SPEE3D’s technology is shaping the future of how metal parts are produced
In the rapidly evolving world of manufacturing, the quest for efficiency, speed, and innovation is never-ending. Traditional methods of producing metal parts – namely casting and forging – have long been a bottleneck for many industries suffering from slow turnaround times, high costs, and inefficiencies. This has been compounded by the challenges posed by a global supply chain that is vulnerable, expensive, and restrictive in terms of customization options. However, a transformative solution has emerged in the form of Cold Spray Additive Manufacturing (CSAM), a technology pioneered by SPEE3D, which is already redefining the landscape of metal manufacturing.
Introducing CSAM: a game-changer for metal manufacturing
CSAM uses a high velocity compressed gas stream to accelerate metal powder particles at supersonic speeds, and while it is a 3D printing capability, it most closely competes with traditional casting. Upon impact with a substrate, these particles deform and bond together, creating dense, strong cast-equivalent parts without the need for high temperatures or specialized conditions.
CSAM offers several advantages over other manufacturing processes, including high deposition rates, operation at relatively low temperatures to minimize material distortion, and the ability to use a wide range of materials. Furthermore, it is a cost-effective, highly automated process that can be deployed anywhere, making it ideal for producing large parts quickly and efficiently.
SPEE3D’s solution: equipment, software, training, and support
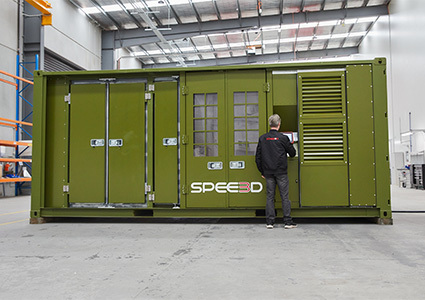
SPEE3D’s CSAM technology takes metal casting into the 21st century – giving customers the unprecedented ability to manufacture cast-equivalent metal parts on-demand and on-site, faster than ever thought possible.
SPEE3D doesn’t just offer a novel manufacturing technology; it provides a comprehensive ecosystem designed to ensure its clients can leverage CSAM to its fullest potential. This includes a range of equipment from small to large-format metal 3D printers, like the LightSPEE3D and WarpSPEE3D, and deployable solutions such as the XSPEE3D.
XSPEE3D
Drawing on direct collaborations and feedback from field trials with the Australian Army, SPEE3D identified a clear need for a deployable metal additive manufacturing capability that could simplify logistics and address the challenge of transportability in remote locations. SPEE3D’s dedication to solving transportability challenges resulted in the creation of the XSPEE3D – a ruggedized, containerized metal 3D printer housed within a standard shipping container. This design choice capitalizes on the international standardization of shipping containers for ease of transport via land, sea, or air, allowing XSPEE3D to be moved seamlessly, even to the most challenging terrains.
In addition to manufacturing equipment, SPEE3D offers software for efficient CAD-to-file preparation (Twinspeed) and robust support services including installation, commissioning, user training, applications assistance, field exercise support, and equipment maintenance packages.
Transformative impact: case studies from defense
SPEE3D’s technology has already made significant inroads in various sectors, from commercial research and development to defense, demonstrating its versatility and effectiveness.
For the defense industry SPEE3D delivers the metal AM (Additive Manufacturing) technology needed to safely, rapidly manufacture cast-equivalent spare metal parts on-site and on-demand. This allows a defense force to accelerate battle damage repair from weeks and months to hours and days.
Three main elements of SPEE3D’s solution set it apart for defense customers: proximity, speed, and simplicity. It delivers on-site, containerized metal manufacturing proven to operate in remote, austere environments. It is also the industry’s fastest metal manufacturing technology and by eliminating the need for lasers or inert gases, complex infrastructure, or extensive training the technology is simple enough for technicians in the field to operate the equipment quickly and safely.
SPEE3D’s journey in the defense sector began in 2019, when the Royal Australian Navy embarked on a $1.5 million trial of CSAM technology. The navy was keen to explore the potential of manufacturing and certifying metal 3D printed marine applications for an Armidale-class patrol boat
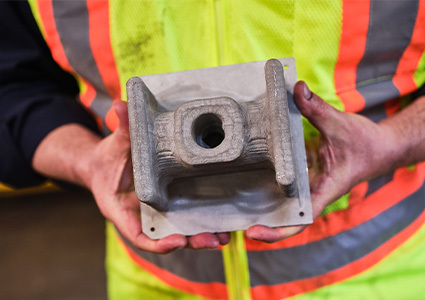
In 2020 and 2021, the Australian Army conducted world-first expeditionary metal 3D printing trials that aimed to significantly increase the availability of parts compared to what the regular supply chain could provide. The trials demonstrated that the WarpSPEE3D printer could be taken into an expeditionary environment and manufacture metal parts in the field. This achievement showcased the deployable capabilities of CSAM technology to the front lines, enabling defense forces to manufacture their own metal armored vehicle tools and parts in hours when needed. Over the course of the trials, Australian Army personnel created and produced over 50 case studies of 3D printed Australian Army components, from part design through to printer operation, part post-processing, and testing.
In 2022, SPEE3D technology was also trialed by British Army REME soldiers to generate parts for a multinational training force as part of a concept assessment in tandem with the US Army’s Project Convergence Program. Several thousand US, UK, and Australian service members, researchers, and industry partners aimed to evaluate approximately 300 technologies, focusing on advancing joint and multinational interoperability in future operational environments.
During the joint exercise, SPEE3D and the British Army collaborated on creating dozens of applications for various US and British armored vehicles over the campaign’s two weeks. For example, while out in the harsh desert conditions of Fort Irwin, one of the many parts the SPEE3D and British Army team printed was an M109 specialist tool. At the request of the US Army, this specialist tool was able to be designed in just nine minutes. It was printed in 30 minutes and heat-treated in just under two hours and then put to immediate use in a real-life scenario to remove a bolt from an M109 wheel.
In 2022, SPEE3D’s WarpSPEE3D printer was also utilized by the US Navy during the NCMS REPTX exercise. The printer produced dozens of military maritime parts in various corrosion-resistant materials on US Navy Ship ex-US Paul F. Foster, DD 964, the Self Defense Test Ship (SDTS). The trial opened the possibility of military ships becoming self-sufficient manufacturing hubs, reducing the need for port visits for metal part replacements and repairs. This could potentially allow ships to stay out at sea for longer, enhancing ship readiness when in theater.
Moreover, the deployment of multiple WarpSPEE3D printers to support Ukrainian military operations highlights the strategic advantage provided by CSAM technology. By enabling the rapid production of critical repair parts on the frontline, SPEE3D is directly contributing to the resilience and readiness of defense forces.
SPEE3D’s vision for the future of manufacturing
SPEE3D is at the forefront of a manufacturing revolution, offering a solution that not only addresses the limitations of traditional and additive manufacturing methods but also paves the way for new possibilities in design, efficiency, and sustainability. By providing a robust, scalable, and cost-effective alternative, SPEE3D is not just solving today’s manufacturing challenges; it’s shaping the future of how we produce metal parts across industries. As Benjamin Franklin’s wisdom suggests, investing in the right tools is paramount to success. In the context of modern manufacturing, SPEE3D’s CSAM technology and ecosystem might just be the right tool for the job and a pivotal investment in an organization’s future, be that in the lab, on the workshop floor, on a ship or even the front line.
SPEE3D is a leading metal additive manufacturing technology company dedicated to the research, development, and delivery of metal 3D printers and integrated systems. The SPEE3D portfolio offers significantly faster production than traditional metal manufacturing methods and offers a wide range of metals, including aluminum, aluminum bronze, stainless steel, and copper.
To learn more about how SPEE3D can enhance your business, visit: