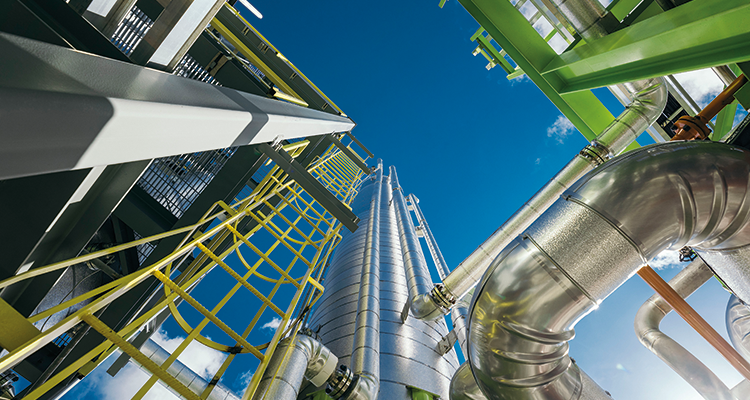
Solugen is taking sustainability to new heights through carbon removal; here’s how
The chemicals industry is one of the most polluting in the world. In addition to being responsible for 30 percent of global carbon emissions; it can also be accountable for releasing toxic compounds. As such, we rarely hear about the processes used to refine products within the chemicals sector. Fortunately, the opposite is true at Solugen. Based in Texas, the company is incredibly proud of what is taking place in its bioforges, which use feedstocks to produce molecules that are sustainable and cost-effective. Furthermore, as one of its founders is a physician, the business swears by the oath to do no harm to the planet. This means not only sustaining the lives of the people within and around its operation, but also the environment.
The team at Solugen has developed a process that uses bio-based feedstocks instead of petroleum, thereby actively removing carbon from the atmosphere. Having introduced the concept of the first carbon negative molecule, and how it can be scaled to meet the needs of a range of industries, Solugen has become a global leader in scalable synthetic biology.
Sean Hunt, Chief Technology Officer and Co-Founder, shares greater insight into the operation of his business. He highlights how the bioforges and their processes are shaping the manufacturing industry by contributing to a greener and more sustainable future for the chemicals sector.
Solugen was brought to life in 2016 after Sean, and Co-Founder Gaurab Chakrabarti, discussed the potential of carbon removal over a poker game back in 2010. “We met through my wife actually. Gaurab has an MD and PhD in oncology, while my background is in chemical engineering, where I focus on heterogenous metal catalysis, which is the core technology that forms the world around us.” From Sean’s perspective, the dynamic between him and Gaurab is what facilitated this pioneering process. “We jokingly call Gaurab the artist and I am the hammer. He specializes in enzymes, and I focus on heterogenous. For me, Solugen is the story of two people who function as a great team; that’s what we’ve been since day one and we will continue to be that for as long as possible.”
Green chemistry
Gaurab believes in using biology in unconventional ways to solve complex problems. Having studied computational neuroscience as an undergraduate at Brown University, he received his MD and PhD in cancer biology and enzymology at the University of Texas. He is an author and co-author on over 20 peer-reviewed publications and patents, and both he and Sean have made it onto Forbes’ list of 30 Under 30 in Industry and Manufacturing. Sean’s background is quite similar, although his engineering experience has spanned a wider range of industries and applications. He worked as a fuel cell engineer for the US Navy, a vaccine and API process engineer for Merck in Singapore, and a Cocoa Puff engineer at General Mills. Sean holds a PhD in chemical engineering from MIT, where he studied renewable energy and green chemical manufacturing on metal catalysts as an NSF graduate research fellow. With these credentials, the pair have formed an unstoppable partnership.
“Back in 2010, Gaurab was working on enzymes that produce chemical processes at 100 percent yield with water at room temperature, which is the definition of green chemistry. This offers the best of both worlds because we get the same upfront functionality of enzymes, coupled with downstream heterogenous metal catalysis process,” Sean shares.
The idea was sparked by the possibility of building a chemical plant that yields 90 percent, instead of 50, to increase revenue and lower emissions. Through the use of AI to engineer enzymes and metal catalysis that can bypass the limitations of traditional fermentation, Solugen produces molecules at room temperature using bio-based feedstocks, no air or water waste emissions, resulting in zero toxins and zero waste. “It allowed us to have a smaller CapEx footprint as we wouldn’t have the downstream installation costs. So, we pitched the concept to MIT in a competition where the grand prize was $100,000, and we lost spectacularly.”
Golden month
However, this defeat did not dishearten the pair. If anything, it spurred them on. Following that, one of its first customers saw the MIT pitch video, and expressed that if Sean and Gaurab could produce the same bio peroxide that was demonstrated in the video, the customer would buy it. “So, we built this tiny PVC reactor to create our solution, and that’s how we expanded into a one-stop-shop – manufacturing chemicals, and growing to become fully integrated.”
Since then, the company has scaled up its core technology and blended its supply chain distribution business to service customers in the energy, industrial water treatment, agriculture and concrete sectors. Sean is pleased to announce the company has recently celebrated its ‘golden month’. This milestone recognizes how its first commercial plant has run for 1000 hours at over 1500 kgs per hour, with an average of 94 percent yield of product from feedstock. “This is so exciting, and it proves that we can grow even further. Currently, we are looking into long-term debt financing to build out an asset fleet, which will help us reach more customers,” he expresses.
When it comes to chemistry and biology, nature has years of experience, and it’s from here that Sean and Gaurab draw their inspiration to innovate sustainable manufacturing. Unfortunately, this isn’t always an easy task, and takes a large amount of finance to get off the ground. Sean believes the secret is bridging the gap between equity and debt financing to make the process more accessible to other businesses. “They are two completely different worlds. An incumbent chemical plant can have an incredibly expensive CapEx. I still see a huge bias towards building through the traditional way because it’s considered low risk. Our process is more efficient, even though it is still risky. We are fairly advanced in terms of our journey, but we are going to ramp up the efforts regarding our scalability so that everyone has access to this technology.”
Sustainable operations
The company’s approach to making the manufacturing industry more sustainable is a holistic one that begins with the feedstock. “Today, we use regenerative agriculture, but in the future, we are looking at cellular feedstock to help with industrial emissions.” But is there more that can be done? Sean’s answer is ‘absolutely’. From his experience, the US government is grappling with policy to improve ways in which manufacturers can work more sustainably. “Recently, I was in Washington DC at the GC3 for the Department of Energy roundtable and I learned that there are loads of groups working on this initiative, which is so encouraging.”
Life’s building blocks
The success of Solugen’s bioforge factories now serve as a model to be duplicated in other areas. “We are honing in on a location that will have a 25KTA plan. The rationale is not to scale globally, but rather to grow slowly. We have a pipeline of 42 different molecules that are at various stages of research and development, and our ultimate goal is to take the whole molecule pipeline and launch it on a bioforge asset.”
This means that Solugen’s plans to innovate the business further will also allow it to continue to develop. “One of our most exciting outcomes is the completion of two different projects we’re working on. One of them consists of converting recycled cardboard pulp into feedstock, meaning small cellulose fibers can be turned into glucose. The main feedstock we use at the moment is corn-based so that will be a great diversification. At the same time, we are also working to convert waste cardboard pulp into nylon through the entire value chain where we want to hit a number of transformation steps.”
In five years’ time, Sean is keen to see Solugen’s core asset base expand. “We have been commercializing drop-in chemistries so that in five years, our project to convert cardboard to nylon, for example, will be a helpful practice across the world. This is what we want to see: sustainability in the chemicals industry, where you’re least likely to see it,” says Sean.
The climate crisis seems to be the most insurmountable challenge humanity has faced to date, and from what Sean has shared, tackling it means starting with the invisible building blocks of life. Solugen has established a product development process to help meet the growing demand for sustainable, nontoxic ingredients. With the help of scientists like Sean and Gaurab, this application is accessible across a wide range of industries, and serves as a reminder of how powerful the right molecule and the right method can be.