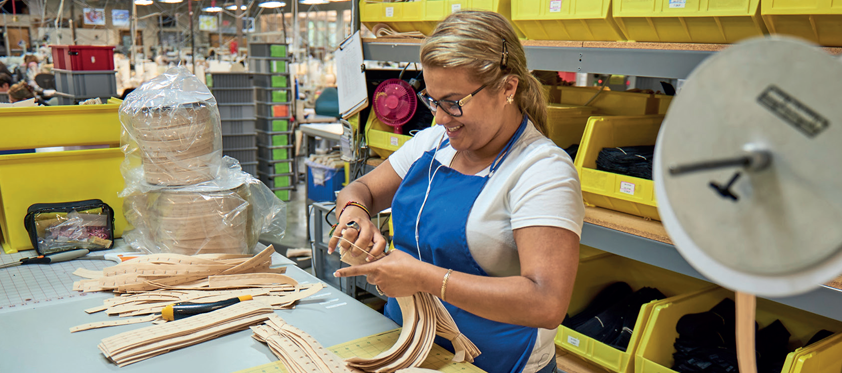
The Marena Group
The mask crusaders
Harnessing its years of experience in the manufacture of medical-grade compression garments, The Marena Group has turned its expertise to the creation of masks and gowns, to assist in the fight against Covid-19
Having commenced operations over a quarter of a century ago and starting from a humble garage, The Marena Group (Marena) now employs over 200 members of staff and serves customers in over 58 countries around the world. Created by the company’s founders Bill and Vera Watkins, the breakthrough product for Marena was a patented fabric, from which they designed and made medical-grade compression garments for use after surgery. Working closely with both leading US textile mills and surgeons, Marena continued to test its new inventions and improve patient comfort and care through innovation, winning a variety of awards along the way, and introducing products such as shapewear and activewear to its product line. In 2015, the company received private equity investment to enable its next level of evolution, and by 2016 it was partnering with NASA to develop compression garments for astronauts, and embarking on new medical and retail partnerships.
Already a US Class 1 medical device manufacturer, and no stranger to innovation, Marena was ideally placed to get involved in the response to the coronavirus pandemic. Nevertheless, its first foray into mask manufacture had a somewhat unconventional start at the kitchen table of Linda Burhance, VP of Product Development, as Dale Clendon, President and CEO of the business explained: “Linda’s career has spanned clothing and fabrics as well as medical devices, and she is a rock star in that world,” he began. “Back in March, just as Groupthis was starting to happen, and the wearing of masks came to the fore, Linda realized that the characteristics of our fabric in terms of it being cool, comfortable, wearable and easy to put on made it ideal for masks. So, she developed and designed a mask in her kitchen at home and came to me and said ‘I think we can do this.’
“I believed we needed to sell $100,000 worth of masks to make it at least worthwhile to the business – and no sooner had I said that, people started coming out of the woodwork asking for masks and when we started reaching out to businesses we discovered that the demand was actually huge!”
New opportunities
In fact, requests for its masks escalated to such levels that Marena had to create a new manufacturing facility from an existing warehouse, and form a relationship with a contract manufacturer in Mexico, too. “We thought we were trying to maintain our business and help some people, but it just went kind of crazy!” exclaimed Dale. “We had the credentials with our medical background, which gave us a lot of credibility, and we did spend a lot of time educating the buyers, which really helped us as well. We were supplying to a lot of businesses that were trying to get their people to continue to work during the pandemic, or get them comfortable so they felt able to get back to work, and some of the larger organizations literally had unions saying they weren’t going to work if they didn’t get protection. So, we have made masks for really large global business companies like General Mills and UPS, some of which we branded for them – we were in the right place at the right time I think!”
In just a few short months the company has sold millions of masks and this has now also lead the business into the area of gowns too. “We could transfer our garment manufacture expertise into this segment and because we are already a Class 1 medical device manufacturer we meet all the requirements and the diligence that is required so it has spawned another whole new business for us,” added Dale.
Going quickly from zero to over a million in terms of production numbers is not an easy process at the best of times, but add in a global pandemic and traditional processes like materials sourcing bring in a new batch of challenges to overcome. “For the masks, we are using our own unique, patented material, which includes a lot of Lycra and is warp knitted, which meant that we had to locate other warp knitters to create enough raw material, and we had to find other components as well, and this was extremely difficult,” agreed Dale. “As we have gone into the gowns side, we have found the same thing, where we have had to do global searches for materials, both on the reusable and disposable side.” This pursuit for materials revealed some unorthodox suppliers, particularly from the automotive sector. “We have found that a lot of the manufacturers who make fabrics for cars actually create very unique textiles that can meet the requirements for reusable and disposable gowns, which is highly regulated,” Dale revealed. “Another challenge was that many American companies and hospitals wanted to source their raw materials from America rather than the Far East, so we needed to find these materials close to home as well.”
The team at Marena took these challenges in their stride, because as Dale explained, not only were they getting to help people in a dire time, but they were also contributing to the continuing success of the business in what were very difficult circumstances. “I would say that my team here at Marena has been incredibly motivated and excited, and we created a lot of camaraderie and a tremendous amount of enthusiasm as we really felt like we were doing good things for a lot of people,” he stated. “Also, our suppliers were not only looking to help from an altruistic perspective, but they have a lot of employees as well and they need to make a living.”
From speaking to Dale and hearing of Marena’s continually expanding plans, the company’s suppliers will be very busy going forward. Mask production continues at pace with new products for children gaining in popularity by the day – for example, the State of Indiana recently purchased a million masks from Marena for all its children from first grade through to high school. “Our children’s masks come in three different sizes and ours are anti-flammable and they have to be comfortable for kids, too. We believe that is an underserved area and we are looking at doing education programs for that as well, to explain to children why they need to wear a mask – we are looking at developing a mascot and materials for teachers and schools in order to alleviate some of the confusion around mask wearing,” Dale highlighted.
“We are also in the midst of launching a material that is treated with an anti-viral and anti-bacterial coating, which kills any viral or bacterial material that comes into contact with it. It was created during the Ebola outbreak and given its ability to kill 99.999 per cent of bacteria and viruses we think in a consumer environment it would make people feel a bit more comfortable, particularly for children. You can rewash it up to 50 times and it still has the potency on the mask.
“Another area where we are in discussions with a large university and a defence contractor is on a project where we are using some science to try and make an N95 mask out of a new material that we believe that could make it into a reusable product. That has never been done for an N95 before, and that has got us heavily involved with a whole lot of new people and areas and is creating a lot of new opportunities for us.”
Environmental impacts
Not content with introducing new innovations into the mask segment, Marena is keeping its focus on the compression garment side too, where it is investigating incorporating therapeutics into recovery products so they would deliver a form of pain medication while being worn. “This wouldn’t be a narcotic, but medication to reduce pain when you come out of procedures,” Dale noted. “That is new horizon and we have got a technology that would allow us to do that, so we will be looking at that in the future and expanding into other areas, as well,” he added.
As mask wearing becomes more commonplace and countries such as the UK enforce more rules about wearing these products in shops and public places, the environmental impact of disposable masks is becoming an issue that will have to be addressed. To this end, another of Marena’s activities is continuing to highlight the benefits of reusable masks and gowns – the company historically has always manufactured reusables, and while it is venturing into disposables with its gown manufacture, Dale and his team believe that reusable is the way forward. “Globally the gown business before the pandemic was about seven billion dollars a year, and they say it may be as much as ten times that now, so you can only imagine how much landfill that creates,” he said. “With reusables you can use them multiple times at pennies per use, so you reduce your cost and your waste and they are also biodegradable at the end of their life. We just think that is the right way to go and we have never made disposables up until now, so we believe that reusable is the future in the way the world is today.”
Having been extremely busy over the past four months, not just meeting many new manufacturing challenges but also checking in with staff working at home, participating in companywide Zoom meetings and making sure employees are rewarded for their hard work under such difficult circumstances, Dale now has his eye on the future, where he sees infection control products as a permanent addition to the Marena portfolio. “We have created an opportunity and I believe a quarter to a third of our business will be in PPE/infection control kinds of product, which I see as normal business going forward,” he confirmed. “We hope to make some acquisitions both in the US and globally to add technologies to our set-up, so that we can leverage our existing access to 58 global markets, and introduce our products to more people. For a small company our global reach is fairly rare and by continuing to look at acquisitions that can make us a bigger player we can look at our manufacturing and our cost situation and get to customers in markets that we are not in today.”
As Dale looked forward to the coming years, Marena’s mask production numbers look set to climb to new heights, especially in the short-term, as with no national policy, it is up to individual US States to decide their approach to masks, and the number of States with a mask mandate is rising quickly. “It is great to be busy, but the circumstances are tragic and while it is good business, it’s not what we want in our hearts,” Dale confided. “We will help while we can and it is good for business, but at some time we hope that we can maintain this business in a normal world. We do think that people’s behaviour will probably change and in the West the propensity to wear masks will become much higher. We believe there is probably a retainable piece of the business, but probably nowhere near what it is now and that is fine with us!”
The Marena Group
Products: Medical grade compression garments, masks and gowns
www.marena.com