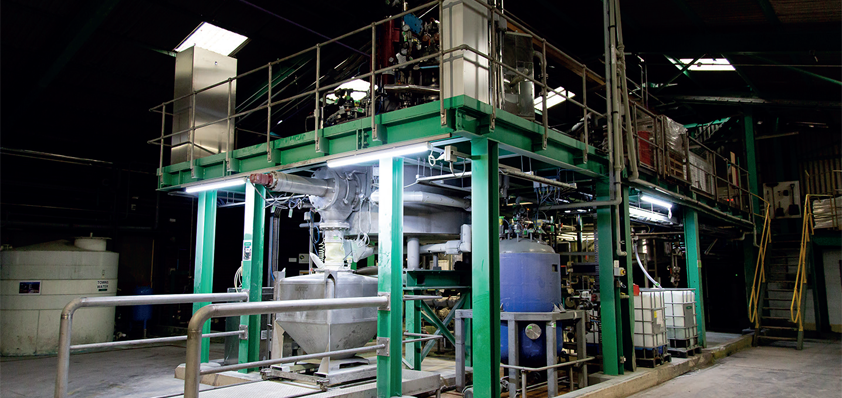
William Blythe Ltd
Chemistry for tomorrow
The year 2020 marks the 175th anniversary of William Blythe Ltd, one of the UK’s leading specialty chemical businesses and a company that has a hugely exciting future ahead of it
Founded in 1845 – in Accrington, Lancashire – William Blythe Ltd is one of the oldest specialty chemical businesses in the UK. Initially formed to produce inorganic chemicals for the local textile industry, today the company delivers specialty chemical solutions to help its customers meet modern technological challenges in markets ranging from life sciences, performance coatings and polymers, to electronics, catalysts and renewable energy.
William Blythe Limited is a wholly owned subsidiary of Synthomer plc, and with this support utilizes industry-leading manufacturing technology, which it combines with world-class chemistry R&D and analytical capabilities to cultivate an evolving portfolio of inorganic derivatives of elements such as copper, tin, iodine, zinc and tungsten. The core capabilities that it uses to create its product range are controlled bi-tri metallic precipitation, redox reactions and hydrothermal synthesis. In more recent times, the company has also worked closely with a range of customers pursuing novel applications for functionalized graphene oxide and doped metal oxides.
“One of William Blythe’s major markets is polymer additives, specifically inorganic materials that go into flame retardants in PVC and polyamide, and from those that facilitate the thermal stabilization of polyamide,” explains William Blythe’s Business Director David Crossley.
Very much an international business, some 70 per cent of William Blythe’s sales are export driven. Sales and Marketing Director, Kevin Hudson, is able to divulge exactly why the company, and its products and solutions are so well travelled. “We manufacture high purity, rigorously defined, consistent products, coupled with the ability to customize our products where the need arises. We combine this with excellent customer service and on time deliveries, which is appreciated by our customers all over the world. Furthermore, we possess a high level of expertise in controlling both the physical and chemical properties of our products, and are constantly looking at where we can offer product enhancements, and this is what drives our business forward.”
A recent example of the company’s product development efforts has been its creation of its own high capacity, granulated, finished absorbent: DURAGUARDTM. Engineered to give industry leading performance, it is designed to remove sulphur from hydrocarbon streams, and boasts unrivalled absorption capacity and durability to natural gas processing operators. In fact, such has been the success of DURAGUARDTM, that in the 18 months since it was developed it has become one of the company’s biggest drivers of growth.
The manufacturing epicenter of the company is its 26-hectare site in Accrington. “Here we have three core manufacturing plants,” David states. “We have our high-volume copper plant, where we manufacture a range of copper derivative products used predominantly in the catalyst and gas purification industries. We then have the tin plant, where we manufacture our flame retardants and tin catalyst products, and thirdly our iodine plant. Here, we manufacture our iodine specialty chemicals that go into a wide range of applications including food additives, electronics, pharmaceutical and printing.
“On site, one will also find our own effluent treatment plant, where we treat all of the effluent generated from our processes. The treated effluent is then discharged directly into the sewer under strict controls that we adhere to under our IPPC (Integrated Pollution Prevention & Control) and trade effluent consent permits. As an Upper Tier COMAH (The Control of Major Accident Hazards) site we have a lot of experience in handling hazardous chemicals such as bulk chlorine, hypochlorites and hydrazine, which gives us a unique opportunity to handle most hazardous chemicals and work with those who want to manufacture products that require high hazard raw materials.”
The aforementioned effluent treatment plant is also a critical element in William Blythe’s scale up of its new advanced materials activities, particularly those with graphene oxide, which produces a lot of acidic effluent that has to treated. “When it comes to graphene oxide, we first identified that our capabilities would fit nicely with manufacturing this advanced material back in 2015,” David continues. “We quickly scaled up production to pilot levels, and have already secured commercial sales as a polymer additive where the unique properties of graphene oxide give significant benefits in the end application. We are also working on a large pipeline of opportunities for a wide range of applications which will deliver significant growth in the near future. With the strong future of graphene oxide clear, we are committed to the scale up of this new material and have plans in place to expand current capacity from hundreds of kilograms to over one ton per year in 2021.”
A second advanced material that William Blythe has spent considerable time developing is its LUXACALTM product range. LUXACALTM is a doped tungsten oxide nanomaterial used in ‘inkless’ digital printing and as an active material for the absorption of radiation in the near infrared (NIR) wavelength range. “We developed this specifically for a client that wanted to make use of a new printing technology which required a NIR absorber to absorb laser energy, transform it into heat, and cause an image to appear,” Kevin says.
While the company had no direct previous experience of manufacturing such a material, the R&D team looked at all possible routes and established that hydrothermal synthesis was the best option. Over the last five years, the company has developed a range of hydrothermal reactors that give it the capability to cover the entire scale up process for new materials, from a five-liter laboratory plant, to a pilot plant of 40 liters, through to a 1000-liter main plant, which it has installed on site. This new hydrothermal synthesis capability allows the production of novel nano sized doped metal oxide materials with different functionality, and what is unique to William Blythe is the ability to produce these materials at commercial scale.
“Another area of increased focus for William Blythe is energy storage,” David adds. “We have several projects ongoing with Innovate UK as part of its Faraday Battery Challenge initiative, where we are working with different companies on active anode and cathode materials for niche and next generation cells. We have also made a significant investment into our R&D laboratory to install application capability that will allow us to manufacture coin cells, quickly getting access to performance data on new active materials.”
If William Blythe delivers on the above pipeline of projects, then it will unquestionably be enjoying significant growth in the future. In the meantime, however, the company finds itself navigating the highly disruptive year that has been 2020. “The Covid-19 pandemic obviously resulted in working practices changing quite dramatically at the beginning of the year,” David confirms. “As we were classed as an essential business we were able to continue to operate, however we moved some of our people to work from home wherever feasible, whilst being able to safely implement social distancing and other procedures on site to ensure a Covid-19 secure workplace in line with government guidelines. The safety of our workforce was our number one priority throughout, and their collective ability to keep us operational and still meet all of our customers’ deliveries on time and to specification has been fantastic to witness.”
Due to the nature of its products and the wide breadth of markets that it serves, the company has thus far been able to ride out the challenges posed by 2020 and the global pandemic. Looking ahead, there are a number of aims that it has to ensure that it pushes forward with its growth strategy. “For us, the immediate future is about delivering on products such as DURAGUARDTM; – which continues to win market share – and LUXACALÔ, while also supporting our core business of polymer additives with more application data,” Kevin states. “We have a new product coming on stream in the polymer additives field that we are excited to soon be able to share with the industry, and we believe that will drive demand in the next few years. All things considered, therefore, there is a lot of positivity and optimism within William Blythe for what is ahead.”
William Blythe Ltd
Services: Bespoke inorganic chemical products<
www.williamblythe.com
William Blythe owns all right, title and interest in the Information portrayed within the wording of the above William Blythe editorial, and all other intellectual property rights and data associated with this information without limitation. All trademarks and logos, including the LUXACALTM and DURAGUARDTM trademarks are the property of William Blythe. Copyright © 2020 William Blythe, all rights reserved.