Unlocking success through digital transformation
Reflecting on 2023, the manufacturing field saw a visible shift in focus. Industry 4.0 and automation emerged as prominent themes within the manufacturing sphere. These topics sparked conversations centered around fine-tuning processes, implementing predictive maintenance strategies, and harnessing the power of real-time data to drive efficiency to new heights. Furthermore, the adoption of digital twins, serving as virtual replicas of physical systems or products, gained traction across the industry.
In a testament to resilience and adaptability, the UK manufacturing sector stood out in terms of outcomes, achieving an impressive output of £224 billion. This achievement propelled the sector from 9th to 8th place in the global manufacturing rankings, solidifying its position as a significant industry player. Amidst the tide of technological innovation, UK manufacturers embraced automation and robotics, strategically aligning their operations with the objectives of Industry 4.0.
Despite its triumphs, the year also presented its fair share of challenges. Global financial uncertainties cast a shadow over the manufacturing sector, triggering a ripple effect of adverse consequences that impeded production processes. Tariffs and sanctions exacerbated the situation, causing shortages in raw materials, surging costs, and disruptions in production timelines. Other hurdles, including geopolitical tensions, advancements in automated technology, and shifting attitudes towards Environmental, Social, and Governance (ESG) principles, have collectively reshaped the manufacturing landscape.
Anticipating heightened challenges
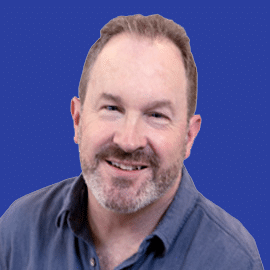
The State of Production Health report sheds light on a pressing concern facing 23.3 percent of manufacturers: the imperative to upskill their workforce. This challenge is no surprise considering the prevalent use of outdated technology which has highlighted a significant skills gap within the workforce when transitioning to Industry 4.0 and even 5.0 capabilities. As advancements continue to reshape the manufacturing landscape, addressing this gap becomes increasingly urgent to maintain competitiveness and innovation.
In the UK, 36.7 percent of manufacturers say their biggest challenge is grappling with the task of successfully adopting new technologies. This hurdle not only impedes organizational growth but also places strain on the workforce. Compounding this challenge are issues related to an ageing workforce and immigration restrictions, exacerbating the difficulty in attracting and retaining young talent. In contrast, EU countries demonstrate greater success in balancing worker rights and promoting worker engagement and safety, underscoring the need for the UK to adapt its approach to remain competitive on the global stage.
Moreover, 21.7 percent of UK manufacturers face rising materials costs due to persistent disruptions in supply chains. Balancing costs amidst heightened demand poses challenges in meeting customer expectations and maintaining operational efficiency. Addressing these issues necessitates proactive strategies and strategic partnerships to ensure resilience and sustainability amid ongoing uncertainties.
The Year of redefining AI
Manufacturers will endure challenges and complexities as the year goes on. Familiar obstacles like skills shortages and supply chain disruptions will persist, requiring mitigation strategies like upgrading technology. Furthermore, new hurdles will emerge, including the pressing need to incorporate Industry 5.0 and AI technologies into their operational frameworks. This necessitates substantial technological overhauls and investment in cutting-edge solutions.
However, a notable shift in perspective will occur regarding AI implementation. Rather than fixating solely on the technology itself, manufacturers will increasingly focus on the processes it enables and the tangible business value it delivers. This shift signifies a maturation in the industry’s understanding of AI’s potential, marking a pivotal moment in its integration into manufacturing practices.
Despite challenges, manufacturing investment will rebound, focusing on technologies enhancing efficiency, productivity, and sustainability over capacity expansion.
There is also a growing emphasis on sustainable business practice including pressure to disclose carbon footprint and ESG credentials. This again builds on the necessity of AI technology to aid the reduction of waste and downtime to counter other costs.
Striving for success
In 2023, the industry faced challenges and uncertainties. Looking to 2024, AI adoption will take center stage, but companies must balance tech investment with talent development. Manufacturers must stay agile to navigate unforeseen challenges and capitalize on opportunities. Prioritizing innovation and sustainability will be essential for thriving in 2024 amidst ongoing transformation, positioning companies to emerge stronger in a dynamic business landscape.
By Brian Fitzgerald
Brian Fitzgerald is CRO of Augury. A leader in Machine Health and Process Health solutions, Augury uses purpose-built AI technology, trained by industry experts and the world’s largest data library, to help manufacturing and industrial companies eliminate production downtime, improve process efficiency, maximize yield, and reduce waste and emissions. Its global customers achieve 3-10x ROI, often in a matter of months.