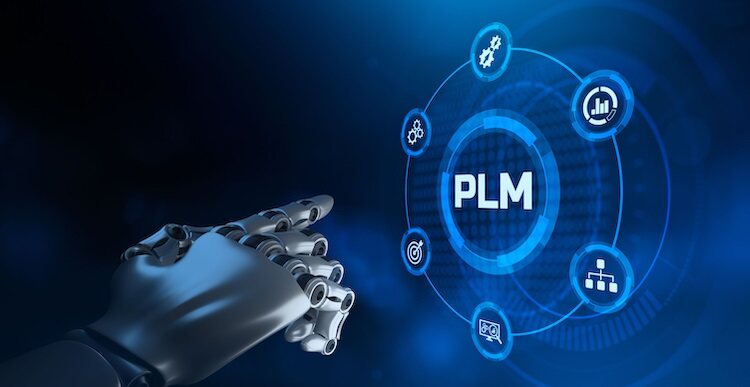
The future of product lifecycle management: trends reshaping manufacturing
Innovative digital technologies and the increasing demands of product development and manufacturing are driving significant changes in Product Lifecycle Management (PLM). Once perceived as a mere engineering-focused product data management solution, PLM is now seen as an indispensable infrastructure driving end-to-end product development lifecycles. As we look to the future, several key trends are redefining PLM and reshaping the future of manufacturing.
Digital thread vision evolves to align with PLM realities
The initial vision of the Digital Thread aimed to provide manufacturers with complete traceability throughout the product lifecycle, enabling cross-functional teams to collaborate in real-time with up-to-date product information. However, the current reality is different. Access to data in closed, legacy systems has been a major barrier to extending the thread across the enterprise. Industry leaders have adapted by developing more targeted digital threads for specific phases of the product lifecycle.
These partial threads, while limited in scope, can play a key role in justifying additional investment. Business users should easily be able to imagine the additional value a more complete Digital Thread could provide. However, it’s clear that the traditional notion of a monolithic Digital Thread is impractical. The concept must shift to enabling these isolated threads to link to one another virtually. The full Digital Thread will span many systems and many organizational boundaries but will be held together with an additional layer of federation.
PLM’s shift to the cloud
In today’s fast-paced world, technology advancements are reshaping the way products are developed and increasing their complexity. This complexity is not only changing the way we approach PLM but also overtaxing the corporate data center environments that have traditionally hosted digital engineering software.
As companies attempt to keep up with these increased demands, they are turning to advanced technologies like AI and immersive tools such as Augmented Reality and Virtual Reality to enhance collaboration and integration across their PLM systems. However, this shift poses several challenges, including concerns about security, adaptability of systems, and the need for specialized expertise.
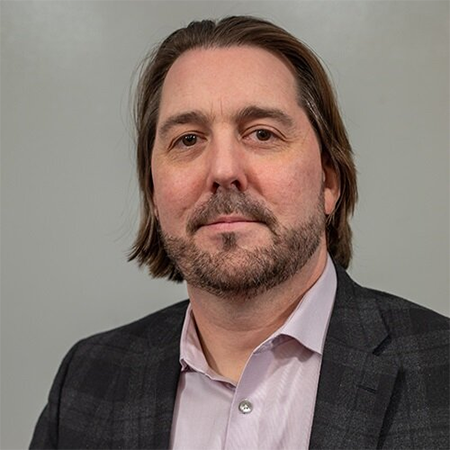
To overcome these hurdles, organizations are seeking out PLM solution specialists and turning to SaaS deployments. This strategic shift not only offloads the burden of managing IT functions but also ensures smooth operations in an increasingly complex technological environment.
Digital thread to unlock AI’s potential
Gartner predicts that by 2026, more than 50 percent of PLM vendors will have incorporated GenAI capabilities in selective functional areas. There is no disputing that AI is emerging as a game-changer in PLM, promising to completely revamp digital engineering and manufacturing processes. However, despite this potential, only 14.6% of companies currently use AI in their manufacturing operations, highlighting a significant untapped opportunity.
The fragmented nature of engineering data within organizations is one of the biggest reasons why AI hasn’t been more widely adopted. This restricts our ability to deliver a larger value across the product lifecycle. To overcome this challenge, companies can establish a robust Digital Thread framework that seamlessly connects disparate workflows and data sources, encompassing both structured and unstructured data.
The integration of AI into the Digital Thread can open many possibilities within manufacturing. By leveraging AI’s predictive capabilities, companies can anticipate maintenance needs, optimize supply chains, and drive product innovation. Through sophisticated analysis of customer feedback and market trends, AI allows manufacturers to make data-driven decisions that align with evolving consumer preferences and market dynamics.
Evolving data governance requirements
As product functionality has become increasingly software-driven, manufacturers are facing new challenges when navigating the myriad of regulatory compliance requirements. These requirements are scattered across various sources, including stacks of documents such as PDFs and diverse data repositories like DOORS or Jama. Distinguishing between design-specific requirements from stakeholders, systems models, and general design space exploration adds another layer of complexity.
The inability to pinpoint the exact set of product-related and country-specific regulatory compliance requirements poses significant risks for manufacturers. It increases the likelihood of either overdesign, leading to unnecessary expenses, or failure to obtain approval due to missed requirements, potentially resulting in life-threatening accidents. Given the complexity of requirements and their constantly evolving nature, demonstrating compliance during verification and audits is essential for manufacturers.
The future of PLM in manufacturing will depend upon manufacturers effectively integrating these trends. By navigating the evolving digital ecosystems, harnessing advanced technologies, and prioritizing comprehensive data governance, manufacturing companies can create a path towards innovation, efficiency, and sustainable growth.
By Rob McAveney
Rob McAveney is CTO at Aras. For the past 20 years, he has focused that passion on building rich software platforms that solve difficult business problems for major industrial companies. Rob acts as Aras’ technology visionary and provides design oversight for future PLM technology, while remaining grounded in the realities of configuration management, systems integration, and the many other challenges of delivering enterprise software. Prior to Aras, Rob led technical sales engagements for Eigner, an early entrant in the PLM market. He began his career at Boeing, where he gained a broad understanding of engineering and manufacturing systems and processes.