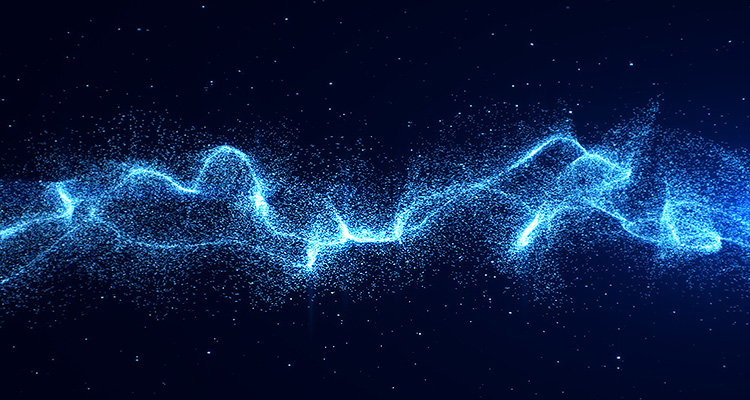
The four best ways to lower energy costs. By Dr. James Crosby-Wrigley
This year, the manufacturing industry faces significant challenges. Many external factors are influencing the economic outlook of the UK sector, including rising employment taxes, increased costs of raw materials, additional compliance standards, and further trade barriers for export orders. These represent significant and largely uncontrollable factors which may ultimately reduce the profitability of an organization.
However, there is one additional cost which manufacturers have significant control over – operational energy costs and expenditure. While grid-sourced commodity markets remain volatile and non-commodity price increases are introduced by independent bodies (e.g. Distribution and Network Operators), businesses have the opportunity to control how this affects them. In this article, I outline the four best ways for businesses to implement cost-reducing measures (using the example of Silverline Office Equipment) and ultimately increase their profitability.
Option 1: Undertaking site audits, metering solutions, and sustainable practice implementation
For a manufacturing business to thrive, it is essential to have a thorough understanding of how its facilities operate. While many successful businesses excel at managing engineering and process operations, they often overlook the allocation of energy within these processes. This gap can be effectively addressed through bespoke site audits and advanced metering solutions. By leveraging detailed audits and process-level metering data, manufacturers can achieve two key outcomes that reduce energy consumption and costs:
Identifying out-of-hours consumption: Advanced datasets provide insight into the exact flow of energy throughout a facility, making it possible to pinpoint energy usage during out-of-hours periods. Corrective measures can then be implemented to eliminate unnecessary consumption.
Minimizing idle time: Major assets, such as process equipment or fundamental infrastructure (e.g. heating and lighting), are often left running when not necessary. By identifying this idle time through metering data, businesses can adopt practices to minimize energy wastage and reduce expenses.
Measures such as these can have a 20 percent to 50 percent energy consumption reduction on a facility.
Option 2: Introducing more efficient technological infrastructure
Manufacturers can significantly reduce energy consumption without compromising productivity by introducing efficient technologies. Voltage optimization helps streamline electrical supply, cutting down on energy waste while ensuring equipment continues to operate effectively. LED lighting systems, paired with smart controls and sensors, adapt to real-time needs, reducing unnecessary usage. Variable speed drives (VSDs) enable equipment like pumps and conveyors to match energy use with actual demand, boosting efficiency. Lastly, upgraded heating and ventilation systems also play a crucial role in minimizing energy consumption while maintaining the required climate conditions.
These technologies typically reduce the total energy consumption from a facility by seven percent (voltage optimization) to 40 percent (heating and ventilation upgrades).
Option 3: Installation of renewable generation assets
The energy grid is typically associated with three major challenges for manufacturers: high carbon footprint, high costs, and volatile pricing. Renewable energy solutions, such as solar PV systems, are excellent technologies that address these issues effectively:
Cost savings: The cost of renewable energy systems has reduced drastically over the last ten years. For example, rooftop solar PV panels pay back their cost in three to six years with a lifetime cost of energy of approximately 5 to 7p/kWh. For industrial manufacturers, this can result in tremendous cost savings in energy-intensive operations.
Price stability: Factory units can generate 25 percent to 40 percent of their total energy needs in-house through the installation of renewable energy systems. This independence reduces exposure to the volatility of grid energy prices, allowing producers to stabilize manufacturing costs and reduce finance risks.
Lower carbon footprint: Renewable sources like solar PV make use of natural and renewable inputs to generate power. This helps the manufacturer reduce their carbon footprint by a large margin compared to using grid electricity to supply their requirements, as desired by sustainability goals and regulatory needs.
Option 4: Applying sophisticated energy purchasing strategies
Electricity and gas, like other major commodities, are traded daily on open markets by a network of traders. Many manufacturers rely on fixed contracts, committing to energy supply for 12 to 36 months based on prices set on a single day. While this approach provides some budget certainty, it also exposes businesses to risks from market price fluctuations.
A more strategic alternative is a flexible purchasing framework. This method allows manufacturers to make energy purchasing decisions over an extended timeframe, capturing opportunities during favorable market conditions and unlocking potential cost savings.
Given that energy is a significant expense for manufacturers, it should be managed with the same level of sophistication applied to other large-scale procurement decisions. By leveraging flexibility and market insights, manufacturers can better manage risks, reduce costs, and enhance operational efficiency.
Spotlight of Silverline office equipment:
Silverline Office Equipment, a leading manufacturer of office furniture, partnered with Advantage Utilities to enhance sustainability and reduce energy costs. Through a comprehensive audit, Silverline implemented Solar PV panels, voltage optimization, and a flexible purchasing framework. These measures resulted in a 58 percent reduction in energy consumption, cutting CO2 emissions by 172 tonnes, and achieving cost savings of £671,753 in 2022.
With economic pressures set to continue, manufacturers should look to tried and tested solutions to bring down their energy costs. From site audits and more efficient infrastructure, through to renewable generation and sophisticated energy purchasing, manufacturers should follow in the example of Silverline Office Equipment as evidence of what’s possible – significant savings and impressive sustainability gains.
Dr. James Crosby-Wrigley
Dr. James Crosby-Wrigley is Head of Sustainability for Commercial and Industrial Energy Supply and Usage at Advantage Utilities. With a Ph.D in Geochemistry, Geological and Earth Sciences/Geosciences from the University of Cambridge, Dr. Crosby-Wrigley now offers business support to a range of companies looking to achieve net-zero and manage their energy costs through sustainable energy solutions.