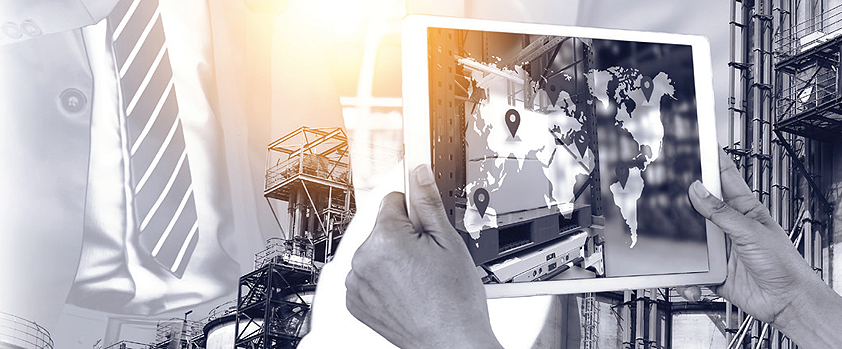
The right resources
So why are manufacturers slow about fully getting on board and will that change in 2020 and beyond asks James Kemp
We are on the cusp of an Industry 4.0 revolution. A brave new world where computers and technology are connecting and communicating to share real-time data for a more efficient, productive and safer factory and supply chain.
Yet the ultimate dream of this Connected Factory, as it is known, where processes end-to-end are interconnected, streamlined and optimised through technology, still feels a long way off for many manufacturers.
The UK in particular lags behind the Industry 4.0 curve, though surprisingly the US is yet to catch up with Europe and Asia according to a recent World Economic Forum and McKinsey report (Fourth Industrial Revolution Beacons of Technology and Innovation in Manufacturing).
What we are seeing is that many manufacturers are still only realising the huge potential of this technology, or are just beginning to take tentative steps towards a fully connected factory.
As global manufacturers such as BMW, Bosch and Tata Steel, who have already embraced the Connected Factory model demonstrate, there is a world of possibility for manufacturers as the technology evolves and advances at an incredible pace. Hardware and software that enables automation, analytics, Internet of Things (IoT) and digitisation, so that manufacturers can connect and maximise their whole value chain, are already a reality for some.
Why now?
The Connected Factory will be put into even sharper focus as labour and energy costs continue to rise and global competitiveness intensifies. As manufacturers feel these burdens, they will no longer be able to put off the inevitable; having to install and use these new technologies to make their assets work harder and more efficiently.
However, as compelling and exciting as that sounds, it won’t be easy as there’s certainly no simple, short-term or cheap solution to implement and to get it right. Every manufacturer will have different resources, expertise and requirements proving that there’s no ‘one-size-fits-all’ approach.
We deliver complex engineering projects and capital works programmes for clients in UK, Europe and beyond across a diversity of sectors from food and drink, advanced manufacturing to energy, so have seen first-hand the barriers and challenges that clients face when trying to integrate this technology into their operations to achieve greater connectivity.
Breaking down the barriers
For many manufacturers cost is still the single biggest factor in slow or failed adoption of connected factory technology. In cases where they have Why now?
The Connected Factory will be put into even sharper focus as labour and energy costs continue to rise and global competitiveness intensifies. As manufacturers feel these burdens, they will no longer be able to put off the inevitable; having to install and use these new technologies to make their assets work harder and more efficiently.
However, as compelling and exciting as that sounds, it won’t be easy as there’s certainly no simple, short-term or cheap solution to implement and to get it right. Every manufacturer will have different resources, expertise and requirements proving that there’s no ‘one-size-fits-all’ approach.
We deliver complex engineering projects and capital works programmes for clients in UK, Europe and beyond across a diversity of sectors from food and drink, advanced manufacturing to energy, so have seen first-hand the barriers and challenges that clients face when trying to integrate this technology into their operations to achieve greater connectivity.
Breaking down the barriers
For many manufacturers cost is still the single biggest factor in slow or failed adoption of connected factory technology. In cases where they have Through the continual monitoring and integration of data from across all areas of the site, valuable insights such as around energy usage, production speeds, wastage, maintenance and safety, can all help manufacturers boost productivity, reduce lead times, eliminate errors and improve output quality.
However, there is no point having reams of data without the right software or resources in place to optimise its potential. We have seen instances where manufacturers have spent considerable money upfront gathering data only then to not know what to do with it or have the resources to fully capitalise on its invaluable insights.
This is why taking a holistic approach is crucial. Having clear objectives and targets to aim for, a robust strategy to deliver these and the right people and expertise in place up front will help to ensure a good return on investment is realised. Without these essential project management resources then the technology and its outputs essentially become redundant.
What is also crucial is that senior management understands the breadth of resources needed to make their investment in technology worthwhile – this could be upskilling existing engineers, appointing a head of efficiency and making sure their outcomes are aligned to overall business objectives and are management driven.
As Elon Musk famously said in a tweet: “Excessive automation at Tesla was a mistake. To be precise, my mistake. Humans are underrated.”
What’s next?
There’s a myth that only big global players with huge budgets can afford and achieve Connected Factory status, but this is not true. With the right systems, resources and foresight in place, even small- and medium-sized manufacturers can and will begin to seize the opportunity for continuous improvement and leaner manufacturing through advanced data analytics.
We are likely to see the cost of the cost of this technology fall over the coming decade and as pressures of energy costs, sustainability and labour intensify, more manufacturers will be turning to technology. So perhaps that dream of a Connected Factory will become a reality for many more manufacturers in this new decade – I hope so.
James Kemp
James Kemp is Managing Director of Pentadel Project Management, a company of architects, engineers and project managers supporting clients throughout the UK, Europe and globally with the smooth, timely and cost-effective delivery of complex engineering projects and capital works programmes. Whether a client is planning a new development, the extension of a current facility or the modification of a newly purchased building, the Pentadel team has a strong track record of delivering entire projects from concept to commissioning.
www.pentadel.com