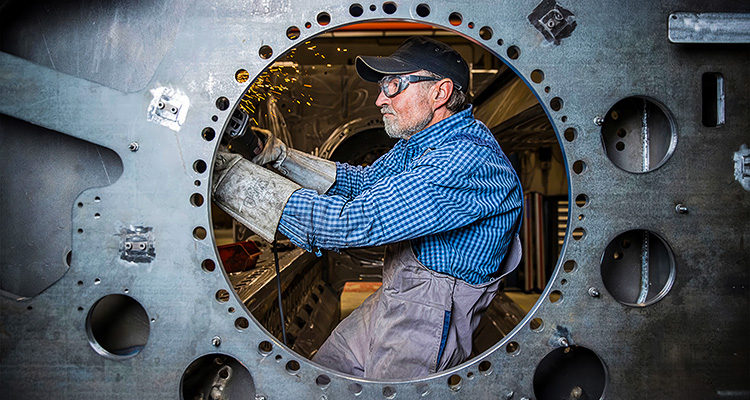
UNTHA’s Austrian engineering meets unmatched reliability to promote the circular economy
Since its establishment in 1970, UNTHA has been fulfilling a promise to do everything in its power to be more reliable than its competitors across all products and services. Renowned for state-of-the-art technology, UNTHA produces high-quality shredders that are durable, robust, and above all, reliable. The company offers a comprehensive product range that caters to countless applications, from compact wood shredders to high-performance industrial shredders specifically designed for the recovery of reusable materials. UK Sales Director, Gary Moore, shares more information about UNTHA’s operations.
“Today, UNTHA employs 500 people all over the world. All shredders are developed, manufactured, and assembled at the Kuchl site, in Austria. UNTHA shredders are used in a wide range of applications, from material recycling to the processing of residual and waste wood and the reprocessing of waste to produce alternative fuels. In this way, the company makes an important contribution towards the conservation of resources and the sustainable processing and reduction of waste. With subsidiaries in the US, UK, Poland, and Germany as well as a global sales network, the company is active in more than 40 countries across every continent. Furthermore, it boasts an export rate of around 90 percent, placing it among the world’s leading manufacturers in this growing, future-oriented industry. In addition to headquarters in Kuchl near Salzburg and an office in Vienna, UNTHA has six independent sales subsidiaries in the US, UK, Germany, Turkey, Iberica and Poland,” he begins.
As the company’s geographical presence expanded, so did its capabilities and product range. “Shredders have been our specialty since our establishment in the 1970s. We pride ourselves on continuous innovation, always pushing the boundaries to develop industry-leading machines. Nonetheless, our focus goes beyond mere advancements, as we strive to enhance energy efficiency, reduce noise levels, simplify maintenance, and ensure unmatched durability in every design. From rotor speeds to cutting shafts and gearboxes, we meticulously engineer our shredders for longevity. Our commitment to quality means our machines can operate seamlessly for decades, outlasting many competitors by six-to-seven times, especially when managing tough materials. While some may doubt the longevity of our ‘built to last’ promise, our history speaks for itself. Unlike standard machines that last only a few years, our technology endures, maintaining peak performance even with heavy duty applications. Additionally, our customer service extends beyond the initial purchase with offerings like the shredder rebuild service, enhancing efficiency up to eightfold and extending the lifespan of cutter sets. At UNTHA, we redefine return on investment by prioritizing easy maintenance, high uptime, and low whole life running costs. Businesses using our shredders not only benefit from immediate cost savings but also secure a long-term solution that stands the test of time,” Gary highlights.
In 2024, UNTHA established a new innovation center in Kuchl, headed up by Stefan Scheiflinger-Ehrenwerth, its Chief Innovation Officer. Gary explains how this project has changed the company’s operations and sheds light on the benefits it has introduced for clients. “Inaugurated in 2024, the UNTHA Technology Innovation Centre is a dedicated hub for innovation, located in Kuchl, near Salzburg. Within this innovative facility, a team of approximately 15 experts, spanning various departments, collaborates in an environment equipped with offices, workshops, and mini-production and assembly halls. This setup enables us to swiftly construct prototypes and conduct immediate testing. Central to the center is an open innovation space strategically positioned within our prototyping zone. This unique arrangement not only facilitates internal collaboration among our technicians and engineers but also fosters early engagement with customers and industry pioneers for valuable feedback. By involving end-users and stakeholders from the outset, we ensure a direct line of communication to understand operational needs and refine technological solutions accordingly. Through this collaborative approach where insights are shared bidirectionally, we enhance our collective knowledge base and drive innovation forward,” he states.
Through its partnership with Aigner Stahlbau Verkehrstechnik GmbH (Aigner), UNTHA is advancing its expansion strategy. This collaboration not only provides UNTHA with a reliable partner in the procurement market but also enhances its manufacturing footprint at Aigner’s facility in Pöttelsdorf, Austria, thereby positioning the company for greater operational efficiency and growth in the industry. “Established in 1990, Aigner operates with a team of 45 employees and manages approximately 1500 tons of steel per year. The Pöttelsdorf site spans 10,000 square meters and includes a new 4000-squaremeter production hall. Our growth trajectory accelerated when we acquired Aigner, a company that specializes in the large-scale production of machine components that are subsequently assembled at our Kuchl facility. Due to capacity constraints at our Kuchl site, the acquisition of Aigner has allowed us to advance our expansion plans without being hindered by local limitations. This strategic move not only addressed our capacity challenges but also solidified the longstanding partnership between our companies,” Gary informs.
Across its facilities, UNTHA maintains rigorous standards when it comes to quality, all while keeping sustainability in mind. Gary discusses the approaches and techniques employed by the company to lessen the environmental impact of its operations. “We actively promote and facilitate initiatives that advocate for sustainable consumption, waste reduction, and the advancement of a circular economy. By doing so, our aim is to drive positive change for a more sustainable planet. Committed to environmental responsibility, we strive to minimize the carbon footprint of our technology and operations. To that end, our shredding technology is manufactured in a way that optimizes the reuse, recycling, and energy recovery of waste materials, championing sustainability at every stage. Likewise, our machinery is designed to enhance material separation, significantly reducing the environmental impact of waste disposal processes. In line with the principles of a circular economy, which we fully embrace, we offer innovative solutions for refurbishment and rebuilding, ensuring the long-term operational efficiency of our shredders. Furthermore, we collaborate closely with waste management experts to tailor solutions that precisely align with our unique requirements.”
Additionally, UNTHA is acutely aware of the correlation between systems and people in delivering top-quality work. “While systems provide the framework, it is the right individuals that truly make the difference, which is why we are dedicated to sourcing and cultivating the finest talent in the industry. Quality is not just a checkbox but a core value that both individuals and organizations must embody. By empowering our team members, giving them a platform for growth, and instilling this mindset across all departments, we ensure a consistent standard of excellence in every customer interaction and project engagement,” Gary ends.