The future is predictive: How advanced analytics are transforming maintenance
Sitting under the overarching banner of an asset performance management (APM) approach, predictive maintenance has the potential to revolutionize how industrial assets are operated and maintained. Advanced analytics applied to real-time sensor and operational data can predict failures before they occur, optimize maintenance schedules, and drive significant improvements in key performance metrics like downtime, costs, and sustainability.
We’ve reached an inflection point where the maturity of digital technologies and availability of industrial Internet of Things (IIoT) data have made predictive maintenance a reality across all types of assets and industries.
The benefits are clear. On the one hand, predictive maintenance can anticipate conditions that could lead to unexpected equipment breakdowns, process deviations, environmental emissions, or harm to personnel. On the other hand, such tools encourage resource-efficient production by detecting early signs of excessive process variability and disturbances that could lead to off-spec products or catalyst decay.
The demand from operators is steadily increasing – they want solutions focused squarely on driving business value through improved reliability, efficiency, and sustainability. Vendors must demonstrate how their technologies directly address challenges like reducing unplanned downtime, cutting maintenance costs, and optimizing asset performance.
It’s no longer enough to tout novel algorithms or technologies. Success comes from applying domain expertise to translate predictive insights into optimized maintenance plans and operational procedures customized for each unique process and asset. The focus must be on tangible outcomes, not technologies.
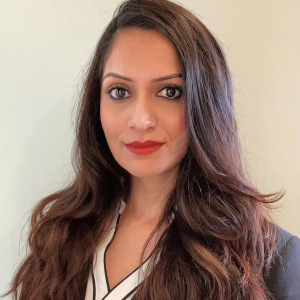
Scaling the barriers
While the benefits of predictive maintenance are well established, adoption challenges remain. Legacy assets lacking sensors present an instrumentation hurdle that can be expensive to navigate.
Overcoming change resistance also requires demonstrating how digital solutions empower, not replace, workers by giving them new tools to do their jobs better. Vendors must make technologies intuitive and valuable for all roles from operators to executives.
Other barriers include integrating predictive insights across complex, interconnected processes and translating predicted failures into optimized schedules factoring in inventory levels, skills availability, and optimal timing for repairs. Addressing these challenges will accelerate the transition to a new paradigm of proactive, predictive, and prescriptive maintenance.
New technologies are also emerging that will further enhance predictive capabilities. Advances in machine learning and artificial intelligence are enhancing anomaly detection, failure prediction and root cause analysis. Augmented and mixed reality applications are bringing predictive insights directly to technicians in the field through mobile devices and smart glasses. The ‘digital twin’ concept synchronizes virtual asset models with real-time data for continuous optimization of performance.
Finding a way forward
As technologies mature and proven outcomes accumulate, predictive maintenance is gaining acceptance beyond early adopter industries like oil and gas, power generation, and metals and mining. All operators now recognize they must embrace such solutions to remain competitive in an era of rapid change. Those who view digital transformation solely through operational or cost lenses will miss its potential to revolutionize processes and business models.
Looking ahead, entire plants and processes will become ‘self-optimising’ – continuously monitoring asset conditions and automatically adjusting operations to maximize reliability and performance based on predictive insights. Technologies will empower a new generation of workers that expect intuitive, mobile-first experiences.
Success will go to those who integrate predictive maintenance into overall digital transformation strategies and sustainability goals. Only through such holistic approaches can operators address today’s imperative to improve efficiency while reducing environmental impact. The future of maintenance is predictive, and that future is now.
By Pratibha Pillalamarri
Pratibha Pillalamarri is Senior Manager, Global Product Marketing at AspenTech, a global leader helping industries at the forefront of the world’s dual challenge meet the increasing demand for resources from a rapidly growing population in a profitable and sustainable manner. AspenTech solutions address complex environments where it is critical to optimize the asset design, operation, and maintenance lifecycle. Through its unique combination of deep domain expertise and innovation, customers in asset-intensive industries can run their assets safer, greener, longer and faster to improve their operational excellence.