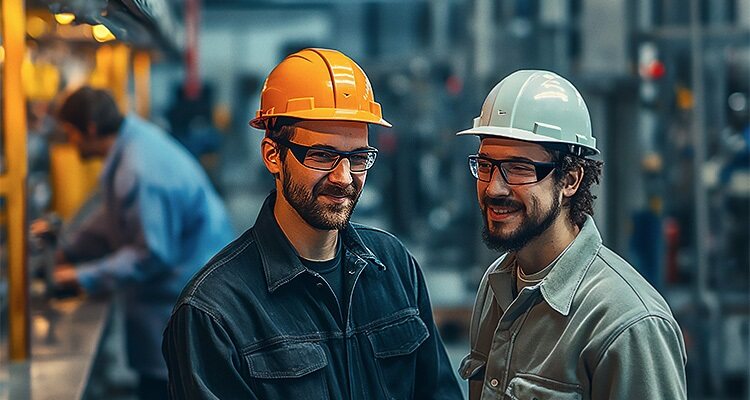
Tom Mercer’s predictions for the top manufacturing trends of 2024
As we start a new year, there are mixed feelings about what 2024 will bring for the manufacturing industry. From sustainability to supply chains and automation – businesses across manufacturing must learn to adapt and innovate to ensure they can deliver what their stakeholders want.
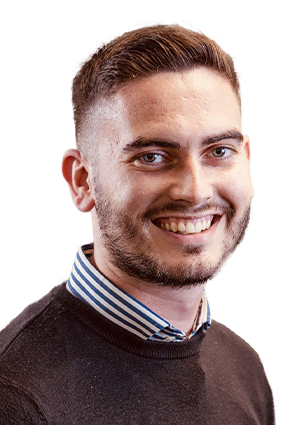
A green and cleaner year ahead:
In 2024, we will see a further push for greater sustainability across the manufacturing sector. While environmental benefits will remain a key driver, companies will also turn to greater sustainable measures to increase operational efficiencies and reduce costs. Sector-wide, the pressure from their customers for companies to adapt to more climate-friendly practices will continue to be a big motivator. We will see a greater divide between companies spearheading innovation and sustainability and those needing help to adapt. For survival, companies and organizations can only respond to the call for greater transparency by investing in sustainable practices and processes.
Also, as net-zero targets become another year closer, manufacturers must be fully aware of their carbon emissions and what they can do to minimize the impact. This can be done by measuring energy consumption, the size of the premises, and how much travel is included in the manufacturing processes. Some top ways of reducing emissions quickly are by setting up company-wide recycling schemes, switching to renewable energy providers, or even buying offsets from companies that allow customers to fund carbon-reducing projects like solar energy or wind farms.
Welcome to the 4th Industrial Revolution:
Industry 4.0, the ‘4th industrial revolution’, is a huge talking point within manufacturing, which will become louder over the next year. With increasing pressures on bottom lines, continued trouble with logistics capacity and a sheer lack of workforce – I expect we will see more manufacturing companies turn to AI/IoT/automated robotics to protect their future, increase output quality, and reduce the reliance on people.
A switch to AI and automation does take time – so the earlier steps are taken towards innovation, the better. Manufacturers can quickly begin a digital overhaul by focusing on ensuring connectivity within the production premises is ready for expansion to newer and more demanding systems and that cyber security measures are robust.
Companies must fully embrace automation operationally to stay ahead. The increase in the use of smart tools within businesses to automate simple but repetitive processes, alongside the rising pressure to increase staff retention in a shortage of talent market, will drive streamlining and automation across manufacturing.
Delivering across a supply chain:
The manufacturing industry is feeling the pinch because of a consistent shortage of materials, high energy costs affecting production – and the inevitable disappointed customers who haven’t received what was promised.
Most manufacturing businesses are experiencing disruption in their supply chain, so building long-term resilience in 2024 will be crucial to survival – and growth.
By diversifying supplier lists as much as possible and ensuring complete visibility within a supply chain – ideally being able to pinpoint the location and track the moment of individual materials/parts – and using prior reliable data to predict need – supply chains will become more efficient, cost-effective, and reliable.
Team morale:
In a traditionally low-paid and high-turnover job market, team morale is a critical factor in production quality and punctuality, and this year will be no different. We’ve spoken to a few manufacturing firms that want to drive a unique and positive culture within their business to retain key staff and attract staff from competitors. But their biggest hurdle is improving team morale before introducing a new culture.
At GAINLINE, we work with manufacturers to encourage them to adopt a regular and open conversation policy throughout their business. This also helps to ensure people are praised for hard work (verbally and through incentives) and that all employees are challenged to ensure they don’t get bored of their roles. Adapting these simple behavior changes can quickly implement a culture shift.
As we are still seeing an exodus of people leaving companies that have requested staff to be in the office full time, I think there will be more debate around how managers can better meet remote workers’ needs and what remote work culture is whilst recognizing disengagement amongst remote staff. ■
Tom Mercer
gainline.co.uk
Tom Mercer is Commercial Director at GAIN LINE, a business consultancy run by a senior team that has spent the last 15 years transforming businesses – from household names to industry leaders and everything in between. With offices in London and Manchester, GAIN LINE’s mission is to prepare and guide the businesses of today through to tomorrow by delivering cutting-edge digital solutions and business consultancy solutions.