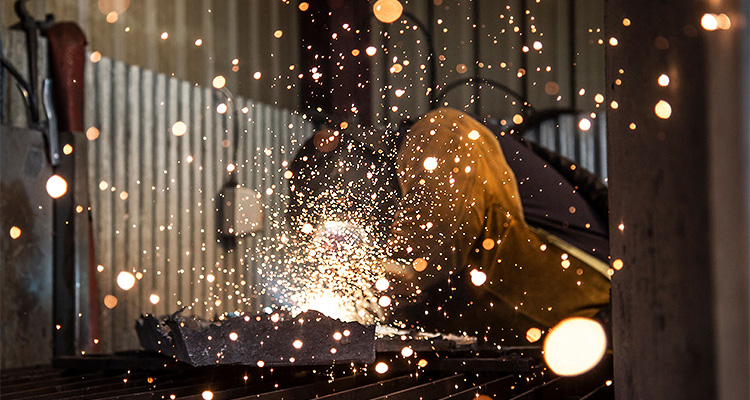
Why Advanced Alloy Services is focused on recycling processes, UK innovation, and global growth
As superalloy revert specialists and suppliers of high purity and superalloy metal, Advanced Alloy Services (AAS) has earned a strong reputation across the industry for buying, selling, and processing high-temperature alloys and metals. Since its formation in 1993, the business has grown significantly and has been recognized by the Yorkshire Fastest 50 initiative for the last two years.
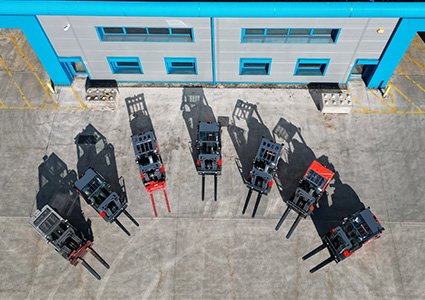
Stephen Hall, Managing Director, elaborates on the company’s history and evolution. “Alan Fisher, the founder of AAS, originally worked in one of the superalloy industry’s most recognized and pioneering companies, Ross & Catherall, now part of the Doncaster’s Group, who remain a customer to this day,” Stephen begins. “Alan saw an opportunity to build his own business and supply the growing UK superalloy production market, so in March 1993, he formed AAS with the backing of four investors and a total of £60,000.
“Over the last 30 years, AAS has grown into a leading privately owned, independent supply company with 40 employees and a turnover of more than £50 million. Alan remained MD for over 23 years until 2016, when I joined and took over the company’s day-to-day operations. The business continued to expand rapidly,
and we moved to a 44,000-square-foot purpose-built facility in 2017.
“In 2018, Alan retired from the business, shortly prior to the completion of a management buyout in 2019, which saw me take full ownership and control under Advanced Alloy Services (Holdings) Ltd. Shortly after, AAS formed a joint venture (JV) with Revert Alloys & Metals (RAM), called Advanced Revert LLC (AR), to further enhance international trade, with a specific focus on the US market.
Award recognition
Turning to the company’s capabilities, Stephen continues: “We source high purity critical metals, test and processes revert (a term used to refer to recycled superalloy scrap), and provide services used in the manufacture of nickel and cobalt based superalloys to companies around the world. These superalloys are used in the most demanding engineering applications, such as aerospace, power generation, automotive, oil and gas, medical, defence and space exploration. In a world focussed on sustainability and circular economy, AAS completes the recycling circle.”
Having received the King’s Award for Enterprise – International Trade in 2024, we’re keen to hear Stephen’s reflections on such a monumental achievement. “Since 2019, the world has gone through several ‘once in a generation’ events like Covid-19, Brexit, shipping crises, the war in Ukraine, a cost-of-living crisis in the UK, as well as government changes in both the US and UK,” he shares. “Navigating these events as a new business owner has been immensely challenging, so it was amazing to be recognized for the King’s Award, the first award the business ever entered. The award is fantastic recognition for the AAS team and our combined efforts to cope with challenges and come out stronger.”
Thinking about the wider industry, Stephen explains how AAS is supporting the trade of critical metals. “I have supported the UK Government and Critical Mineral Intelligence Centre in the assessment of metals and their supply chains for many years,” he explains. “We were key contributors with Rolls-Royce on the aerospace alloys report and we manage a large metals recovery project for Rolls-Royce on a global basis, which has already returned millions in value.
“We plan to partner with Rolls-Royce for further R&D work on metal recovery, and the processes we’re developing will have significant potential for other businesses in the supply chain where alloys containing critical metals are used. We hope to quantify the carbon savings of recycling and recovery processes of critical metals versus the massive carbon emissions from overseas mining and refining operations. From prior studies, it’s estimated that the saving could be as much as 98 percent, which will be a significant driver for innovation within recycling and recovery processes.
“While the UK is recognized as a global leader in innovation, many large companies do not always embrace innovation due to perceived risks, stretched resources, approval structure, and concern about shareholder value. In a world now focused on critical minerals and metals, it’s soul-destroying to see examples of poor recycling and revert processing.
“AAS, however, is committed to supporting UK innovation. We’ve supported a PhD student for a couple of years, and we’re excited about the Knowledge Transfer Project with Coventry University and Innovate UK. We are trying to develop a process of recovering critical metals from superalloys using bioleaching technology, which would develop new or better routes of recycling and recovering metals, as well as supporting the resilience of UK supply chains and reducing the environmental impact from primary mining operations.”
Global presence
As our conversation ends, Stephen turns his attention to the company’s growth strategy moving forward. “We want to establish a footprint in the UK, US, and Asia, as this combination will enable us to source and deliver to any of our customers quickly and efficiently,” he shares. “To bring together the different entities under one recognized umbrella, we’re forming Advanced Alloys Group.
“We have a new JV project starting this year with the opening of a brand-new factory in Asia. This location will provide a perfect platform to process some of the material we source from Asia and for us to further expand sales in the region. We’re also expanding our capabilities in the US with investment and development of AR. We’ve installed processing equipment to enable us to source and process material domestically within the US, rather than coming to the UK first.
“With the development of the US business, our JV in Asia, and the creation of the Advanced Alloys Group to cement the development of our global presence, we have a busy year ahead,” Stephen concludes. “Within the next five years, we hope to see a well-established global presence of Advanced Alloys Group around the core Advanced Alloy Services Ltd business. We believe that this will incorporate new innovative processes for better metal recovery and recycling and ultimately, we hope to be able to license this technology to other companies.”