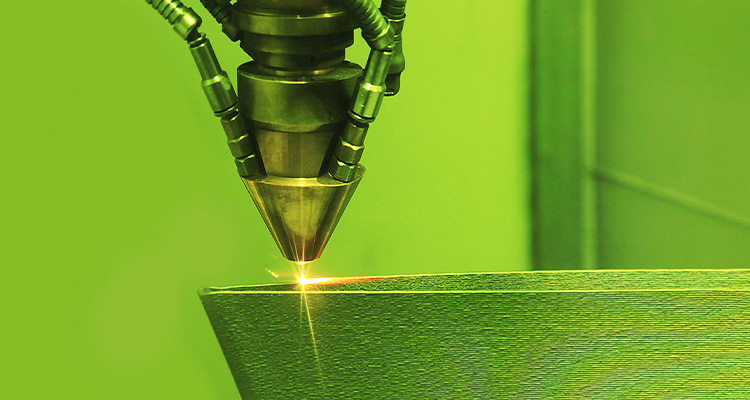
What’s the future for 3D printing asks Chris Tuck
Additive Manufacturing (AM), more commonly referred to as 3D Printing (3DP), has been part of the manufacturing landscape for over 30 years. It was initially developed as prototyping technology (referred to as Rapid Prototyping) to speed up the development of products in a range of sectors, from automotive to consumer goods. The layer-by-layer nature of the technology caught the imagination through the ability to manufacture complex geometries without the need for tooling and reduced manual intervention. In the early 2000’s the technology was first mooted as a potential manufacturing technology for end-use parts by
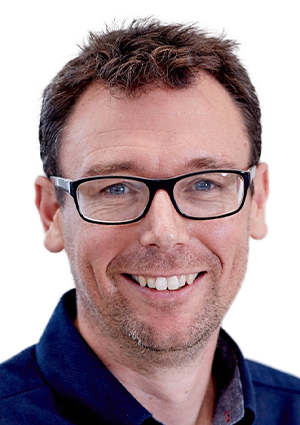
researchers in the UK, EU and North America. Conventionally, these machinery and processes were limited to plastic materials, but the advent of high-power laser and electron beam systems saw advances in the development of metallic, and to a degree, ceramic processes for the direct production of parts.
These advances in the early 2000s ignited significant interest in AM/3DP as a method to produce highly functionalized components that could have higher
performance. For example, using design optimization tools or coupling with 3D scanning techniques to produce customized geometries that were individual to the user. This saw significant uptake of AM/3DP in healthcare devices, aerospace and automotive industries enabling added value to products in often demanding environments.
However, penetration into the wider manufacturing base has been hampered for several reasons. Firstly, an often-cited panacea for manufacturing technology, the view that ‘you could build anything’ was always naïve, and those that bought into that premise were often disappointed. In fact, just as with other more traditional manufacturing technologies, AM/3DP has its own set of rules and limitations that need to be understood, advanced and implemented through design, manufacturing and post-processing of components that are intended for end use, something that in the Rapid Prototyping days were not really an issue. This requirement to have better understanding of the manufacturing constraints and the lifecycle of components has become one of the harder barriers to overcome and one that has proven costly for those implementing these technologies within their manufacturing operations. However, where the business and technical cases are clear there are numerous examples of success, whether it be for metallic or plastic parts and products.
One of the key drivers for AM/3DP has been trust, whether this is related to the process reliability and repeatability or in the material properties that are a result of the manufacturing process. An important aspect to remember for this technology is that the material properties of the final component are a result of the process, in a similar way to a casting or injection moulding process, especially where thermal energy (i.e. melting based) processes are used.
These two aspects have seen the bulk of research and development activity for the last ten or so years, identifying ways of controlling the process to ensure part accuracy, distortion and the material properties of the components produced. In addition, there has been a need to improve on the variety and availability of materials for this process to enable production in varying sectors. An area that has seen large increases in materials development are the metallic processes, where once they were limited to a small range of steel and titanium alloys, the last ten years has seen a large increase in development, in aluminum, copper and even magnetic alloys. The polymer machines, especially those based on powder materials, have seen less development due to the material constraints and the ability to prototype small batches of material for research and development.
AM/3DP has seen a cooling of prominence and some turmoil in the commercial arena over the last few years, however, the research agenda and the relevance of the technology has never been higher. Now considered a ‘tool in the toolbox’, AM is a viable technology across a range of new sectors, including space, defense, medical implants and consumer goods and apparel. As such the research agenda is focusing on the next generation of technologies, ones that are more sustainable, reducing waste in both part and process, to provide reliable and repeatable material properties, that can be tailored to design need. Longer term, the development of multi-material AM/3DP processes looks to be a gamechanger, producing entire systems with significant additional functionality in the part through the incorporation of functional materials, such as pharmaceuticals, electronics, biological or optical componentry.
Chris Tuck
Chris Tuck is Professor of Materials Engineering in the Centre for Additive Manufacturing at The University of Nottingham UK. Ranked 24 in Europe and 15th in the UK by the QS World University Rankings: Europe 2024, the University of Nottingham is a founding member of Russell Group of research-intensive universities. The University is among the best universities in the UK for the strength of our research, positioned seventh for research power in the UK according to REF 2021.