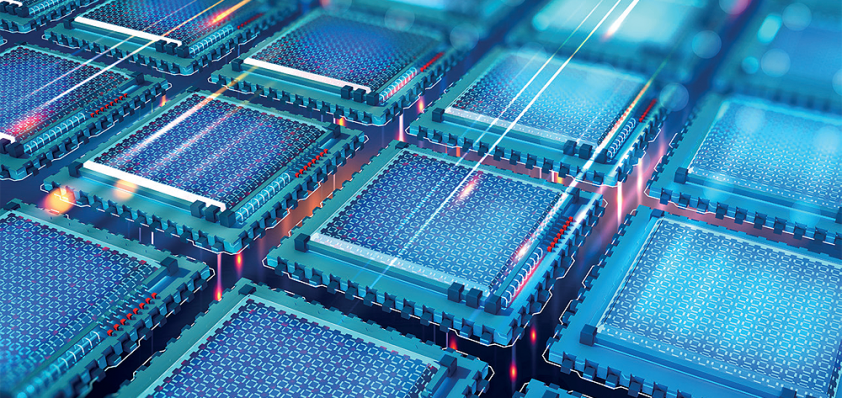
The rule of two
As we continue our march into the 21st century, we enter the golden age of digitalisation. We have access to unprecedented volumes of data, powerful analytics and computational processing power; but this is only the beginning. In March 2020, Honeywell announced that it is on the cusp of releasing the world’s most powerful quantum computer, which will be up to 100,000 times faster by 20251. However, even with this level of processing power, our industry still faces a number of significant hurdles.
Unplanned downtime continues to plague the process industry, with a recent report showing that in one year, crude distillation units in the refining industry experienced more than ten years of combined unplanned downtime2. While many organisations balance break-fix and timed maintenance regimes, advanced ones are looking to digitised reliability and optimisation initiatives to reduce unplanned downtime and increase throughput.
Supply and demand imbalances are impacting profitability. As feedstock sources and qualities vary, organisations are forced to change process unit configurations to handle them. Added to this, demand cycles for finished products are changing more rapidly, leading to significant shifts in final product pricing and margins. Industry leaders are using digitalisation initiatives to optimise their plants and maximise profitability based on changes in supply and demand.
CO2 reductions are becoming a focus for the industrial sector. It is estimated that the energy, electricity and industrial sectors contribute more than 60 per cent towards global CO2 emissions3. Governments entities such as the European Union are beginning to mandate reduction targets4, and industry participants such as BP are responding5. Digitalisation is seen as a key enabler to drive emission reductions in the industrial sector without large capital investment6.
Vital knowledge is leaving our industry and replacing it is a challenge. We are dependent on the expertise of experienced engineers, many of whom are nearing retirement age. Added to this, the average tenure of employees in single roles and organisations is reducing. This means that untapped knowledge is at risk of being lost and will become difficult to maintain and build on in the future.
When talking to process engineers about overcoming these challenges, many say that in an ideal world they would be able to see inside their process unit and know the unit’s dynamic constraints, bottlenecks and additional capacity. Knowing this would allow them to anticipate operational changes and respond accordingly before upsets occur. If a process engineer had a digital twin of their process unit, they could better respond to a number of the challenges their industry faces.
Let’s take a step back for a moment to consider the concept of a process digital twin. At Honeywell, we define a process digital twin as digital representation of a physical asset that is configured to respond just as that physical plant or asset would in the field. The concept of a process digital twin is not new, and has been evolving since the 1970s in the form of process simulation. What has changed in recent years is the ability for these high-fidelity process models to be fed with real-time plant data and augmented with industrial cloud ecosystems to uncover and seize opportunities to increase throughput, decrease downtime, and optimise production and energy consumption in near real-time.
So, what is possible when an industrial plant leverages the power of a process digital twin enabled ecosystem? Let’s take a real-life example of a refinery in Europe which sources crude feedstocks from more than 25 countries around the world. The level of variation in crude qualities presented the refinery with significant challenges in maximising production yields and impacted their profitability. This organisation was executing a company-wide digitalisation initiative with a focus on projects with direct impacts on efficiency and reliability.
The organisation partnered with Honeywell to deploy a process digital twin for a single process unit of the refinery. This project aimed to increase product yield and unit throughput by capturing process knowledge, and leveraging the underlying process model to enable improvement opportunities such as increasing catalyst performance and alleviating the coke to make constraint on the unit.
The deployment consisted of:
- Data uplift: Real-time process and laboratory data from the refinery is uplifted to a cyber-secure, cloud-based ecosystem.
- Data cleansing: Advanced data cleansing routines are executed including data correction, mass balance reconciliation, data conditioning, component balancing and simulation to ensure that the best information is used as a basis for further processing
- Digital twin execution: Cleansed data is run through the digital twin to determine the current operation against expected operation
- Fault model processing: Outputs are fed through fault models to trigger any early event detection along with appropriate resolutions
- Visualisation: The results from digital twin execution and fault model processing are presented to users in the form of dashboards to drive situational awareness and improve understanding of constraints and opportunities.
According to the refinery, the deployment and inputs from process experts enabled the refinery to increase unit catalyst performance and adjust other operating parameters to increase yield and profitability by $1.45 million per year. The refinery is also evaluating other recommendations that will increase throughput and provide an additional $5.6 million per year in benefits.
As stated in the Progress Global Survey, 59 per cent of respondents are concerned they are too late with digitalisation efforts and will fall behind competitors7. With many advanced organisations already reporting significant benefits from Process Digital Twin Enabled Industrial Ecosystems, the time for digitalisation is now!
1 https://www.cnet.com/news/quantum-computer-will-get-100000x-faster-by-2025-honeywell-says/
2 Oil Digitalization, BloombergNEF, September 2019
3 https://www.iea.org/data-and-statistics/?country=WORLD&fuel=CO2%20emissions&indicator=CO2%20emissions%20by%20sector
4 https://ec.europa.eu/clima/policies/strategies/2050_en
5 https://www.bp.com/en/global/corporate/news-and-insights/press-releases/bernard-looney-announces-new-ambition-for-bp.html
6 https://www.iea.org/reports/digitalisation-and-energy
7 https://www.progress.com/docs/defaultbp.com/…/news-and-insights/press-releases-source/default-document-library/landing-pages/dach/ebook_digitaltransformation_final.pdf
Nathan Simiana
Nathan Simiana is Product Marketing Manager, Honeywell Connected Enterprise, Industrial. Honeywell is a Fortune 100 technology company that delivers industry-specific solutions that include aerospace products and services; control technologies for buildings and industry; and performance materials globally.
www.honeywell.com