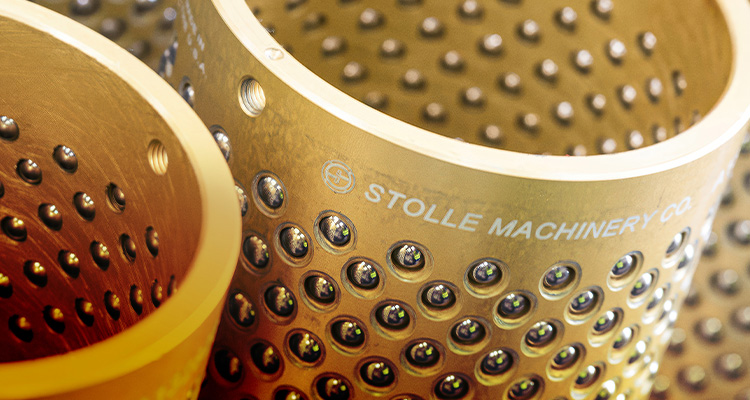
Stolle is committed to advancing metal packaging for future can makers while delivering sustainable solutions today
Stolle is the world’s leading supplier of two piece can and end making machinery for the can making industry. Its high-speed machines are the backbone of can making operations worldwide due to their proven productivity and reliability. The company provides complete solutions at any level, from individual machines, line modules, and rapid service with OEM parts to the design, build, and commissioning of a complete facility.
Integral to Stolle’s global operations are Stolle Europe and Stolle Machinery UK: Stolle Europe supplies Global Systems solutions to customers alongside a growing UK based conveying equipment operation. Stolle Machinery UK designs and manufactures washer, oven and necking solution to customers globally out of its UK and Poland facilities.
Stolle Europe’s Global Systems team is well equipped to serve beverage, food can and end makers throughout the United Kingdom, Continental Europe, the Middle East and Africa.
“I manage the systems integration part of the business,” begins Jamie Fraser, Stolle Global Systems Project Director. “Stolle is predominantly a machinery manufacturing company, and some of those machines are manufactured for installation in turnkey projects for which we carry out the design, installation, and commissioning and then hand over the operational factory to the client, wherever in the world they’re based.”
Stolle Global Systems has extensive experience around the world, from new installations on green or brownfields to facilities redesign, individual machine module analysis and remediation. Many of the Stolle Global Systems team are former can plant employees and managers themselves, affording the insight and experience to understand the intricacies and practical ramifications of can and end line layout and construction. “I’m responsible for manufacturing in Europe,” continues Richard Mercer, MD Stolle Machinery UK (SMUK), “which covers the manufacture of several of Stolle’s product lines across two sites in the UK and a site in Poland. Where Jamie’s team designs the factories and installs the equipment, SMUK is responsible for manufacturing some of the equipment that operates those product lines.”
Stolle Machinery UK facilitates the design and manufacture of a wide range of thermal products including Optimus washers and dryers, DecoCure pin ovens and InterCure internal bake ovens. It also builds the Stolle E-NCKR modular die necking system, as well as coolant filtration systems configured to fit any body maker module.
All this experience combines to create a powerful partner for companies in emerging markets, that are looking for can making solutions. “South Africa has been quite a hotspot for us over the last few years,” Jamie shares. “We first did a project there in 2019, and since then, have consistently completed projects, one after the other, for two prominent clients. One of the customers owns beverage brands and the other is a packaging company that wanted to get into can making and has since grown beyond expectations. Its capacity was about one billion cans a year and is now up to three billion cans a year. It’s a similar story for the brand owner; the initial expectation was a capacity no greater than 800 million cans a year, but we’re currently expanding that line to one billion and there’s talk of a second line as well. It’s been a very successful market for us and has developed rapidly.”
Likewise, the conveying piece of Stolle’s operation is also experiencing exceptional growth with a predicted increase of 60 percent. Stolle Conveying Systems designs, manufactures and commissions specialized conveying and material handling systems from large turnkey conveying system projects to smaller designs and projects. It also stocks a wide range of mechanical and electrical support components. Production ranges from systems for DWI, including fast changeover, three-piece cans, composite cans, ends conveying, and PET systems to varied food production applications.
Beyond new systems, Stolle Conveying Systems offers line speed improvement, modifications, and retrofits, as well as decommissioning and machine relocation. Its facility utilizes the latest machinery and technology to meet customer requirements and the highest standard of manufacture. All products are designed, manufactured, installed, and commissioned by industry expert engineers, who are accustomed to customer expectations.
Dave Wildey, Project Director, Stolle Conveying Systems, is responsible for the sales side of the conveying segment as well as the technical design aspect, with a focus on emerging markets and new designs. “Stolle acquired a local conveying company approximately six years ago,” he explains. “It would generally do one line a year but since the acquisition, it’s been integrated into the Stolle Global Systems team, so we now work alongside Jamie’s team. Every time a can line is sold, we are involved in the conveying for that line. It has taken off massively and has grown very quickly.”
“We do have several active contracts,” adds Jamie, “and are finishing a project in Mexico for Heineken, which has been hugely successful for us. It’s Heineken’s first can line, as the company opted for vertical integration in that plant. It was a full turnkey project for us, passing qualification tests last month, and is currently being handed over to the customer and closed off.”
In a significant new development, Stolle Machinery UK recently completed the construction of a new facility in Burnley, UK. The 158,000-square-foot facility has been built to consolidate Stolle’s Altham UK manufacturing operations that were in five separate buildings. The facility in Burnley includes spaces for machine assembly, parts machining and warehousing, field service, die and machinery rebuild, engineering and administration. The new Burnley facility includes the latest sustainability features and will allow operations to be more efficient. The site benefits from Cat A specification offices, as well as a BREEAM Very Good standard rating.
The Burnley facility will also be the core of spare parts distribution to customers in Europe, Middle East and Africa. The project to transfer inventory is on track to complete during Q2, capitalizing on synergies to combine manufacturing, spares supply and internal procurement for this key revenue stream for the Stolle group. The site will be a major hub for genuine Stolle OEM parts, field service and technical support, working closely with customers to support their needs.
“We’re delighted to be consolidating our operations into this impressive facility in Burnley,” Richard elaborates, “which is exactly what we’ve been looking for. Many of our employees are based in Burnley and the surrounding areas, so it was vital we stayed close to our current home in Altham.
“The real inroad for us,” he enthuses, “is that we manufacture the machines as well as install the lines. We can also provide additional bolt-on services as part of any package from the outset, which gives us a competitive advantage.”
“I think Stolle would consider itself different to everybody else in the market,” Dave adds. “While we face competition on numerous fronts, nobody has the range of products we offer. There are other machinery manufacturing companies and other system integration companies, but there are not many companies that can do it all.
“Historically, for systems, we had to ship a large amount of equipment around the world. Ten years ago, either the customer would take on that logistics aspect or we would pass it all over to a freight forwarder. Over the last five years, we’ve been able to bring that more in house to create an additional revenue stream by offering shipping services. This brings the added benefit of greater control.”
“In terms of control,” Jamie adds, “we’re working with forecasts and longer projections more so than ever before which helps suppliers to deliver the necessary quantities, which is particularly important having emerged from the instability of recent years.”
Stolle is committed to advancing metal packaging through a constant flow of sustainable innovations and technology that will benefit customers. From some of the strongest and most metal-efficient tab designs available to brilliant new equipment upgrades and revolutionary new equipment poised to positively impact the next generation of can making, Stolle continues to make significant investments in R&D in every area of can making. The company’s global Technical Centers are dedicated facilities, developing the advanced technology that future manufacturers will come to rely on while producing the sustainable machinery features that today’s customers expect.
“The company is constantly innovating and introducing new technologies. Stolle inSight, for example, ushers in the future with an interactive interface that provides real-time operational analytics through the HMI, improving performance and efficiency in real-time, while reducing recovery and maintenance times. The inSight Panel also maintains a log of performance and quality data for deeper analysis,” Richard adds. “We’re continually working to make our machines more sustainable in terms of the technologies we implement to help reduce energy and water consumption, as well as exploring alternative energy provision.”
The Stolle Optimus Can Washer, for instance, has the lowest water consumption of any can washer available. Intelligent counterflow and backflow systems minimize water usage and discharge to the drain. Fresh water is introduced at the final rinse and is filtered and recycled through earlier rinse stages where the cans are less clean. Energy saving features include a low loss header for heat recovery from other can plant systems to reduce boiler gas consumption.
Stolle is committed to sustainable equipment and practices that help manufacturers produce over 400 billion aluminum cans annually. Unlike plastic, which is not easily recyclable, aluminum is infinitely recyclable and 75 percent of all the aluminum ever made is still in use. Indeed, only nine percent of plastic made since 1950 has been recycled; most of it is in landfills and oceans.
Looking ahead to the coming year, Stolle is set for steady growth across the group. “We’re currently getting a lot of enquiries on the conveying side of the business, which also ties into the systems side. Several customers are looking to expand the capacity of existing lines, so are exploring integrating conveying into those projects,” Dave shares. “Further afield, we want conveying to be up there, competing as a market leader in the industry. That’s really the goal for any Stolle product. We strive to be a solutions provider and position ourselves ahead of the curve in terms of innovative and sustainable solutions.”
Indeed, Stolle is dedicated to continually advancing customer needs through innovation and technology. Specialized engineering staff work with experienced technicians in Stolle’s R&D Technical Centers to try out new ideas and concepts and incorporate new technology and materials as they become commercially available. Many times, teams start from scratch, developing equipment that simply doesn’t exist to fulfill industry needs for function, speed and efficiency, now and for the future.