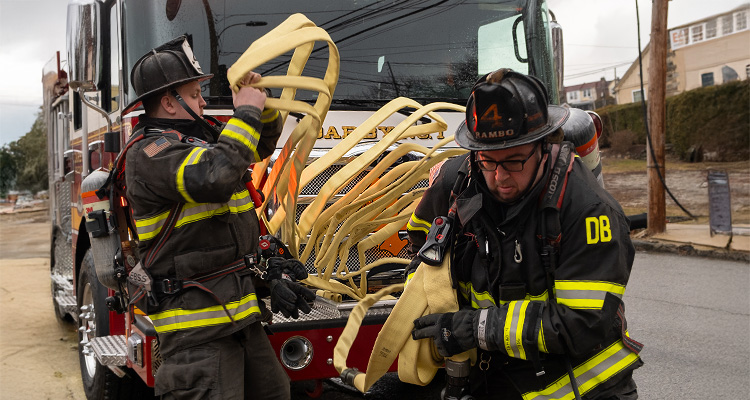
Why Snap-tite Hose’s dedication to quality and innovation extends beyond manufacturing
As one of the largest lay-flat hose manufacturers in the US, and the only one to be ISO 9001:2015 certified, Snap-tite Hose (Snap-tite) provides hose for municipal, industrial, forestry, military, and agricultural applications. With the user depending on the hose in vulnerable or life-threatening applications, Snap-tite prioritizes reliability, quality, and durability of every single hose, regardless of its application.
Having focused primarily on the municipal sector in recent years, Snap-tite has elevated industry standards for both quality and safety, designing products through collaboration with firefighters to ensure the hose not only meets requirements but can withstand tough conditions. However, the company has recently launched new products to target growth in other critical markets. Snap-tite’s agricultural hose caters to the industry’s unique demands, for instance, and is designed to optimize efficiency in challenging farming environments.
In early 2024, James Novinsky joined Snap-tite as CEO, and has since taken the business to new heights, transforming internal processes, upholding quality standards, and refining the approach to customer service. We sit down with James to learn more about Snap-tite and the impact his leadership is having on operations.
“My career before Snap-tite was very different; I worked for a subsidiary of Bosch, Bosch Home Appliances, and was fortunate to spend two years working in Morrocco before the pandemic,” James begins. “I believe that everything happens for a reason, and when Covid hit, I knew it was time for a change. I was considering getting into the nonprofit sector before I was approached with the role at Snap-tite, and I started talking to my eldest son, who is a volunteer firefighter, and found his stories fascinating.
“I have huge respect for the fire industry, and I knew I wanted to help create and innovate the best possible products. Now that I’m in the role, I know that Snap-tite is my purpose and it brings me great joy and pride to know that our products have helped save lives. I’ve taken this passion one step further in my personal life too by training to become a volunteer firefighter and assist the amazing people fighting every day.”
Quality criteria
Turning to Snap-tite’s portfolio, James continues: “Our products are made differently according to the conditions in which they will be used. The Warrior™ hose, for instance, is the only UL Type 1 fire hose in the industry, designed to withstand extreme heat and is difficult to burn or puncture. The agriculture sector, on the other hand, requires a hose able to withstand movement, as farmers often need to drag hose from a tractor, so flexibility and low pressure are essential. While we have several products for each application, we strive to work with the customer to ensure we’re supplying the correct hose for each application.
“As a premium lay flat hose manufacturer, we know that firefighters depend on our products when lives are at risk. Being ISO certified means we have a rigorous approach to quality at our Pennsylvanian facilities in Erie and Union City. In fact, we give our stamp of approval by testing every single hose before they leave our buildings.”
This approach to quality also extends to Snap-tite’s supply chain. “Our suppliers are subject to very high standards, and we have internal processes to ensure quality in line with our ISO certification,” James explains. “When we receive products, for instance, they go into quarantine until we receive certification notices about specific tolerations. We also retest each material to confirm it passes our quality standards and we’ve created a corrective action process for anything that doesn’t pass. By working closely with suppliers, we outline what we’re expecting and ensure our approaches to quality are aligned.
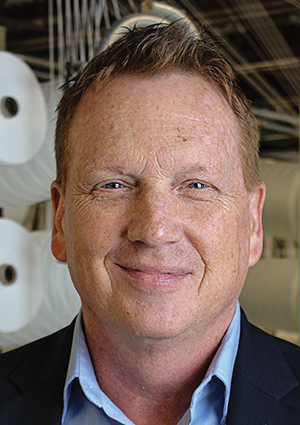
“We’re currently embarking on a lean process using Six Sigma concepts to refine our process and align methodologies across the business. We’re also upskilling our people and increasing training to aid our efficiency and productivity.
“Alongside quality, we also emphasize meaningful innovation. We’re constantly developing our understanding of the industry and our customers’ problems by networking and collaborating with others. We’ve talked with the fire industry, for example, to better understand the anatomy of fire and how firefighters must adapt their response depending on materials and external conditions. As an example, the rise in EVs poses a challenge as an EV fire requires an average of 40,000 gallons of water compared to around 500 gallons for a diesel car.
“We also consider how chemicals impact our hose and developing products that absorb less carcinogens and hazardous chemicals,” he adds. “We’re involved with absorption studies and our hose has been independently certified to contain zero PFAS chemicals by the University of Notre Dame.”
With our conversation ending, James turns his attention to the company’s current priorities and future. “Over the last 18 months, we’ve focused on employee wellbeing and development,” he states. “We want to create an environment where people not only feel valued but also look forward to work. By establishing a competitive wage scale and improving our benefits, we’ve seen a dramatic decline in employee turnover from 30 percent to just four percent. Our staff take pride in what they do, which is reflected in high morale across the team and our willingness to engage with visitors.
“2025 will be a fantastic year for Snap-tite, and we’ll begin to reap the rewards of the time and effort we’ve put into our infrastructure over the last year. When I joined, for instance, our delivery time was between 26 and 28 weeks but we’ve reduced this to just 28 days. We’ve also developed a strong foundation to manage capacity, and we’re reintroducing our agricultural, industrial, military, and forestry product lines. We’ll continue to learn and introduce meaningful innovations in 2025, and we’re also keen to educate and collaborate with customers and users of our products to continuously improve everything we do.
“Further afield, we want to pivot from being a hose manufacturer into an innovation solutions company. We’ll aim to expand into adjacent areas and focus on the application to ensure we’re providing the most effective product for its intended use. While manufacturing will always be part of our DNA, we’re aiming for the market to view us as high-quality innovators that solve problems.
“Although we’re not like our competitors, I welcome others to improve product quality and invest in certification processes, as it benefits the wider market; my only question would be what took them so long,” James laughs as our conversation closes. “Snap-tite is an amazing company with amazing people, and every day I come to work knowing that what I do genuinely matters.”
From speaking with James, his passion for the industry is clear to see, and he will undoubtedly maintain the company’s industry-leading reputation for creating innovative products that improve the market and save lives as Snap-tite continues to grow.