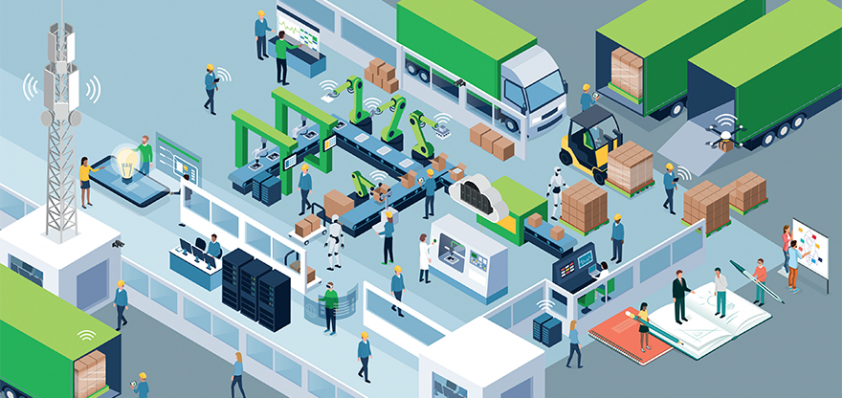
Smart connections
Talk of Smart Factories, the Industrial Internet of Things and Industry 4.0 have been commonplace since the internet revolutionized communications towards the end of the 20th century but, for many manufacturers – particularly those further down the supply chain – these ‘grand ideas’ have remained steadfastly just that: ideas.
But with the arrival of 5G, the technology to turn ideas into reality is finally here, and three years after the UK Government launched its 5G Testbeds and Trials (5GTT) programme, the results are demonstrating serious potential to transform manufacturing operations across the world.
The UK’s first live 5G factory trials took place at the Worcestershire 5G Testbed through 2018-2020, in what was a landmark step toward the creation of smart factories in Britain. Working with locally based Worcester Bosch, Yamakazi Mazak and defense company QinetiQ, amongst others, the trials tested use-cases for 5G technologies, covering everything from changes to factory floor production processes, to real-time analysis and remote machine operation.
Worcester Bosch tested 5G for improved factory output, exploring preventative maintenance using IoT sensors and data analytics to predict failure; QinetiQ looked at designing security into 5G networks and applications; while Yamakazi Mazak explored how technology could be used to troubleshoot applications, allowing senior engineers to remote guide onsite engineers through remote machine maintenance. Elsewhere, SME aerospace manufacturer, AE Aerospace, has also been developing its ‘glass factory’ concept, looking at how installing a private 5G network can be used to plan production, collecting and monitoring performance data in real time to optimize production, and create a new ‘capacity availability’ model; how sensors can be used to locate and ensure gauges are correctly calibrated; and using AI to improve quality and inspection processes. Whilst at the Manufacturing Technology Centre in Coventry, we are working with them to build a 5G network and develop demonstration use-cases that will highlight to visitors the capabilities of 5G in an industrial setting.
These use-cases have all contributed to seminal work as part of the DCMS 5G Testbed and Trials (5GTT) programme, which identified that 5G networks could enable productivity savings of two percent in manufacturing, the equivalent of £2.6bn when extrapolated across the whole of the UK, although many believe this to be a conservative estimate. They are just a handful of examples that highlight a myriad of ways 5G will enable smarter, connected manufacturing.
So how can more manufacturers get involved?
Lack of awareness of the ‘real life’ benefits, use case identification, identifying resources to trial ideas and build business cases, working with legacy equipment, cyber security concerns, technical knowhow, funding and access to 5G networks are just some of the barriers currently preventing manufacturers from getting ready for the fourth industrial revolution.
However, progress is being made. A 2017 survey by Make UK suggested that just 20 percent of manufacturing SMEs had started the job of preparing for Industry 4.0, but, by 2020, 80 percent of respondents were reporting they would be ready by 2025. The impact of the Covid-19 pandemic may impact that timeline slightly, but, with networks and support systems increasingly in place to help manufacturers of all sizes explore the potential of 5G, UK manufacturers should be set to lead the charge into this smart new age.
As the team behind the installation of the first private 5G network at a UK manufacturer, we’ve seen first-hand the challenges and benefits of setting up a smart factory environment, from the perspective of both manufacturing businesses and also technology providers. That is why we created our Testbed as a Service programme, supported by technology partner BT, to provide a safe and accessible platform for UK industry to develop and test next generation technology.
While there will be some individual use cases that require 5G networks on their own merit, there isn’t one killer application or use case that will drive 5G adoption. More likely, the installation of
5G networks will be best justified where several applications operating together require the benefits that 5G offers. These benefits range from increased bandwidth capacity, faster download times, reduced latency, and greater ability to connect multiple devices in a flexible environment.
On the shopfloor, this might translate into the ability to monitor and adapt production schedules in real time, storing and processing highly-detailed inspection images for quality inspections carried out by artificial intelligence or locating tools and moving them around the factory on a just-in-time basis.
Many applications are likely to arise from existing continuous improvement programs and, as such, I4.0 readiness may well be led by a combination of CI, operational and R&D teams. To adapt a sporting analogy: it’s the accumulation of marginal gains, supported by 5G networks, that will likely deliver the greatest returns. Productivity gains from improvements in process, quality control, health and safety, customer experience and a greener agenda are all achievable, and can be amplified still further by collaborating between project teams, in-house departments, manufacturing sites and even supply chain businesses and customers.
Crucially, with greater collaboration comes security risks and this is where access to public and private 5G testbeds comes into its own – allowing security features such as multi-site network access control, strong mutual authentication and encryption to be trialed, tested and built into programs from the off, ensuring manufacturers can benefit from IIOT in a cyber safe environment and stay at the forefront of security developments through access to security experts and products, such as those developed by security specialists QinetiQ.
All in all, the potential offered by 5G to power smart, connected manufacturing is exciting but knowing where to start can be overwhelming, not least when juggling the day-to-day challenges of running daily operations. But the eco-system is developing quickly. Governments across Europe are investing in networks and trials to drive adoption within their own manufacturing sectors, and ensure they are well placed to reap the benefits offered by Industry 4.0. With a variety of funding streams now coming online too, there has never been a better time to connect with 5G experts and identify the right IIoT opportunity for your business.
Ste Ashton
Ste Ashton works at 5G Testbed as a Service provider nexGworx. In 2018, Worcestershire was chosen by Government as the home of a new 5G Testbed, putting the county at the forefront of technological innovation. Worcestershire 5G (W5G) was one of six projects led by small and medium-sized enterprises (SMEs), universities and local authorities that represent the best of UK innovation, resources and expertise. It tested 5G technology within several business-led applications, with a focus on manufacturing and how 5G technology can improve productivity. The testbed was highly commended at the World Communication Awards and won Most Commercially Viable Use Case at the inaugural 5G Realised ‘Use Case Awards’.
W5G is now a private 5G Testbed as a Service (TaaS) provider and officially launched as nexGworx in June 2021. nexGworx is hosted and operated at Malvern Hills Science Park (MHSP) and supported by formal teaming arrangements between MHSP, Worcestershire County Council and strategic technology partner BT plc, along with its supply chain partner ecosystem. It continues to be actively supported by Worcestershire LEP.
www.nexGworx.co.uk