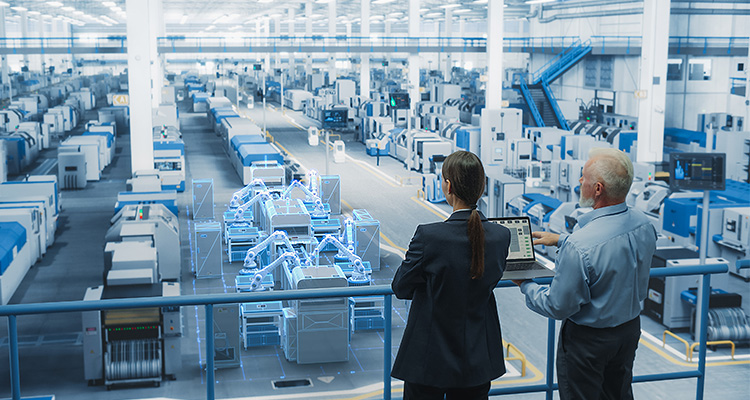
Silvia Gonzalez discusses how advanced automation is enabling more sustainable manufacturing
Across manufacturing there is continued investment in digital solutions to optimize operations. This includes addressing the obsolescence of existing automation, as well as automating remaining manual processes. Companies are implementing a broad range of advanced automation solutions to help meet their sustainability goals. Among these solutions are IoT sensors, robotics, and data analytics including cloud computing and artificial intelligence (AI). Technologies such as these are enabling organizations to increase the efficiency of their production processes, and identify opportunities to reduce energy consumption and materials waste, and increase throughput and product consistency. Producers are also continually looking for opportunities to apply predictive analytics, enabling them to identify potential equipment health issues before they become critical and cause downtime, waste and increased costs.
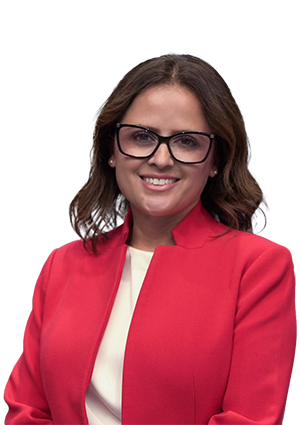
Reducing energy consumption has an obvious positive environmental impact. Industrial machinery is energy-intensive, consuming high power even when idle. To better meet sustainability goals, operators need greater visibility into their facilities’ energy use to address inefficiencies and waste. Energy management solutions support this by providing real-time insight into energy consumption and operating costs. Plant managers can view detailed values, such as idle consumption and peak loads, and see savings opportunities. For example, manufacturers can identify idle machines and optimize machine schedules during off-peak hours, reducing electricity use across the plant floor and significantly lowering overall utility costs. Most facilities can reduce energy waste by ten-to-30 percent and carbon emissions by 15-to-30 percent.
Clean-in-place systems
Focusing on the processes and equipment that consume the most energy helps to make the biggest improvements. Within food and beverage and life sciences, clean-in-place (CIP) and steam-in-place (SIP) systems can use nearly 30 percent of a plant’s utilities, but manufacturers often do not know exactly how much energy and media each cleaning cycle consumes. Also, cycles typically run for a preset amount of time that may be longer than required for proper cleaning. This results in wasted time, water, steam, chemicals and energy. Again, greater visibility into the systems and control of the processes is key to optimizing their efficiency. This is provided by CIP/SIP utility solutions that combine sensor-equipped devices, such as pressure regulators and valves, with integrated software to capture and aggregate critical process data for analysis. These solutions automate the necessary reporting process, while also providing an in-depth view into the process to help manufacturers improve efficiency, reliability and sustainability. By tracking utilities and comparing each cycle against an ideal CIP/SIP cycle, manufacturers can reduce water consumption by 20-to-35 percent.
Optimizing compressed air use
Pneumatic systems are essential to power many processes and machines, but compressed air generation makes up 20-to-30 percent of electricity consumption at a typical manufacturing facility. There is often a lack of visibility to the amount of compressed air used by each line or machine and the subsequent energy consumption. Without monitoring, up to 30 percent of compressed air generated can be lost due to leaks and sub-optimization of machines and devices. Compressed air monitoring solutions can continuously measure air flow in real time, identify anomalies early, and send personnel notifications to address them. Taking a floor-to-cloud approach, these solutions utilize air flow sensors to collect compressed air data, with edge gateways transmitting data to cloud-hosted software that provides easy access to the data from any location. Statistics and trends help to determine leakage, energy consumption and the amount of carbon dioxide produced, enabling operators to make quick, informed decisions about the most appropriate course of action.
Machine learning
Taking this one step further, machine learning models are now available that enhance pneumatic system applications by learning ideal system behavior and accurately forecasting anomalies. When minor air flow deviations occur, AI can pinpoint leaks before they escalate, allowing personnel to address them proactively. The models can even detect creeping leakage – a subtle but impactful issue that can reduce overall equipment effectiveness (OEE). AI-driven condition monitoring and prediction helps facilities to optimize energy use and improve sustainability. Moreover, by reducing energy costs and preventing unplanned shutdowns, these solutions deliver a rapid return on investment.
Recyclable bio-based plastics
Lowering energy consumption and emissions is essential but reducing material waste and single-use packaging are other areas where advanced automation is supporting sustainability. Consumer product manufacturers are increasingly committed to reusable, recyclable or compostable packaging, but this brings new challenges. Recyclable bio-based plastics, for example, are extremely sensitive to heat, which makes it almost impossible for traditional hot sealing methods to hit the necessary time/temperature ‘sweet spot’ every time – a necessity to ensure packaging strength and performance. Advanced ultrasonic welders employ high-frequency vibration to create friction heat within plastic layers’ interface during brief (less than one second) weld cycles. Very precise weld control ensures the quality of the join, while having the added benefit of only consuming energy during the millisecond weld cycles, helping to deliver energy savings of 25-to-75 percent relative to traditional thermal sealing. ■
Silvia Gonzalez
Silvia Gonzalez is Global Director of Software at Emerson, with over 26 years of experience in software and industrial automation. She leads cross-functional teams delivering innovative solutions in digital transformation, IIoT, SCADA, connectivity and augmented reality. Emerson is a global technology and software company providing innovative solutions for the world’s essential industries. Through its leading automation portfolio, including its majority stake in AspenTech, Emerson helps hybrid, process and discrete manufacturers optimize operations, protect personnel, reduce emissions and achieve their sustainability goals.