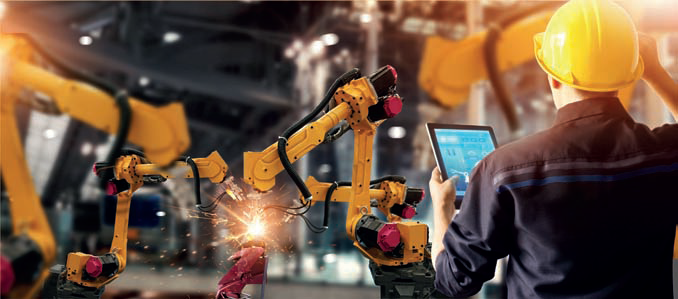
Use your data
The fallout from Covid-19 is forcing manufacturers to pivot quickly in a number of ways – moving from just-in-time to just-in-case inventory management models, addressing workforce availability challenges and rethinking approaches to employee health and safety.
To ensure business continuity, many manufacturers have adhered to their local government’s imposed measures, including split shifts to enable social distancing and prevent high rates of worker absence. Some have even mandated quarantine areas for goods arriving from ‘high risk’ countries. This, however, has had an enormous knock-on impact. Not only on ways of working but also on logistics, storage and even energy consumption of manufacturing plants.
Don’t get me wrong. The majority of manufacturers have viable business continuity plans in place. But these are short-term, based on relatively low risk or infrequent scenarios, like tsunamis or earthquakes. Without much in the way or forewarning, manufacturers are now facing a truly global crisis, likely to wreak havoc on the industry.
The United Nations has estimated a potential $50bn decrease in exports across global value chains as a direct result of the virus. And while it might be too early to draw a line on the balance sheet, the real gaps that the pandemic has exposed are clearer than ever. While manufacturers have been grappling with both supply and demand shocks, many realised that traditional supply chains are not fit for purpose. In many cases, resilience has been sacrificed for greater cost or time saving efficiencies.
Now, manufacturers need to find ways to become more agile. They need to future-proof their operations by integrating new technologies to maintain both an effective supply chain and operational workforce. Trends we have already seen emerge, such as using data analytics to drive operational efficiencies, will, and indeed must, be accelerated.
Establishing the foundation for antifragile supply chains
What we’ve seen up until now is that when companies are under budgetary pressure, they rely on data to secure buy in from the wider business. This is smart thinking when it comes to making an investment during an economic crisis. But in the face of a global pandemic, manufacturers need to be nimble and agile enough to continue operating during times of unrest.
Let me give you an example. I grew up in Lebanon, in the Middle East. Today, years after the Civil War ended, people still have access to electricity only 12 or 14 hours a day. But most of them rely on their own generators. As power production is so decentralized, this allows the system to be resistant and antifragile to unanticipated shocks. The point here is simple. The reason manufacturers are struggling to deal with the fallout of Covid-19 is because their supply systems are fragile. What this doesn’t allow them is to be flexible – for example, very few manage to use the data they have to identify and connect with alternative suppliers when there are sudden shocks to their supply chain. The overreliance on manual processes and the lack of visibility into their supply networks has created tangible impact on their production.
So, how can manufacturers retool their supply chain to find an optimal solution in times of crisis? It might sound obvious, but the foundation of an antifragile supply chain is to become digital. Data and analytics have enormous potential to modernize and transform manufacturing operations.
Yes, most manufacturers are already gathering useful data throughout their operations, but it’s essential that they use it effectively. Don’t rush out to install sensors on everything, oftentimes what you’ve got is more than enough to build a robust view of your manufacturing operations and supply chain. One way is by using what we call an Asset Avatar – AI algorithms that help simulate scenarios and take into consideration all costs, such as fuel or storage, alongside any other factors as the distribution curves in each country or city. This will allow manufacturers to consider an optimal solution and build greater resilience to mitigate detrimental effects on the operations. Gaining real-time insights into where supply chains are strained can open an opportunity to predict the risks and help diversify the available options.
Transforming the workplace for a safe return to production
A study by The World Economic Forum looking into building resilience across manufacturing, revealed that the number one priority for manufacturers is to protect their workforce. Manufacturers have already taken measures such as implementing home-working policies, pushing travel restrictions and visitor bans, or making wearing of protective equipment mandatory.
However, protecting the workforce to safely return to work should go beyond PPE. Driven by manufacturers’ reliance on human capital and the impacts of social distancing, it is critical that they maintain the safety of their workers. And this is where new technologies can be levelled up to directly solve these pain points to also benefit in the long run.
New technologies such as Light Detection and Ranging (LiDAR) are already being deployed to help ensure social distancing in manufacturing facilities as well as optimise people flow. By using thermal cameras and LiDAR technology, manufacturers can detect the temperature of a person from a distance, so that workers can be screened for symptoms of Covid-19, while workspaces can be monitored for compliance with distancing recommendations. By combining this data with existing sensor data, manufacturers can perform machine learning analysis and identify potential high-risk areas, optimise operations management, and even develop policies around what to do when an employee has a fever or hasn’t washed their hands.
Protecting human life has become even more of a priority during the pandemic. It’s essential that manufacturers look to new solutions and take a proactive approach to prevent and mitigate the impact of future pandemics.
The manufacturing industry is not only a driving force behind the global economy, but it also contributes to a better quality of life. We depend on the success of manufacturing for ensuring continued production and quality of goods, while advances in technology will ensure a safer work environment suitable for the future production systems.
Wael Elrifai
Wael Elrifai is VP of Big Data, IOT & AI at Hitachi Vantara, a wholly-owned subsidiary of Hitachi, Ltd. Working alongside each customer, Hitachi Vantara applies its unmatched industrial and digital capabilities to their data and applications to benefit both business and society. More than 80 per cent of the Fortune 100 trust Hitachi Vantara to help them develop new revenue streams, unlock competitive advantages, lower costs, enhance customer experiences, and deliver social and environmental value.
www.hitachivantara.com