The supply chain’s supply chain needs integrating. It’s finally starting to happen
Manufacturing supply chain integration typically evokes the exchange of data about materials, components, subassemblies, and final products as they take shape for the marketplace. Another dimension of supply chain integration gets less attention: the exchange of data to improve the efficiency, flexibility, and operation of the factory equipment that makes those products. That is, the integration of the supply chain that creates the supply chain.
There’s a consortium for that. Factory-X, funded by the German Ministry for Economic Affairs and Climate action, involves 56 companies, associations, and research institutions. They’re focusing on 11 use cases. While some have to do with supply chain traceability and integration as more commonly understood, several of those use cases are about improving shop-floor operations through better data exchange among those who make, set up, operate, upgrade, and maintain the systems and machines of that let manufacturers live up to their names.
The Factory-X consortium’s use cases are diverse. They range from boosting transparency and consistency of production equipment-related information to
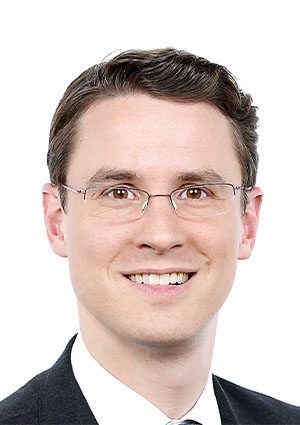
traceability of machine components to simplifying production setup and control. Let’s take a closer look at one of those use cases: Under the banner of ‘collaborative information logistics,’ it focuses on tackling the inefficiencies that emerge because of the lack of standards in how companies exchange data about manufacturing assets.
Making life easier for shop-floor personnel
Consider the plight of the maintenance manager on a modern production line. The line involves an array of material-handling equipment, fabrication and processing machines, assembly equipment, and quality-control machines from different vendors. Each machine has different sets and formats of documentation, maintenance instructions, and spare-part information, all on different websites. In addition, there’s the matter of managing and scheduling the updates for all the different software releases for many machines. Keeping track of it all via vendor websites takes a lot of the maintenance manager’s time and effort.
Two dynamics further complicate the challenge. First, shop-floor equipment is becoming increasingly complex and, often, more integrated with other equipment on the line. That integration is a good thing. But that complexity does make it harder to reprogram, reconfigure, and maintain, and repair production assets, and integration boosts the odds of a problem with one machine cascading to others. Second, an aging manufacturing workforce has seasoned talent retiring in larger numbers, putting complicated and consequential maintenance and repair in less-experienced hands.
Sharing data boosts production efficiency
The idea behind Factory-X’s collaborative information logistics and several other use cases is to enable the exchange of information about production assets using common data standards to enable communication between component/material producers, package-unit makers, those running the package units in production, and outside service providers repairing and maintaining the units – across any platform. It boils down to improving production fundamentals to minimize downtime and keep factories running more efficiently.
Doing so will let users such as our maintenance manager access specific, updated data on assets at the serial-number level in one place. That means they’ll be able to avoid the time and effort of searching for, confirming, tagging, and otherwise dealing with scattered, potentially dated information about all the different machines on the production floor. The maintenance manager, operators, and others will have current, accurate information on the documentation, digital nameplate, precise components, technical components, and spare parts of a machine, as well as specific maintenance or integration needs that each production asset needs to run effectively on its own and in harmony with other machines up and down the line.
Further, AI can improve the efficiency and effectiveness of the maintenance manager’s routine tasks. For example, the system can learn which maintenance activities have been conducted in response to identified issues and can suggest maintenance activities, parts, and special tools required as the maintenance manager creates a new maintenance order.
Production-asset-chain integration is happening
Many individual business supply network platforms already share production-asset-related information supporting proven industry standards in identification, data modeling, classification, and technical interfaces (including ID-Link (IEC 61406), VDI 2770, and ECLASS). However Factory-X aims to take the next step, enabling smoother collaboration between the different vendor platforms and incorporating new standards and concepts such as Asset Administration Shell. Prototypes are underway, with collaboration between OEMs and component makers, software developers, and package-unit makers as part of Factory-X collaboration on an actual production line. The lessons will apply to other proofs of concept, pilots, and, with time, to full production ecosystems across many manufacturing verticals.
There’s been much attention paid to supply chain integration and the traceability, visibility, resilience, efficiency, agility, and sustainability it promises to deliver. Rightly so. Factory-X’s core philosophy, too, is that good things happen with better data exchange. Given increasing asset complexity, growing workforce skills gaps, and the efficiency and productivity gains to be won, manufacturers should embrace the integration of the production-asset supply chains that supply chains depend on.
For a list of the sources used in this article, please contact the editor.
By Daniel Krampe
www.sap.com
Daniel Krampe is an industrial manufacturing solution expert at SAP. SAP is a German multinational software company that develops enterprise software for managing business operations and customer relations. SAP stands for Systems, Applications, and Products in Data Processing. SAP is the world’s largest provider of enterprise application software.