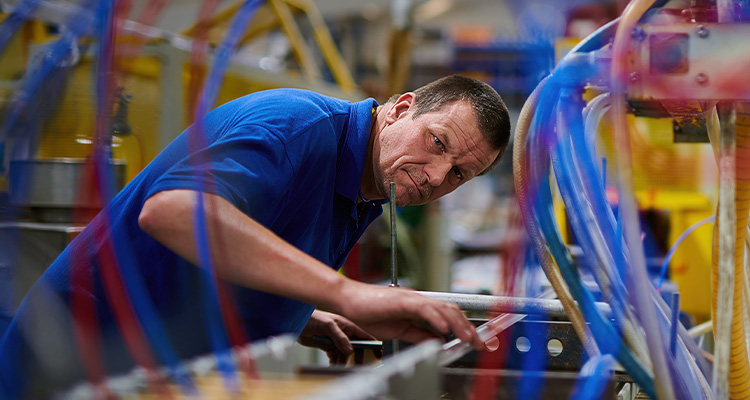
With expert craftsmanship, collaborative relationships, and a push for sustainability, Condale Plastics is shaping the future of UK manufacturing
Specialist manufacturer of bespoke plastic extrusions, Condale Plastics, is reengineering manufacturing in the Southeast of England. The company has a long legacy in the UK’s manufacturing industry, as Managing Director, Michael Stewart, begins: “Condale Plastics was originally founded in 1969. It operated as a family business for many years, up until 2022, when it was taken over by new ownership. Our job is to make bespoke plastic extrusions - meaning we don’t produce our own goods, but rather we help our clients manufacture a range of different products.
“Using our best-in-class machinery, we work with our client’s designs to manufacture high-quality custom plastic extrusions to meet their specific requirements, including plastic tubing and thermoplastics. For a long time, our primary offering was PVC, and this still makes up the majority of our extrusions. That said, we have expanded our range in recent years and can now offer products in virtually any thermoplastic.
“We supply to virtually every sector within the manufacturing industry, except for automotive. Our largest clients come from the electrical sector - as demand for electrical insulators has skyrocketed in recent years. We also work with several businesses in the leisure sector, providing components for caravans and fixed-term chalets.
“We also serve the medical and aerospace defense sectors. Our range of products is very varied and covers anything that requires plastic modelling. This allows us to diversify when necessary and keeps the business adaptable to changing industry demands.”
Years of experience, combined with industry-leading in-house capabilities, keep Condale Plastics a cut above. As Michael details: “We have our own tool-making department in-house, which means we can effectively support customers throughout the entire design process. Clients will often come to us with initial design concepts, and we work together to make the product easier to manufacture.
“With so many years of experience, we can support clients as they develop their designs and guide them through every stage to delivery of the end product. We love helping our clients create something new and we pride ourselves on our efficiency. Our facility has over 30 extrusion lines, meaning we can keep lead times relatively short and optimize everything to the client’s needs.”
To ensure it stays at the forefront of UK manufacturing, Condale Plastics embraces a collaborative approach. As Michael affirms: “We work closely with all our customers, many of whom we have partnered with for years, ensuring open communication on manufacturing advancements. We also leverage different tools, such as Teams and other digital platforms, to ensure we can consistently collaborate with our client base.
“We also take a personal approach to the process and like to balance communications with in-person meetings. It’s important that we bring clients in, so they can understand how we work and get a transparent understanding of the whole process. Having a physical presence means that development times are often quicker, and we forge the strong bonds that lead to repeat business.”
This collaborative approach wouldn’t be possible without Condale Plastics’ people. As the UK faces a skilled worker shortage, Michael discusses how the company
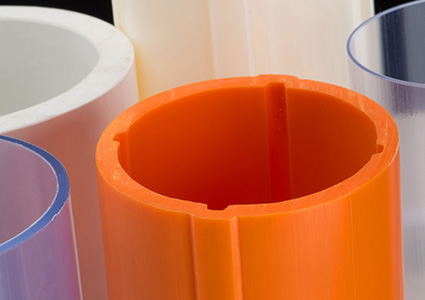
plans to support its staff: “It’s important for the safety and satisfaction of our existing staff that they are supported by a full team. We have an ageing workforce, and around two-thirds of our people are over 50, so we’re quite driven to recruit young people into the industry.
“We’re heavily invested in recruitment and creating training opportunities. We provide attractive, well-paid opportunities for young people. We’ve sponsored several students through their master’s qualifications and expanded our search internationally to find skilled workers in other countries.
“To bring in local talent, we’ve recently started working with Crawley College, a nearby trade school. In the coming months, we plan to bring in new apprentices in our maintenance team and tool-making division. Our aim is to add more of these positions over time.
“We’ve also been focused on upskilling our existing workforce with onsite training opportunities and regular vocational courses. We want to enhance their existing engineering capabilities, which will increase our share of skilled workers.”
Investing in the next generation of talent is just one way in which Michael and his team are thinking ahead. The company is also dedicated to supporting sustainability wherever possible, as Michael reveals: “We’re in the early stages of a new sustainability drive. We’ve historically been ISO 9001-accredited, but we’ve increased our energy efficiency, and now we’re ISO 14000-accredited, with the environmental standard attached.
“That said, we still want to do more in terms of sustainability. We’ve got a strong foundation internally, and our goal now is to reach Net Zero in the next few years. We already produce a significant number of products using recycled materials, as our customer base indicated a strong demand for more environmentally friendly options, and we’ve responded accordingly. In our view, becoming more eco-conscious has benefited everyone.”
It’s clear that the next chapter for Condale Plastics will be its best yet. Considering the road ahead, Michael concludes: “Customer service will continue to drive everything we do. To bring even more informed and efficient service to our client base, we’ll be investing more in our workforce’s skills and revitalizing the industry by supporting talented young engineers.”