gates to the factory slowly swing open as the self-driving truck arrives. It reverses into the unloading bay and a team of robots swing into coordinated action. They remove the contents and load it onto the conveyor belt that recognizes and directs the components in the right direction – ready just in time for the next production run.
The ‘intelligent’ software drives the operation. Plugged into the factory and the wider supply chain it knows exactly when to order supplies, how to schedule, configure and run different production lines. It adapts based on any arising issues, such as changes in demand or supply problems. It is the brain of the operation.
On the other side of the facility, quality checking and packaging takes place. Before loading onto the next available self-driving vehicle, where the goods are transported automatically to the next step in the supply chain.
The autonomous factory, at the heart of a connected supply chain, is a long-held vision of what the future of manufacturing should look like. A world with lights-out production and zero human operators, where the location of the factory is irrelevant, and the manufacturing process is not impacted by the cost of labor, components, or production.
Intelligent software will be at the heart of the autonomous factory, communicating with businesses throughout the supply chain as it oversees everything from component ordering, delivery, and allocation to multiple production lines, to quality control, packaging, and shipping to its destination. At the same time, it can instantly adapt to any arising issues, such as changes in demand or manufacturing shortages.
But how can we connect and automate each individual element of the production process, from the intake of components, through manufacturing to the product’s ultimate destination? This is not a puzzle that can be easily solved. There are many different elements that need to be automated and connected – requiring a combination of many technologies, from hardware, and networked cloud infrastructure to software, all combined with integration and manufacturing expertise.
Giant strides made but challenges remain
The good news is that we have made massive strides towards this future in recent years. The foundation technologies delivering Industry 4.0, such as robotics, AI and its deep learning applications, are the building blocks of this future world. However, we should not expect a flick of switch change overnight. There are still some challenges ahead.
Some manufacturers still need to put in place the critical foundation technology infrastructure, such as cloud networks. There are also still some production challenges to overcome. For example, if we look at electronics production, the Surface Mount Technology (SMT) process is already highly digitalized but the Final Assembly, Test and Packaging (FATP) process is currently still more manual than automated. The challenge of automating the assembly of modules or the placement of the final irregular and odd-shaped components on the circuit board, still has to be resolved.
As well as the remaining individual production processes to automate, there is the ongoing challenge of integrating all the different elements into one production management system and embedding this software intelligence into the wider supply chain.
Today, organizations like ours are focused on delivering the digital layer which enables different machines and systems currently in silos, to talk to one another. That translates into full visibility and the ability to gather both real time and historical data that can be used to optimize operations.
Methods for procurement logistics and production planning are becoming increasingly important, such as the ability to model the entire production process and display it as a digital twin. This makes it possible to improve the capacity utilization of several lines and reduce the set-up times factored into the production schedule.
Looking to the near future, the next generation of powerful software management systems are delivering Process Enforcement, Material Management, Asset Performance Maintenance, Product Traceability, Defect Management, Business Intelligence and Station Control. With the associated data transparency, quality can be improved. In addition, costs are reduced and productivity is increased. Plan-result differences can be analyzed automatically and production schedules can be optimized accordingly.
Already advantages today
So, yes, there are still challenges ahead but the great news is that as we quickly complete each building block towards the autonomous factory, manufacturers are still able to take advantage by increasing operational efficiency as each new piece of the ultimate solution becomes available. And already today those benefits are significant.
As we automate each process and production line, we improve operational equipment efficiency. We reduce costs, we increase productivity and we improve important aspects such as material management and traceability across the supply chain.
Many of the largest organizations have already recognized these benefits and are aggressively implementing to gain competitive advantage. However, some medium and smaller sized manufacturers are still hesitating. They worry that these automated solutions cannot be tailored to their smaller facilities and production lines or the cost of the investment will be too large.
My message to those organizations is to look more closely. The move to the autonomous factory will be evolutionary, not revolutionary. It will be modular and can already be tailored to meet individual needs. It may still be 20 years before we reach the point where we have truly reached the autonomous factory and that moment of production equivalency. Even then it may still only be 90 percent automated but the commercial, social and environmental benefits will be immense. In the meantime, there are still plenty of commercial wins available for organizations as they follow the path towards that goal and reap the rewards of taking each new step on the autonomous factory journey.
Akira Yamashita
Akira Yamashita is Head of Panasonic Factory Solutions Europe. Panasonic Factory Solutions Europe is helping to make smart factories a reality with its wide range of automated solutions including electronics manufacturing solutions, robot and welding systems and software solutions engineering. As part of Panasonic Connect Europe, the business aims to contribute to the success of its customers with innovative products and integrated systems and services – all designed to deliver on Panasonic’s vision to Change Work, Advance Society and Connect to Tomorrow.
https://pfse.panasonic.eu