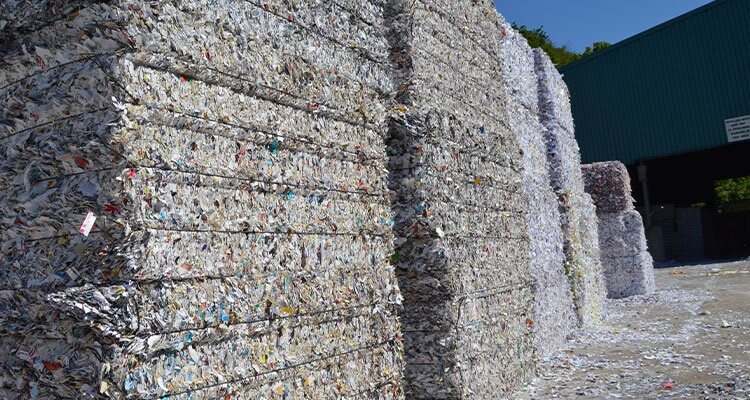
Through constant adaptation, Fourstones Paper Mill proves that centuries-old businesses can successfully embrace sustainability
In the ever-evolving world of manufacturing, Fourstones Paper Mill (Fourstones) has weathered many storms, transitioning through the ages, and more recently emerging as a beacon of sustainability and professionalism in the paper industry.
Tracing its roots back to 1763, Fourstones was founded by William Charnley, initially producing paper for the book industry. The business has witnessed and survived many historic events, including the American Revolution and both World Wars. While its ownership has changed hands over the years, the company’s resilience, commitment, and ability to adapt has been the key to success.
Its product offering has evolved over time, adapting from newsprint to filter paper and cellulose wadding. The turn of the millennium marked a significant moment in the company’s history with a management buyout (MBO) led by Peter and Pauline Duxbury. Recognizing the changing landscape within the paper industry, the Duxburys made a strategic decision to transition towards tissue paper grades for hygienic paper disposables.
This transformative shift led to remarkable growth, increasing turnover from £2.5 million in 2000 to an impressive £50 million in 2023. Today, Fourstones operates on three sites, employs 180 staff, and is renowned within the UK paper industry as a quality supplier. Peter Duxbury, Managing Director, joins us to share the company’s story of not only survival, but also remarkable success.
“Growing from a small operation has allowed us, the owners, to be at the heart of the business with a strong team around us and an emphasis on clear communication,” Peter begins. “Our openness and flexibility have enabled us to be responsive to market changes at a much quicker pace than larger organizations with large management structures. We have a better vision of the entire company, which means we can build relationships with employees and more easily recognize areas for improvement.
“We currently operate two UK-based paper mills; one in Northumberland, England, and one in Fife, Scotland. Across the two sites, we run three paper machines, which are capable of manufacturing 32,000 tons of 100 percent FSC recycled paper every year. We have a fourth paper machine currently being installed, which we predict will double our annual production output.
“To put it simply, we supply paper reels to converting customers and finished paper disposable products to UK wholesale and distribution customers. Paper reels consist of low grammage tissue, cellulose wadding, and a selection of other specific paper grades, all of which are manufactured from UK paper waste supplies and certified as 100 percent FSC recycled.
“While we don’t currently manufacture virgin pure cellulose paper, our intention is to produce virgin paper on our new paper machine,” he outlines. “We plan to source the pulp for this new grade of paper from reliable and ethical sources, as we hope to maintain our status of exclusively supplying FSC certified paper. Also, the machine is expected to run at speeds of 1700 meters-per-minute at a width of 2750 meters, achieving an additional 30,000 tons of paper every year.”
The eight-figure investment involves not only the purchase of the new machine, but also upgraded works to the stock preparation system, effluent plant, electricity supply, and civil works. “In addition to the machine itself and the necessary infrastructure improvements, we’ve also invested in four additional converting lines to accommodate some of the additional product we expect from the machine,” Peter reveals. “We’re already experiencing improved efficiencies and quality outputs from upgrading our systems, and we’re also installing a rewinding unit to allow us to combine one ply reels for more compact converting operations.”
Green commitment
Returning to the company’s product offering, Peter continues: “In addition to paper reels, we’ve diversified our product range by converting paper into finished goods in-house, using integrated converting operations on both our paper mill sites and at our additional converting plant in Northumberland. Our Sapphire, Purdi, and HONEST finished goods ranges are supplied to hundreds of UK distributors, servicing janitorial, medical, industrial, and beauty markets.
“These ranges consist of center-feed, AFH toilet tissue, medical couch rolls, and domestic toilet rolls to name a few,” he elaborates. “We’ve always aimed to provide reliable and consistent products using our own paper supply without compromising on quality. Over the years, we’ve also been known to create paper for other applications, from incontinence care to oil filter and agricultural wiping products. This approach has enabled us to build a loyal customer base and develop a positive reputation in the industry.”
Notably, in 2021, Fourstones launched HONEST, a disposable paper range with significantly reduced chemical usage, to address concerns over the paper industry’s environmental impact and promote sustainability. “Utilizing our knowledge of paper manufacturing, we were very aware of the chemicals used, of which many converters are oblivious,” Peter explains. “That’s why we launched HONEST, to combat the use of chemicals and spark a conversation about how we can minimize the environmental impact of paper manufacturing.”
The company’s commitment to sustainability has not gone unnoticed, instead earning it a nomination for a Sustainable Manufacturing award. “As a company specializing in recycled paper manufacturing before ESG became a mainstream focus for most businesses, we’ve always taken the environment seriously,” Peter reflects. “Core to our shortlisting is our genuine belief that businesses should operate with integrity and honesty.
“It’s no secret that paper making requires a huge amount of raw material, chemicals, water, and energy; we’ve always been upfront about this and never ‘greenwashed’ our offering. Instead, we’ve taken actions to ensure we continuously reduce our environmental impact. Rather than buying green energy, we’ve invested in our own energy generation with on-site hydro turbines and heat recovery systems.
“We’ve also taken part in a 2023 UK Government pilot for ISO 14064 greenhouse gas emissions reduction,” he reveals. “We’ve submitted a full carbon emissions report that will be audited by a credible third-party auditor. Once we obtain our certification, we’ll continue to work with the pilot to produce a carbon reduction plan that will also be externally audited to ensure consistent progress on our route to becoming carbon free.”
Future upgrades
As our conversation draws to a close, the topic turns to the company’s future. “We expect big things in 2024, starting with the commissioning of our new paper machine in Q2,” Peter concludes. “We’re also in the process of adapting the business for our next growth cycle, which will require some structural changes to ensure we remain agile and competitive moving forwards. This includes major upgrades to our IT system, and we’ll also soon be announcing the outcome of our carbon reduction journey, so we will certainly be a company to look out for in the coming months.”
Having Peter at the helm with his hands-on knowledge of paper manufacturing, combined with the company’s constant reinvestment strategy and dedication to ethical practices, Fourstones is sure to experience continued success in 2024 and beyond.