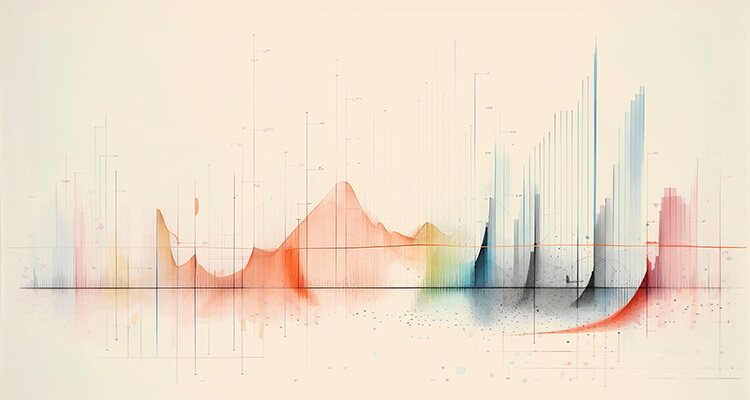
The top four strategies to maximize tech impact
Why do some smart factory initiatives succeed, and others fail? What makes the difference between good and bad technology adoption? These questions are more pressing today than ever.
Research firm Gartner says more than half of manufacturers (54 percent) will increase technology spending by at least 10 percent in 2024 and that business intelligence and analytics software are top priorities as manufacturers transition to smart factories.
Make UK echoed Gartner’s findings in its 2024 Executive Survey, which shows accelerating technology use to improve manufacturing efficiency, productivity and environmental performance.
Multiple factors are driving adoption. High energy costs mean more manufacturers are exploring how to run machines more efficiently, and most manufacturers now recognize that technology offers the best route to greater productivity and prosperity.
And, importantly, technology providers are better attuned to the needs of most manufacturing businesses.
Previously, manufacturers wanting new technology such as machine monitoring had to invest tens or hundreds of thousands of pounds in complex enterprise-scale systems requiring expert installation, integration and configuration to work within their IT infrastructure.
Today, cloud computing and low-cost IoT devices have driven adoption at scale. Manufacturers of all sizes can now adopt the digital tools they need at a scale that is right for them.
However, a lack of experience in adopting technology and business cultures unfamiliar with embracing it hamper transformation. Many manufacturers don’t have teams dedicated to finding and evaluating new tools, and almost half of those surveyed by Gartner expressed regret over recent technology purchases, citing higher-than-expected costs, implementation issues and insufficient functionality.
My company, FourJaw Manufacturing Analytics was founded in 2020 with a vision to maximize manufacturing productivity around the globe. Today, we are trusted by over 120 manufacturers of all sizes in sectors including aerospace, automotive, energy and food production.
For many, adopting our technology is their first foray into ‘Industry 4.0’, so we’ve spent time thinking about how to de-risk adoption and enable manufacturers to achieve the best returns. Those who approach digitization with the right mindset achieve the biggest productivity gains and payback for their investment.
In practice, we see that successful projects have four common themes:
Focus on the problem, not the technology
Adopting technology for technology’s sake is unlikely to generate genuine improvements. Smart manufacturers focus on the problem they want to solve. All technology comes with a learning curve, so it is critical to focus on an issue that those on the shop floor and the top floor agree needs addressing to overcome the inevitable cultural inertia that happens when adopting new technology. How manufacturers use technology can be subtly different for different challenges, so that focus helps to ensure it delivers clear and immediate benefits.
Start small, then scale
Nothing kills technology initiatives like over-ambition. Moving too fast too soon creates more risk, wastes resources and causes projects to grind to a halt as people struggle to see the wood for the trees. Smart manufacturers focus on quick wins first, such as boosting productivity and reducing energy use in a small number of manufacturing cells or production lines. This can be used as a springboard to inspire further improvements. Cloud technologies make it easy for manufacturers to start small with tools such as machine monitoring, enabling them to make initial process improvements on a handful of machines, and replicate that success factory-wide once they have the knowledge to do so.
Measure everything objectively
The adage about managing what you can measure is truer today than ever. Still, production decisions in many factories continue to be informed by a combination of gut feeling and hearsay. Most manufacturers don’t know their productivity levels accurately, why they’re losing productivity, or what to prioritize to improve. Proactive manufacturers start with an objective view of what’s happening on the shop floor that they may observe in real-time and over periods of time. They establish benchmarks to evaluate progress, highlight unknown issues and support better resourcing and technology investment decisions.
Make progress part of company culture
It is impossible to overstate how influential culture is when adopting technology. Forward-thinking manufacturers encourage a culture of innovation and make an effort to make new technologies part of the furniture. FourJaw customer, Hydrafeed, for example, quickly made analytics part of its culture through weekly meetings in which managers and machine operators reviewed production data together and used it to determine how they could boost performance in the next week. They have developed a continuous-improvement mindset among their teams to ensure everyone is invested and aligned with the business goals and objectives, resulting in improved productivity and, ultimately, profitability.
As manufacturers incorporate digital tools into their operations, the key to successful adoption lies in pausing for thought and thinking strategically about how best to proceed. Rising adoption must be accompanied by real focus for manufacturers to thrive and remove the element of risk that comes when starting the journey towards ‘smart factories’.
For a list of the sources used in this article, please contact the editor.
Chris Iveson
Chris Iveson is CEO of FourJaw Manufacturing Analytics. Founded in 2020 as a spinout from the University of Sheffield’s Advanced Manufacturing Research Centre, FourJaw is a UK-based SaaS company empowering manufacturers of all sizes to enhance productivity, reduce energy usage and grow more profitably. FourJaw’s plug-and-play machine monitoring platform integrates seamlessly with machines of any age or brand and is trusted by over 120 manufacturers globally, operating in sectors including aerospace, automotive, energy and food production.